Spring pins, also known as roll pins, tension pins, or split pins, are cylindrical fasteners used to secure components in mechanical assemblies. These pins rely on their elastic properties to create a strong, reliable connection without the need for threading or complex installation tools. This article provides a detailed, technical overview of spring pins, including their types, specifications, mechanical properties, applications, and installation methods, emphasizing their role in engineering and manufacturing.
Overview of Spring Pins
Spring pins are hollow, cylindrical fasteners made from materials such as carbon steel, stainless steel, or alloy steel. Their design includes a longitudinal slot or a coiled structure, allowing the pin to compress radially when inserted into a hole. This compression generates radial tension, securing the pin in place through frictional force against the hole walls. Spring pins are widely used in applications requiring high shear strength, alignment, or temporary fastening.
Unlike solid pins, spring pins are self-retaining due to their spring-like behavior, eliminating the need for additional locking mechanisms. They are cost-effective, easy to install, and suitable for both permanent and semi-permanent assemblies. Their ability to absorb shock and vibration makes them ideal for dynamic environments.
Types of Spring Pins
Spring pins come in two primary types: slotted spring pins and coiled spring pins. Each type has distinct design features and applications, determined by the specific requirements of the assembly.
Slotted Spring Pins
Slotted spring pins are formed from a single sheet of metal rolled into a cylinder with a longitudinal slot. The slot allows the pin to compress during insertion, creating radial pressure against the hole. These pins are simple, cost-effective, and suitable for applications requiring moderate shear strength.
Key characteristics include:
- Material: Typically carbon steel or stainless steel (e.g., AISI 420).
- Diameter Range: 1 mm to 50 mm (metric) or 1/16 inch to 3/4 inch (imperial).
- Length Range: 4 mm to 100 mm, depending on the application.
- Shear Strength: Varies by material and size, typically 2 kN to 50 kN for standard sizes.
Slotted pins are commonly used in hinges, linkages, and general-purpose fastening where ease of installation is prioritized.
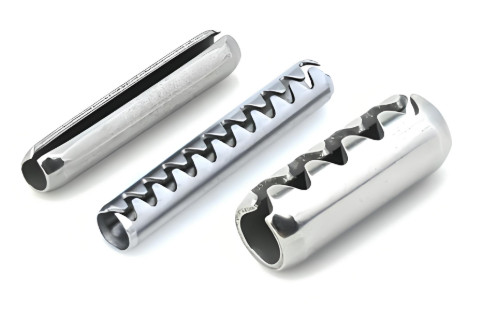
Coiled Spring Pins
Coiled spring pins, also known as spiral pins, are made from a strip of metal coiled into a spiral shape, typically with 2.25 or 2.5 coils. This design provides greater flexibility and uniform stress distribution compared to slotted pins, making them suitable for high-stress applications.
Key characteristics include:
- Material: Carbon steel, stainless steel, or specialty alloys (e.g., AISI 6150).
- Diameter Range: 0.8 mm to 20 mm (metric) or 1/32 inch to 3/4 inch (imperial).
- Length Range: 5 mm to 120 mm.
- Shear Strength: Higher than slotted pins, ranging from 3 kN to 60 kN for standard sizes.
Coiled pins are preferred in applications requiring high shear strength and fatigue resistance, such as automotive components and heavy machinery.
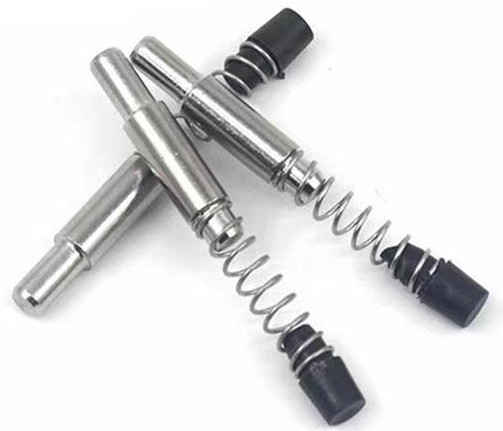
Material Specifications
The choice of material for spring pins depends on the application’s environmental conditions, load requirements, and corrosion resistance needs. The following table summarizes common materials and their properties:
Material | Composition | Yield Strength (MPa) | Corrosion Resistance | Typical Applications |
---|---|---|---|---|
Carbon Steel | C: 0.45–0.65%, Mn: 0.6–0.9% | 600–800 | Low (requires coating) | General-purpose, low-cost assemblies |
Stainless Steel (AISI 420) | Cr: 12–14%, C: 0.15–0.4% | 550–700 | Moderate to high | Marine, food processing |
Alloy Steel (AISI 6150) | Cr: 0.8–1.1%, V: 0.15% | 900–1100 | Moderate (with coating) | High-stress, automotive |
Material selection impacts the pin’s performance under shear, tension, and environmental factors. For example, stainless steel is preferred in corrosive environments, while alloy steel is chosen for high-strength applications.
Mechanical Properties
Spring pins are designed to withstand shear forces, absorb shock, and maintain positional accuracy. Their mechanical properties are determined by material, diameter, and design (slotted or coiled).
Shear Strength
Shear strength is the primary mechanical property for spring pins, as they are often used to resist lateral forces in assemblies. Shear strength depends on the pin’s diameter and material. For example, a 6 mm diameter stainless steel slotted pin may have a double shear strength of approximately 20 kN, while a coiled pin of the same size may reach 25 kN.
Fatigue Resistance
Coiled spring pins excel in fatigue resistance due to their spiral design, which distributes stress evenly. This makes them suitable for applications with cyclic loading, such as in gearboxes or suspension systems. Slotted pins, while less fatigue-resistant, are adequate for static loads.
Compression and Expansion
The radial compression of spring pins during installation creates a frictional lock. The pin’s outer diameter is typically 0.1–0.5 mm larger than the hole, ensuring a tight fit. Coiled pins offer greater elasticity, allowing them to accommodate slight variations in hole size without compromising retention.
Applications of Spring Pins
Spring pins are versatile fasteners used across industries due to their reliability and ease of use. Common applications include:
- Automotive: Securing gears, shafts, and linkages in transmissions and suspension systems.
- Aerospace: Aligning components in landing gear and control systems, where vibration resistance is critical.
- Electronics: Fastening connectors and circuit board components with small-diameter pins.
- Industrial Machinery: Positioning and retaining parts in heavy equipment, such as presses and conveyors.
- Consumer Goods: Used in hinges and locks for furniture and appliances.
The choice of slotted or coiled pins depends on the specific demands of the application, such as load, vibration, and environmental conditions.
Installation Methods
Installing spring pins is straightforward but requires attention to hole preparation and insertion techniques to ensure optimal performance.
Hole Preparation
The hole for a spring pin must be drilled to a precise diameter, typically with a tolerance of +0.05 mm to +0.2 mm, depending on the pin type. The hole should be clean, free of burrs, and perpendicular to the surface to ensure proper alignment.
Insertion Techniques
Spring pins can be inserted manually or with automated tools:
- Manual Insertion: Using a hammer or arbor press for low-volume applications. A pilot hole or chamfered edge aids insertion.
- Automated Insertion: Pneumatic or hydraulic presses are used for high-volume production, ensuring consistent force and alignment.
Coiled pins require slightly higher insertion force due to their multi-coil design, but they offer better retention in oversized or irregular holes.
Removal Considerations
Spring pins can be removed by driving them out with a punch or drift, but care must be taken to avoid hole damage. In some cases, slotted pins are easier to remove than coiled pins due to their simpler structure.
Design Considerations
When selecting spring pins for an application, engineers must consider several factors to ensure reliability and performance:
- Hole Tolerance: Slotted pins are more forgiving of hole size variations, while coiled pins require tighter tolerances for optimal performance.
- Load Requirements: Coiled pins are better suited for high shear and dynamic loads, while slotted pins are adequate for static loads.
- Environmental Conditions: Stainless steel or coated pins are necessary for corrosive environments, such as marine or chemical processing applications.
- Assembly Frequency: For applications requiring frequent disassembly, slotted pins may be preferred due to easier removal.
Proper design ensures the pin maintains its holding strength without compromising the surrounding material.
Standards and Specifications
Spring pins are manufactured to international standards to ensure consistency and compatibility. Common standards include:
Standard | Description | Region |
---|---|---|
ISO 8752 | Slotted spring pins, heavy-duty | Global |
ISO 13337 | Slotted spring pins, light-duty | Global |
ISO 8748 | Coiled spring pins, heavy-duty | Global |
ASME B18.8.2 | Slotted and coiled spring pins | North America |
These standards specify dimensions, tolerances, and mechanical properties, ensuring interoperability across industries.
Conclusion
Spring pins are essential fasteners in mechanical engineering, offering a balance of strength, simplicity, and versatility. Their ability to compress and expand ensures reliable retention in a variety of applications, from automotive to aerospace. By understanding the types, materials, mechanical properties, and installation methods, engineers can select the appropriate spring pin for their specific needs. Adhering to international standards and considering design factors further enhances their performance, making spring pins a critical component in modern manufacturing.