Rapid prototyping is a transformative approach in product development, enabling designers and engineers to create physical models quickly from digital designs. By leveraging advanced manufacturing technologies, it accelerates the design cycle, reduces costs, and enhances product quality. This article provides a comprehensive overview of the rapid prototyping process, its key advantages, and its wide-ranging applications across industries, supported by technical details and practical insights.
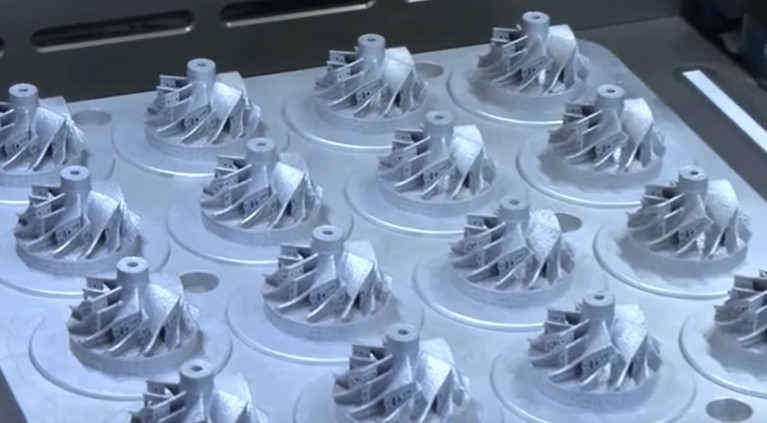
Understanding the Rapid Prototyping Process
Rapid prototyping involves creating tangible models of a design using computer-aided design (CAD) data, often through additive manufacturing techniques like 3D printing. The process allows for iterative testing and refinement, ensuring the final product meets functional and aesthetic requirements. Below is a detailed breakdown of the process steps and common techniques.
Steps in the Rapid Prototyping Process
The rapid prototyping process follows a structured workflow, typically consisting of the following steps:
- Design Creation: A 3D model is developed using CAD software, such as Autodesk Fusion or SolidWorks. The model must be a valid geometric representation, with enclosed boundary surfaces and no internal voids.
- File Conversion: The CAD model is converted into a format compatible with rapid prototyping systems, typically STL (Stereolithography). The STL file approximates the model’s geometry into triangular facets, with file sizes ranging from 1 MB for simple parts to over 100 MB for complex assemblies.
- Slicing: The STL file is processed by slicing software, which divides the model into thin layers (typically 0.05–0.25 mm thick, depending on the technology). This generates toolpaths for the manufacturing equipment.
- Fabrication: The prototype is built using additive, subtractive, or compressive manufacturing techniques. Additive methods, like 3D printing, dominate due to their speed and flexibility.
- Post-Processing: The prototype may undergo finishing processes, such as sanding, painting, or curing, to improve surface quality or mechanical properties. For example, SLA parts require UV curing to solidify resin.
- Testing and Iteration: The prototype is tested for fit, form, and function. Feedback informs design revisions, and the process repeats until the design is finalized.
Common Rapid Prototyping Techniques
Several techniques are employed in rapid prototyping, each suited to specific materials and applications. The following table summarizes the most widely used methods, their key parameters, and applications.
Technique | Description | Materials | Layer Thickness | Applications |
---|---|---|---|---|
Stereolithography (SLA) | Uses a UV laser to cure liquid resin layer by layer. | Photopolymer resins | 0.025–0.1 mm | High-detail models, medical devices, cosmetic prototypes |
Fused Deposition Modeling (FDM) | Extrudes thermoplastic filament to build parts. | ABS, PLA, PETG | 0.1–0.3 mm | Proof-of-concept models, educational tools |
Selective Laser Sintering (SLS) | Fuses powder particles using a laser. | Nylon, TPU, metals | 0.06–0.15 mm | Functional prototypes, aerospace components |
CNC Machining | Removes material from a solid block using computer-controlled tools. | Metals, plastics, wood, alloy | N/A (depends on tool) | Precision parts, rapid tooling |
Each technique offers trade-offs in terms of speed, accuracy, and material properties. For instance, SLA provides excellent surface finish but is limited to smaller parts due to resin costs, while FDM is cost-effective but has coarser resolution.
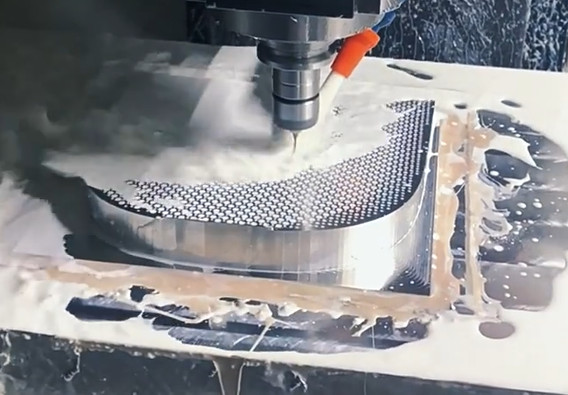
Advantages of Rapid Prototyping
Rapid prototyping offers significant benefits that streamline product development and enhance competitiveness. Below are the primary advantages, supported by technical details and real-world implications.
Accelerated Product Development
Rapid prototyping compresses the design-to-production timeline. Traditional prototyping methods, such as injection molding, require weeks to create tooling, with setup costs ranging from $5,000 to $50,000. In contrast, 3D printing can produce a prototype in hours, with costs as low as $50 for small parts using FDM. This speed enables multiple iterations within days, allowing teams to refine designs based on real-world testing.
Cost Efficiency
By identifying design flaws early, rapid prototyping reduces the need for costly revisions during production. For example, detecting a fit issue in a $100 3D-printed prototype is far cheaper than retooling a $10,000 mold. Additionally, additive manufacturing minimizes material waste, as unused powder in SLS can be recycled, reducing material costs by up to 30% compared to subtractive methods like CNC machining.
Enhanced Design Flexibility
Rapid prototyping supports complex geometries that are challenging or impossible with traditional methods. 3D printing allows for intricate lattice structures or internal channels without additional tooling. For instance, aerospace components with lightweight lattice designs can reduce weight by 20–40%, improving fuel efficiency. This flexibility encourages innovation and customization, particularly in medical implants tailored to patient anatomy.
Improved Stakeholder Communication
Physical prototypes facilitate clear communication among designers, engineers, and stakeholders. A tangible model conveys design intent more effectively than 2D drawings or digital renderings. For example, automotive companies like Ford use 3D-printed prototypes to test dashboard ergonomics, ensuring alignment with customer expectations before production.
Functional Testing
Rapid prototyping enables functional testing at a fraction of production costs. SLS prototypes made from nylon can withstand mechanical stress tests, simulating real-world conditions. This allows engineers to validate performance parameters, such as tensile strength (typically 40–60 MPa for SLS nylon) or thermal resistance, early in the design process.
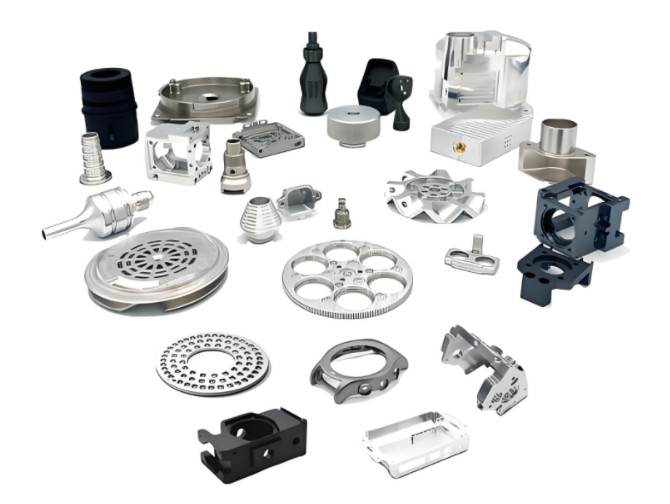
Applications of Rapid Prototyping
Rapid prototyping is employed across diverse industries, from manufacturing to healthcare. Its versatility makes it invaluable for creating prototypes, tools, and even end-use parts. Below are key applications, with specific examples and technical details.
Product Development and Design Validation
Rapid prototyping is widely used to validate product designs before mass production. Consumer electronics companies create high-fidelity prototypes to test device fit and user interaction. For instance, a smartphone prototype made with SLA can verify button placement and screen alignment, with tolerances as tight as ±0.05 mm. Iterative testing ensures the final product meets specifications.
Medical and Dental Applications
In healthcare, rapid prototyping enables personalized solutions. Custom dental implants are produced using SLA, with scans of a patient’s dental arches converted into silicone molds. These implants achieve fit accuracy within 0.1 mm, reducing surgery time. Similarly, 3D-printed anatomical models aid in preoperative planning, improving surgical outcomes by 15–20% in complex cases.
Aerospace and Automotive Components
Aerospace and automotive industries use rapid prototyping for lightweight, high-performance parts. SLS produces nylon or metal prototypes for engine components like turbine impeller, with densities reductions of up to 30% compared to machined parts. Automotive companies like Adidas employ FDM to prototype shoe soles, testing flexibility and durability (e.g., 500,000 flex cycles) before production.
Rapid Tooling and Molding
Rapid tooling involves creating molds or tool inserts using prototyping techniques. CNC machining or 3D printing produces aluminum molds in 1–3 days, compared to 2–4 weeks for traditional steel molds. These molds support small-batch production (up to 1,000 parts) with cost savings of 50–70% over conventional methods.
Educational and Research Models
Educational institutions use rapid prototyping to create models for teaching and research. FDM printers produce low-cost anatomical models or mechanical assemblies, with material costs as low as $0.02 per gram for PLA filament. These models enhance hands-on learning and experimental apparatus development.
Limitations of Rapid Prototyping
While rapid prototyping offers numerous benefits, it has limitations that must be considered for effective implementation.
- Material Constraints: Prototyping materials, such as 3D-printed resins, may not fully replicate production material properties, like impact resistance or thermal conductivity. For example, FDM ABS has a tensile strength of 30–40 MPa, compared to 70 MPa for injection-molded ABS.
- Size Restrictions: Many 3D printers have build volumes limited to 300 x 300 x 300 mm, restricting prototype dimensions. Larger parts require assembly or outsourcing to industrial systems.
- Surface Finish: Additive methods like FDM produce layered surfaces, requiring post-processing to achieve smoothness (e.g., Ra 6–12 µm for FDM vs. Ra 0.8 µm for machined parts).
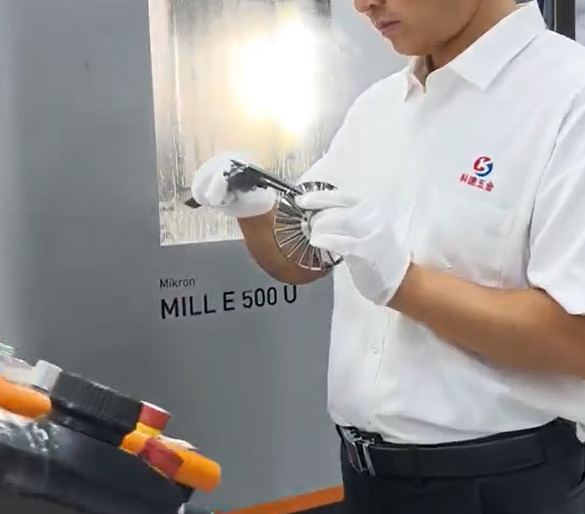
Kesu: Unleash Your Innovation with Rapid Prototyping
From vision to victory, Kesu’s rapid prototyping transforms your ideas into reality with speed, precision, and limitless possibilities. Kesu is a top-notch custom prototyping parts manufacturing provider offering high-quality and precise CNC machining services. In CNC precision machining Kesu is among the top prototypes manufacturer of machine parts all over the world and in China they are the top 5 best rapid prototyping service providers of CNC precision machining parts.
Conclusion
Rapid prototyping is a cornerstone of modern product development, offering speed, cost efficiency, and design flexibility. By leveraging techniques like 3D printing, CNC machining, and SLS, industries can create functional prototypes, validate designs, and accelerate time to market. Despite limitations in material properties and size, the process’s benefits far outweigh its constraints for most applications. Whether in aerospace, healthcare, or consumer goods, rapid prototyping empowers teams to deliver high-quality products with precision and confidence.
Rapid Prototyping FAQ
What is rapid prototyping?
Rapid prototyping is a process that quickly creates physical models from digital designs using technologies like 3D printing or CNC machining. It enables iterative testing and refinement to ensure the final product meets functional and aesthetic requirements.
What are the most common rapid prototyping techniques?
Common techniques include:
Stereolithography (SLA): Uses UV lasers to cure resin for high-detail models.
Fused Deposition Modeling (FDM): Extrudes thermoplastic filament for cost-effective prototypes.
Selective Laser Sintering (SLS): Fuses powder particles for functional parts.
CNC Machining: Removes material from a block for precision components.
How does rapid prototyping save costs?
It identifies design issues early, avoiding expensive production changes. For example, a $100 3D-printed prototype can prevent a $10,000 mold revision. Additive methods also reduce material waste by up to 30% compared to subtractive processes.
How long does it take to create a prototype?
Depending on complexity and technique, prototypes can be produced in hours to a few days. For instance, FDM can create small parts in 2–6 hours, while CNC machining may take 1–3 days for precision components.
Can rapid prototyping be used for final products?
Yes, techniques like SLS or CNC machining can produce end-use parts, especially for small-batch production or custom components like medical implants or aerospace parts.
How accurate are rapid prototypes?
Accuracy depends on the technique. SLA achieves tolerances as tight as ±0.05 mm, while FDM is less precise at ±0.1–0.3 mm. CNC machining offers even higher precision, depending on the tool.