Machining precision is a critical factor in mechanical manufacturing, determining the quality and functionality of produced parts. Precision is evaluated through tolerance grades, ranging from IT01 (highest precision) to IT18 (lowest precision). This article provides a detailed, technical overview of the highest machining precision and tolerance grades achievable for six key machining processes: turning, milling, planing, grinding, drilling, and boring. Each process is analyzed for its precision capabilities, surface roughness, and applications, ensuring a systematic and professional presentation of the subject matter.
Turning: Precision in Rotational Machining
Turning involves rotating a workpiece while a cutting tool moves linearly or along a curved path to remove material. Typically performed on lathes, turning is used to create cylindrical surfaces, end faces, conical surfaces, formed surfaces, and threads. The precision of turning varies depending on the operation type—rough, semi-finishing, or finishing—and the equipment used.
General turning achieves precision grades of IT8 to IT7, with surface roughness (Ra) ranging from 1.6 to 0.8 µm. The process is divided into three categories:
- Rough Turning: Prioritizes material removal efficiency with large cutting depths and feed rates. Precision reaches IT11, with surface roughness of Ra 20 to 10 µm.
- Semi-Finishing and Finishing Turning: Uses high speeds with smaller feed rates and cutting depths, achieving IT10 to IT7 precision and surface roughness of Ra 10 to 0.16 µm.
- Mirror Turning: Performed on high-precision lathes using finely honed diamond tools, this method processes non-ferrous metals to IT7–IT5 precision with surface roughness of Ra 0.04 to 0.01 µm.
Turning is versatile, suitable for both small and large workpieces, but achieving mirror-like finishes requires specialized tools and controlled conditions, such as vibration-free environments and precise tool alignment.
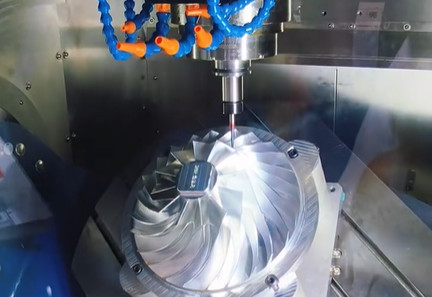
Milling: High-Efficiency Surface Machining
Milling employs rotating multi-edge tools to cut workpieces, offering high efficiency for machining flat surfaces, grooves, complex formed surfaces (e.g., splines, gears, threads), and mold profiles. Milling is categorized into climb milling (tool rotation aligns with feed direction) and conventional milling (opposite directions), each affecting surface quality and precision differently.
Milling typically achieves IT8 to IT7 precision, with surface roughness of Ra 6.3 to 1.6 µm. The process is further divided into:
- Rough Milling: Focuses on material removal, achieving IT11 to IT13 precision with surface roughness of Ra 5 to 20 µm.
- Semi-Finishing Milling: Improves surface quality to IT8–IT11 precision and Ra 2.5 to 10 µm.
- Finishing Milling: Enhances precision to IT6–IT8 with surface roughness of Ra 0.63 to 5 µm.
Milling’s versatility makes it ideal for complex geometries, but tool wear and machine rigidity can limit precision, particularly in rough milling where higher tolerances are acceptable.
Planing: Linear Cutting for Shape Machining
Planing involves a cutting tool moving in a linear, reciprocating motion relative to the workpiece, primarily used for shaping external surfaces. It is less common than milling or turning but effective for large, flat surfaces or specific profiles.
Planing achieves IT9 to IT7 precision, with surface roughness of Ra 6.3 to 1.6 µm. The process includes:
- Rough Planing: Reaches IT12 to IT11 precision with surface roughness of Ra 25 to 12.5 µm.
- Semi-Finishing Planing: Improves to IT10–IT9 precision and Ra 6.2 to 3.2 µm.
- Finishing Planing: Achieves IT8–IT7 precision with Ra 3.2 to 1.6 µm.
Planing is slower than milling due to its reciprocating motion, making it less efficient for high-volume production. However, it remains valuable for large workpieces requiring precise linear surfaces.
Grinding: Precision Finishing for Superior Surfaces
Grinding uses abrasive tools to remove material, offering high precision for semi-finishing and finishing operations. Widely used in mechanical manufacturing, grinding is critical for achieving tight tolerances and smooth surfaces.
Grinding typically reaches IT8 to IT5 precision, with surface roughness of Ra 1.25 to 0.16 µm. It is categorized as follows:
- General Grinding: Achieves Ra 1.25 to 0.16 µm, suitable for most finishing tasks.
- Precision Grinding: Reaches Ra 0.16 to 0.04 µm, used for high-accuracy components.
- Ultra-Precision Grinding: Achieves Ra 0.04 to 0.01 µm, ideal for critical applications.
- Mirror Grinding: Produces surfaces with Ra below 0.01 µm, often used in optics or high-precision molds.
Grinding’s ability to achieve ultra-low surface roughness makes it indispensable for components requiring minimal friction or high aesthetic quality, though it is time-consuming and requires skilled operation.
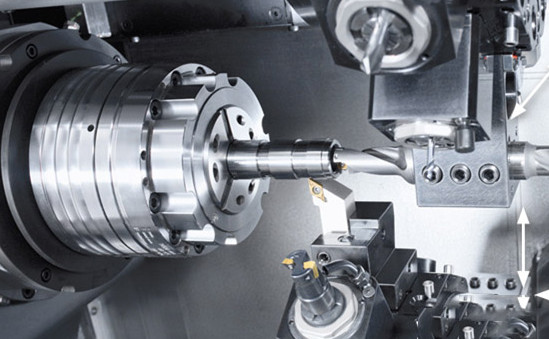
Drilling: Basic Hole Machining
Drilling creates holes using rotating tools, typically on drill presses, lathes, or milling machines. It is a fundamental process for hole-making but offers lower precision compared to other methods.
Drilling generally achieves IT10 precision with surface roughness of Ra 12.5 to 6.3 µm. Due to its limited accuracy, drilling is often followed by reaming or boring for semi-finishing or finishing. Key considerations include:
- Drill bit alignment and material hardness affect hole accuracy.
- Drilling is cost-effective for initial hole creation but unsuitable for high-precision applications without subsequent processing.
While drilling is efficient, its lower precision makes it a preparatory step in multi-stage machining processes.
Boring: Precision Hole Enlargement
Boring enlarges existing holes or refines circular contours using single-edge tools (boring bars). It is used for semi-roughing to finishing operations, offering higher precision than drilling.
Boring achieves the following precision levels:
- General Boring: Reaches IT9 to IT7 precision for steel materials, with surface roughness of Ra 2.5 to 0.16 µm.
- Precision Boring: Achieves IT7 to IT6 precision with Ra 0.63 to 0.08 µm.
Boring is essential for applications requiring precise internal diameters, such as engine cylinders or bearing housings, but requires rigid setups to minimize tool deflection.
Tolerance Grades and Surface Roughness Summary
The following table summarizes the precision and surface roughness achievable by each machining process, providing a clear comparison for manufacturing applications.
Machining Process | Precision (IT Grade) | Surface Roughness (Ra, µm) |
---|---|---|
Rough Turning | IT11 | 20–10 |
Finishing Turning | IT10–IT7 | 10–0.16 |
Mirror Turning | IT7–IT5 | 0.04–0.01 |
Rough Milling | IT11–IT13 | 5–20 |
Finishing Milling | IT6–IT8 | 0.63–5 |
Rough Planing | IT12–IT11 | 25–12.5 |
Finishing Planing | IT8–IT7 | 3.2–1.6 |
General Grinding | IT8–IT5 | 1.25–0.16 |
Mirror Grinding | IT5 or higher | Below 0.01 |
Drilling | IT10 | 12.5–6.3 |
Precision Boring | IT7–IT6 | 0.63–0.08 |
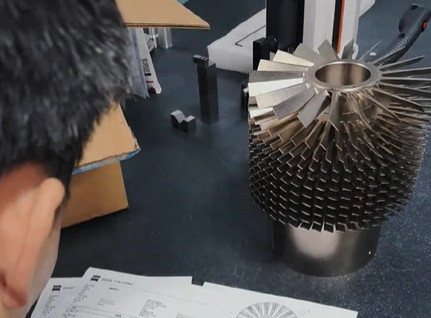
Applications and Considerations
Each machining process serves specific purposes based on its precision and surface quality capabilities. For example:
- Turning and boring are ideal for cylindrical components in automotive and aerospace industries.
- Milling excels in producing complex geometries for molds and gears.
- Grinding is critical for high-precision parts like bearings or optical components.
- Drilling and planing are suited for initial material removal or large surface machining, respectively.
Selecting the appropriate process depends on the part’s function, material, and required tolerance. For instance, IT7 is common for industrial machinery, while IT8 suffices for agricultural equipment. High-precision processes like mirror turning or grinding are reserved for specialized applications due to their cost and complexity.
Conclusion
Understanding the precision and tolerance grades of turning, milling, planing, grinding, drilling, and boring is essential for optimizing manufacturing processes. Each method offers distinct advantages in terms of accuracy, surface quality, and application suitability. By aligning the machining process with the required tolerance grade and surface roughness, manufacturers can ensure high-quality components that meet functional and economic requirements. This systematic overview provides a foundation for selecting the appropriate machining technique for specific production needs.