Magnesium, the lightest structural metal, offers unique properties that make it valuable across industries. Its low density, high strength-to-weight ratio, and excellent machinability enable its use in aerospace, automotive, electronics, and medical applications. However, machining magnesium requires careful attention due to its flammability. This guide provides a detailed overview of magnesium’s properties, applications, and CNC machining practices, including specific parameters and safety measures, to ensure efficient and safe processing.
Properties of Magnesium and Its Alloys
Magnesium, with the chemical symbol Mg and atomic number 12, has a specific gravity of 1.74, making it approximately two-thirds the density of aluminum and one-quarter that of steel. Its low density (1.74 g/cm³) is a primary reason for its use in weight-sensitive applications. Magnesium is typically alloyed with elements such as aluminum, zinc, manganese, and silicon to enhance its mechanical properties. Common alloys include AZ91D, AM60B, and AZ31B, each tailored for specific applications.
Key properties include:
- Lightweight: Magnesium’s low density makes it ideal for reducing component weight.
- High Strength-to-Weight Ratio: Alloys like AZ91D offer tensile strength comparable to aluminum, suitable for structural components.
- Excellent Machinability: Magnesium requires lower cutting forces than other metals, reducing tool wear and energy consumption.
- Thermal Conductivity: High thermal conductivity (approximately 60-90 W/m·K) aids in heat dissipation, beneficial for electronics.
- Corrosion Resistance: When alloyed and treated, magnesium exhibits good corrosion resistance, though it is susceptible to oxidation without proper coatings.
These properties make magnesium alloys versatile, but their flammability, particularly in chip or dust form, necessitates strict safety protocols during machining.
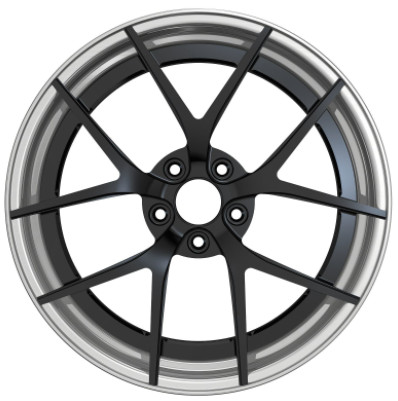
Applications of Magnesium Alloys
Magnesium alloys are used across various industries due to their lightweight and durable characteristics. Below are the primary applications:
Aerospace
Magnesium alloys, such as AZ91D and AZ31B, are used in aerospace for components like gearbox casings, seat frames, and structural parts. Their low weight contributes to fuel efficiency, a critical factor in aircraft design. For example, magnesium components can reduce aircraft weight by up to 30% compared to aluminum equivalents.
Automotive
In the automotive sector, magnesium is used for parts like instrument panel beams, transmission cases, and steering components. Alloys like AM60B provide toughness and impact resistance, ideal for safety-critical parts. Magnesium’s use in valve covers and engine blocks enhances fuel efficiency by reducing vehicle weight.
Electronics
Magnesium’s excellent heat dissipation makes it suitable for electronic devices such as laptops, cameras, and smartphones. Magnesium alloy bodies in professional-grade cameras offer durability and lightweight construction, improving portability without sacrificing strength.
Medical
Magnesium’s biocompatibility makes it a candidate for medical applications, such as orthopedic implants and cardiovascular stents. Biodegradable magnesium alloys, like WE43, eliminate the need for secondary surgeries, as they degrade safely in the body over time.
Other Applications
Magnesium is also used in sports equipment (e.g., bicycle frames), military applications (e.g., lightweight armor), and industrial tools due to its dimensional stability and vibration-damping properties.
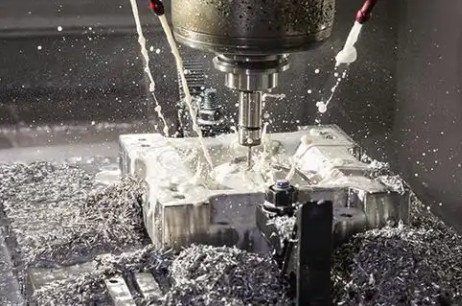
CNC Machining of Magnesium: Technical Considerations
CNC machining of magnesium is highly efficient due to its low cutting forces and excellent machinability. However, specific parameters and equipment are required to optimize performance and ensure safety. Below are the key considerations for machining magnesium alloys.
Tool Selection
Selecting the appropriate cutting tools is critical for magnesium machining. The following tools are commonly used:
- High-Speed Steel (HSS): Suitable for low to moderate production scales due to its flexibility and cost-effectiveness. HSS tools are easily re-sharpened and handle interrupted cuts well.
- Carbide Tools: Preferred for high-volume production due to their superior wear resistance and ability to maintain sharpness at high temperatures. Carbide tools with coatings like Titanium Nitride (TiN) or Titanium Aluminum Nitride (TiAlN) reduce edge buildup and improve surface finish.
- Polycrystalline Diamond (PCD): Used for precision machining, offering excellent wear resistance and minimal material buildup.
Tools should have a positive rake angle (5-15°) to reduce chip welding and a large relief angle (10-20°) to minimize friction and heat generation. Sharp tools are essential to prevent excessive heat, which can ignite magnesium chips.
Machining Parameters
Optimal machining parameters ensure efficiency and safety. The following table outlines recommended parameters for magnesium CNC machining:
Parameter | Roughing | Finishing |
---|---|---|
Cutting Speed (m/min) | 350-600 | 600-800 |
Feed Rate (mm/rev) | 0.005-0.015 | 0.002-0.010 |
Depth of Cut (mm) | 0.5-2.5 | 0.1-0.5 |
Spindle Speed (RPM) | 8000-12000 | 10000-15000 |
These parameters minimize heat generation and promote discontinuous chip formation, reducing fire risks. For thin-walled parts, lower cutting speeds (e.g., 440 m/min for roughing) are recommended to prevent oscillation and friction.
Cutting Fluids
Magnesium is often machined dry due to its high thermal conductivity, which dissipates heat effectively. However, when cooling is necessary, light mineral oils are recommended. Water-based coolants should be avoided, as they react with magnesium to produce flammable hydrogen gas. Mineral oils reduce friction and improve surface finish without increasing flammability risks.
Chip Management
Magnesium chips and dust are highly flammable and must be managed carefully. Discontinuous chips are preferred over ribbon-like chips, as they dissipate heat better and are less likely to ignite. To achieve discontinuous chips:
- Use moderate to high cutting speeds.
- Maintain low feed rates.
- Employ large cutting depths.
- Avoid tight clearance angles to reduce chip continuity.
Chips should be removed using explosion-proof vacuum systems and stored in sealed, non-combustible containers (e.g., steel drums) away from ignition sources. Wet chips must be stored in a remote location, such as an outdoor shed, to prevent spontaneous combustion.
Safety Guidelines for Magnesium Machining
Magnesium’s flammability presents significant safety considerations. Fine chips and dust can ignite easily, and magnesium-fueled fires are difficult to extinguish. Below are essential safety guidelines:
Fire Prevention
To minimize fire risks:
- Use sharp tools to reduce heat generation.
- Avoid tight clearance angles to prevent friction.
- Implement explosion-proof vacuum systems for chip removal.
- Maintain a clean workspace to prevent dust accumulation.
- Ensure adequate ventilation to disperse flammable particles.
Fire Extinguishing
Magnesium fires cannot be extinguished with water, as it exacerbates the blaze by producing hydrogen gas. Instead:
- Use Class D fire extinguishers containing sodium chloride or copper powder.
- Keep a bucket of dry sand nearby for small fires.
- Store fire extinguishers at a safe distance from machining areas.
Storage and Disposal
Magnesium chips and swarf should be:
- Stored in sealed steel drums, separate from other materials.
- Kept dry to prevent oxidation.
- Recycled through approved facilities, as magnesium is recyclable.
Regular inspections and cleaning of machining areas are essential to prevent chip accumulation.
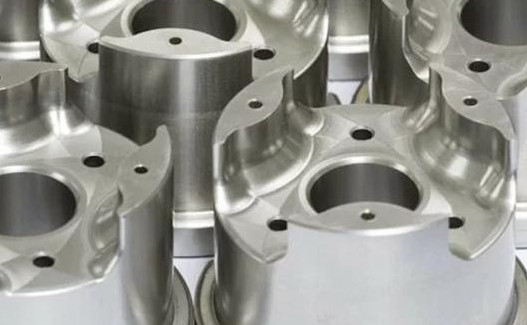
Quality Assurance in Magnesium Machining
Ensuring high-quality magnesium parts requires rigorous quality assurance processes. Key methods include:
Dimensional Inspection
Use precision instruments like calipers and micrometers to verify dimensions against engineering drawings. Critical features must meet specified tolerances (e.g., ±0.01 mm for aerospace components).
Non-Destructive Testing (NDT)
Techniques such as dye penetrant testing detect surface flaws that could compromise structural integrity. NDT is critical for safety-critical parts like automotive valve covers.
Surface Finish Evaluation
Surface roughness is measured using a profilometer to ensure compliance with design requirements (e.g., Ra 0.8-1.6 µm for high-precision parts). Finishing processes like grinding or electrochemical machining can enhance surface quality.
The following table summarizes quality assurance methods:
Method | Purpose | Tools/Techniques |
---|---|---|
Dimensional Inspection | Verify part dimensions | Calipers, Micrometers |
Non-Destructive Testing | Detect surface flaws | Dye Penetrant, Ultrasonic Testing |
Surface Finish Evaluation | Measure roughness | Profilometer |
Conclusion
Magnesium’s unique properties make it a valuable material for lightweight, high-strength components in aerospace, automotive, electronics, and medical applications. Its excellent machinability allows for efficient CNC machining, but its flammability requires strict safety measures. By selecting appropriate tools, optimizing machining parameters, and adhering to safety protocols, manufacturers can produce high-quality magnesium parts while minimizing risks. Proper chip management, fire prevention, and quality assurance ensure safe and effective machining operations, making magnesium a preferred choice for advanced engineering applications.