Hole machining is more challenging than external cylindrical machining due to several factors: (1) tool size is limited by the hole diameter, leading to poor rigidity and susceptibility to bending and vibration; (2) hole dimensions depend directly on tool size, where manufacturing errors and tool wear affect precision; (3) the cutting zone is inside the workpiece, resulting in poor chip evacuation and heat dissipation, making it difficult to control precision and surface quality.
Drilling and Reaming
Drilling
Drilling is the initial process for creating holes in solid material, typically for diameters less than 80 mm. There are two methods: drill rotation or workpiece rotation. In drill rotation, asymmetry in cutting edges or insufficient drill rigidity can cause the hole centerline to deviate or become non-straight, but the diameter remains largely unchanged. In workpiece rotation, drill deviation may alter the hole diameter, but the centerline remains straight.
Common tools include twist drills, center drills, and deep-hole drills, with twist drills being the most widely used. Due to structural limitations, drills have low bending and torsional rigidity and poor centering, resulting in low precision (IT13–IT11) and higher surface roughness (Ra 50–12.5 μm). Drilling offers high material removal rates and is used for holes with lower quality requirements, such as bolt holes, thread pilot holes, or oil holes. Higher precision holes require subsequent processes like reaming, boring, or honing.
Reaming
Reaming further processes pre-drilled, cast, or forged holes to enlarge the diameter and improve quality. It serves as a pre-finishing step or final machining for less demanding holes. Reaming drills resemble twist drills but have more teeth (3–8) and no chisel edge, improving stability and cutting conditions. Reaming typically achieves IT11–IT10 precision and Ra 12.5–6.3 μm surface roughness. It is used for holes smaller than 30 mm in diameter. For larger holes (≥30 mm), pre-drilling with a smaller drill (0.5–0.7 times the final diameter) followed by reaming enhances quality and efficiency.
Reaming can also process counterbored holes or flat end faces using specialized reamers with guide posts for alignment.
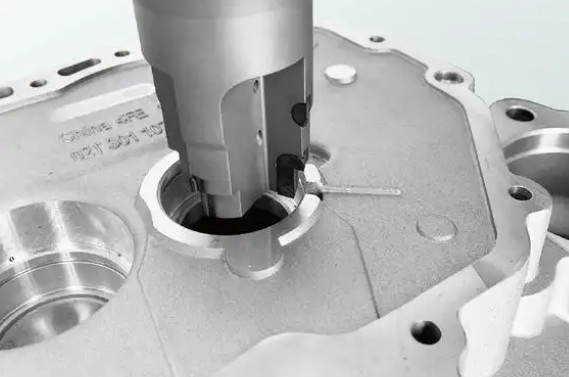
Reaming (Precision)
Reaming is a precision finishing method widely used for small holes, offering a cost-effective alternative to internal grinding or fine boring. Reamers are categorized as hand reamers (straight shank, longer working section, good guidance) or machine reamers (shank or sleeve type). They can process cylindrical or tapered holes.
Reaming allowance significantly affects quality. Excessive allowance increases reamer load, dulls cutting edges, and hinders smooth surfaces and dimensional tolerance. Insufficient allowance fails to remove prior tool marks. Typical allowances are 0.35–0.15 mm for rough reaming and 0.15–0.05 mm for finish reaming. Low cutting speeds (e.g., <8 m/min for high-speed steel reamers on steel or cast iron) and appropriate cutting fluid prevent built-up edges and ensure chip removal. Feed rates range from 0.3–1 mm/rev, depending on hole diameter.
Reaming achieves IT9–IT7 precision and Ra 3.2–0.8 μm surface roughness but cannot correct hole axis positional errors, which must be ensured by prior processes. It is unsuitable for stepped or blind holes. The drill-ream-finish ream process is typical for IT7 precision holes.
Boring
Boring enlarges preformed holes using cutting tools on boring or turning machines. It offers three methods:
- Workpiece rotates, tool feeds: Common on lathes, ensuring hole axis alignment with the workpiece’s rotation axis. Hole roundness depends on spindle accuracy, and axial geometry relies on tool feed precision. Suitable for holes requiring coaxiality with external surfaces.
- Tool rotates, workpiece feeds: Used on boring machines, with the spindle driving the tool and the table moving the workpiece.
- Tool rotates and feeds: The boring bar’s overhang varies, causing taper due to changing deflection. Longer overhangs increase spindle bending, leading to axis curvature. Suitable only for short holes.
Diamond Boring
Diamond boring uses small back engagement (0.2–0.6 mm for pre-boring, 0.1 mm for finish boring), small feed rates (0.01–0.14 mm/rev), and high cutting speeds (100–250 m/min for cast iron, 150–300 m/min for steel, 300–2000 m/min for non-ferrous metals). It achieves IT7–IT6 precision and Ra 0.4–0.05 μm surface roughness. Tools typically use cemented carbide or CBN, as diamond tools are unsuitable for ferrous metals due to carbon affinity. Diamond boring requires high-precision machines with angular contact or hydrostatic bearings and balanced rotating parts.
Boring tools include single-edge and double-edge boring bars. Boring corrects hole axis errors through multiple passes, achieving IT9–IT7 precision and high positional accuracy. It is versatile, processing various hole sizes and precision levels, especially for large, high-precision holes or hole systems.
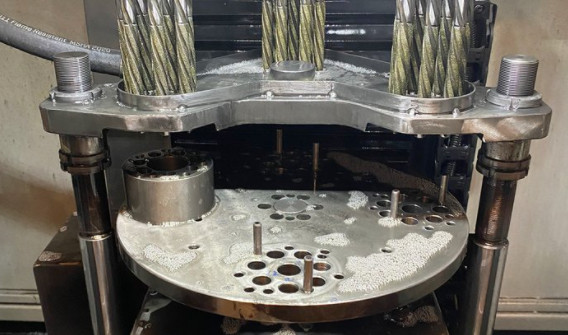
Honing
Honing uses a honing head with abrasive sticks to finish holes. The workpiece is fixed, and the honing head rotates and reciprocates. Abrasive sticks remove thin material layers, creating a crosshatched pattern. The rotation-to-reciprocation ratio ensures non-repeating abrasive paths. The crosshatch angle, influenced by reciprocation (8–20 m/min) and circumferential speeds (16–60 m/min), affects quality and efficiency (e.g., 60° for rough honing, smaller for finish honing). Adequate cutting fluid ensures chip removal and cooling.
Honing achieves IT7–IT6 precision, with roundness and cylindricity errors within 0.005–0.01 mm, and Ra 0.4–0.2 μm surface roughness. It is widely used for engine cylinder bores and hydraulic component holes but unsuitable for highly plastic non-ferrous metals or holes with keyways.
Broaching
Broaching is a high-productivity finishing method using a specialized broach on a broaching machine. The broach performs linear motion, typically requiring 3–8 teeth engaged to ensure stability and avoid surface waviness. Broaching methods include:
- Layered broaching: Removes material layer by layer using a standard broach with staggered chip-breaking grooves.
- Block broaching: Each metal layer is cut by a group of staggered teeth, each removing part of the layer.
- Combined broaching: Rough cutting uses block broaching, and finish cutting uses layered broaching for efficiency and quality.
Broaching achieves IT9–IT7 precision and Ra 6.3–1.6 μm surface roughness. The broach’s front guide ensures self-positioning, but positional accuracy with other surfaces is limited. Broaching is ideal for 10–80 mm diameter through-holes in mass production but is costly for large holes due to complex, expensive broaches.
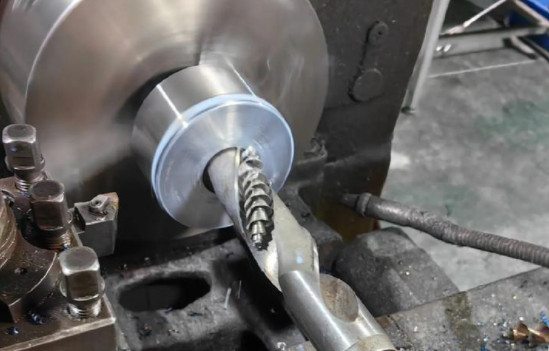
Comparison of Hole Machining Methods
Method | Precision (IT) | Surface Roughness (Ra, μm) | Applications |
---|---|---|---|
Drilling | 13–11 | 50–12.5 | Bolt holes, thread pilot holes, oil holes |
Reaming | 11–10 | 12.5–6.3 | Pre-finishing or final machining for small holes (<30 mm) |
Precision Reaming | 9–7 | 3.2–0.8 | Small, high-precision holes |
Boring | 9–7 | 3.2–0.8 | Large, high-precision holes or hole systems |
Diamond Boring | 7–6 | 0.4–0.05 | Precision holes in non-ferrous metals, cast iron |
Honing | 7–6 | 0.4–0.2 | Engine cylinder bores, hydraulic components |
Broaching | 9–7 | 6.3–1.6 | Mass production of 10–80 mm through-holes |
Key Process Parameters
Method | Cutting Speed (m/min) | Feed Rate (mm/rev) | Allowance (mm) |
---|---|---|---|
Drilling | Not specified | Not specified | Not applicable |
Reaming | Not specified | Not specified | Not specified |
Precision Reaming | <8 (steel, cast iron) | 0.3–1 | 0.35–0.15 (rough), 0.15–0.05 (finish) |
Diamond Boring | 100–250 (cast iron), 150–300 (steel), 300–2000 (non-ferrous) | 0.01–0.14 | 0.2–0.6 (pre), 0.1 (finish) |
Honing | 16–60 (circumferential), 8–20 (reciprocation) | Not applicable | Not specified |
Broaching | Low speed (linear motion) | Not applicable | Not specified |