Stainless steel machining is a critical process in manufacturing, producing durable, corrosion-resistant components for industries like aerospace, automotive, medical, and marine. This guide provides a detailed overview of stainless steel machining, including material properties, machining methods, and challenges related to precision and complexity. The focus is on technical details, systematic approaches, and practical considerations to achieve high-quality results.
Understanding Stainless Steel as a Machining Material
Stainless steel is an iron-based alloy with at least 10.5% chromium, which provides its hallmark corrosion resistance. Additional elements like nickel, molybdenum, and carbon enhance specific properties such as strength, toughness, and machinability. The alloy’s composition varies across grades, each tailored for specific applications. For machining, understanding the material’s properties is essential to select appropriate tools, parameters, and techniques.
Key properties of stainless steel relevant to machining include:
- Corrosion Resistance: Chromium forms a passive oxide layer, protecting against rust and environmental degradation.
- High Tensile Strength: Stainless steel’s strength, ranging from 500 to 1000 MPa depending on the grade, makes it durable but challenging to cut.
- Work Hardening: Many grades, especially austenitic types, harden during machining, increasing cutting resistance.
- Low Thermal Conductivity: Heat concentrates at the cutting zone, accelerating tool wear and affecting surface quality.
- Ductility: Stainless steel’s ability to deform without breaking complicates chip formation and evacuation.
Common stainless steel grades for machining include:
Grade | Type | Key Properties | Machinability Rating | Applications |
---|---|---|---|---|
303 | Austenitic | Sulfur-enhanced, high machinability, good corrosion resistance | 70-80% | Screws, fittings, bushings |
304 | Austenitic | Good corrosion resistance, rapid work hardening | 40-50% | Cookware, chemical tanks |
316 | Austenitic | High corrosion resistance, molybdenum-added, poor machinability | 30-40% | Marine components, medical implants |
416 | Martensitic | High machinability, moderate corrosion resistance | 80-90% | Shafts, gears |
17-4 PH | Precipitation-Hardened | High strength, good corrosion resistance | 40-50% | Aerospace parts, turbine blades |
Selecting the appropriate grade depends on the application, balancing machinability with performance requirements. For example, 416 is preferred for ease of machining, while 316 is chosen for superior corrosion resistance despite its challenges.
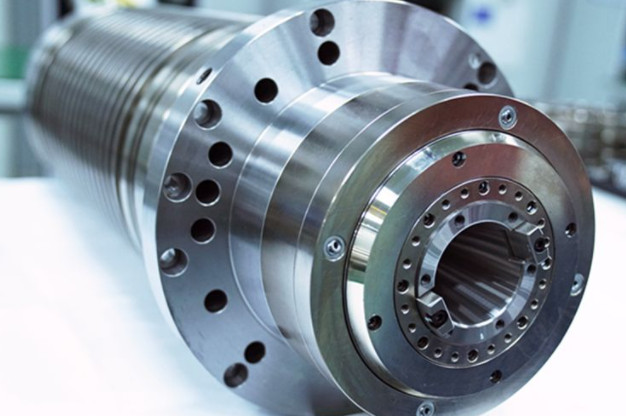
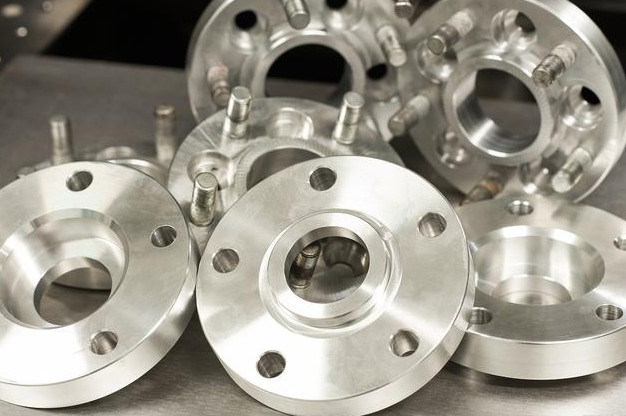
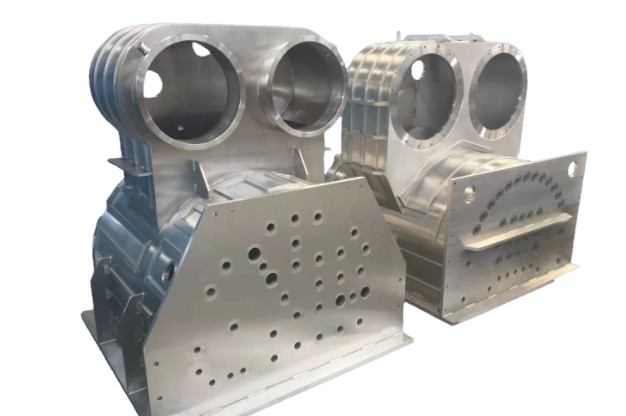
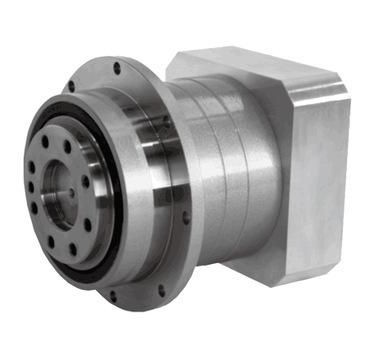
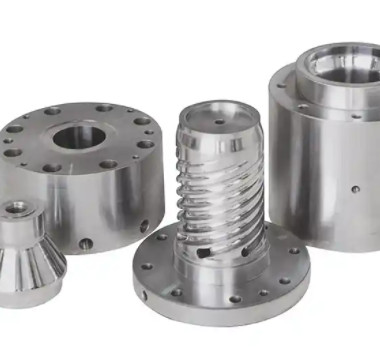
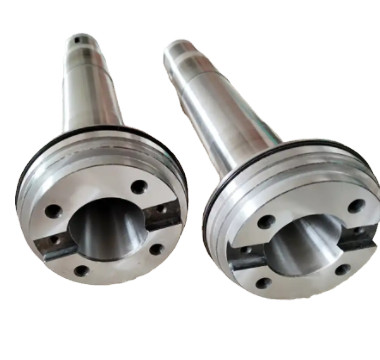
Machining Types for Stainless Steel
Stainless steel machining encompasses various methods, each suited to specific part geometries and requirements. The primary machining processes include milling, turning, drilling, grinding, and electrical discharge machining (EDM). Below is a detailed examination of each method, including their applications, tools, and parameters.
CNC Milling
CNC milling uses rotating cutting tools to remove material from a stationary stainless steel workpiece. It is ideal for creating complex shapes, slots, and surface finishes. Milling is widely used for components like brackets, housings, and intricate aerospace parts. Key considerations include:
- Tools: Carbide end mills with TiAlN coatings are recommended for their durability and heat resistance. A 4- or 5-flute end mill ensures efficient chip evacuation.
- Parameters: Typical surface feet per minute (SFM) for milling stainless steel ranges from 100 to 350, with chip loads of 0.0005" for 1/8" end mills to 0.006" for 1" end mills.
- Coolant: High-pressure coolant or minimum quantity lubrication (MQL) reduces heat buildup and prevents work hardening.
Milling excels in precision but requires careful parameter adjustment to avoid tool wear and surface defects due to stainless steel’s toughness.
CNC Turning
Turning involves a rotating workpiece and a stationary cutting tool, typically performed on CNC lathes. It is suited for cylindrical parts like shafts, pins, and bushings. Turning achieves high tolerances and smooth finishes but faces challenges with stainless steel’s work-hardening tendency. Key aspects include:
- Tools: Carbide inserts with positive rake angles minimize work hardening. Coated inserts (e.g., TiN or TiAlN) enhance tool life.
- Parameters: Cutting speeds range from 90 to 245 m/min, with feed rates of 0.06 to 0.48 mm/rev and depths of cut from 0.016 to 1.87 mm, depending on the grade.
- Setup: Secure workpiece mounting and minimal tool overhang prevent vibration and ensure precision.
Turning requires lower speeds compared to softer metals to manage heat and maintain tool integrity.
Drilling
Drilling creates precise holes in stainless steel for bolts, rivets, or fluid passages. It is often a secondary process combined with milling or turning. Challenges include chip evacuation and heat buildup. Key considerations include:
- Tools: Cobalt or carbide drill bits with polished surfaces reduce friction. Split-point geometry aids chip breaking.
- Parameters: Cutting speeds of 50-100 m/min and feed rates of 0.05-0.2 mm/rev are typical. Peck drilling cycles prevent chip clogging.
- Coolant: Continuous coolant flow is critical to manage heat and extend drill life.
Drilling stainless steel demands robust equipment to handle the material’s hardness and avoid tool breakage.
Grinding
Grinding uses abrasive wheels to achieve fine surface finishes and tight tolerances, often for finishing operations. It is suitable for stainless steel parts requiring high precision, such as medical instruments. Key aspects include:
- Tools: Aluminum oxide or silicon carbide wheels are effective. Wheel speed must be controlled to avoid tempering the material.
- Parameters: Surface speeds of 20-30 m/s and light depths of cut (0.01-0.05 mm) ensure quality finishes.
- Coolant: Continuous coolant prevents overheating, which can compromise corrosion resistance.
Grinding is labor-intensive but essential for applications demanding exceptional surface quality.
Electrical Discharge Machining (EDM)
EDM uses electrical pulses to erode material, ideal for complex shapes and thin-walled parts. It includes sinker EDM for intricate cavities and wire EDM for precise cuts. Key considerations include:
- Tools: Copper or graphite electrodes for sinker EDM; brass or zinc-coated wires for wire EDM.
- Parameters: High-frequency pulses (10-100 kHz) and low voltage (50-200 V) ensure precision.
- Limitations: EDM is slower and limited to conductive materials, making it suitable for specialized applications.
EDM excels in precision but is less efficient for high-volume production.
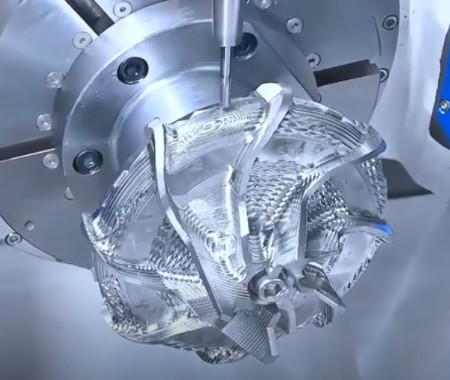
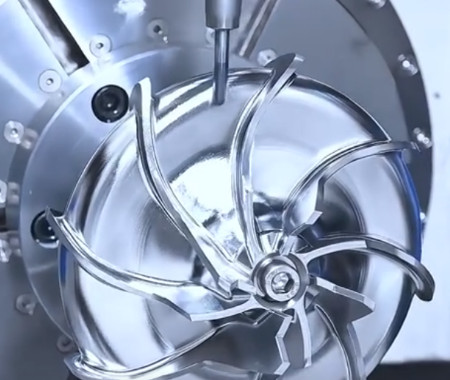
Difficulties in Stainless Steel Machining
Machining stainless steel presents several challenges due to its material properties. These difficulties impact precision, complexity, and overall machining efficiency. Below are the primary obstacles and strategies to address them.
Work Hardening
Stainless steel, particularly austenitic grades like 304 and 316, hardens rapidly during machining. This increases cutting resistance, leading to tool wear and potential surface defects. To mitigate work hardening:
- Use sharp tools with positive rake angles to reduce cutting forces.
- Maintain low cutting speeds to minimize heat generation.
- Employ chip-breaking cycles to manage chip formation and prevent adhesion.
Low Thermal Conductivity
Stainless steel’s low thermal conductivity causes heat to concentrate at the cutting zone, accelerating tool wear and risking material deformation. Strategies include:
- Using high-pressure coolant or MQL to dissipate heat effectively.
- Pausing machining if overheating occurs to allow cooling.
- Selecting coated carbide tools to withstand high temperatures.
Precision and Complexity Challenges
Achieving tight tolerances (e.g., ±0.0005") and complex geometries is difficult due to stainless steel’s toughness and tendency to vibrate. Key considerations include:
- Tool Deflection: Vibrations from tool chatter can lead to dimensional inaccuracies. Anti-vibration tool holders and rigid machine setups are essential.
- Complex Geometries: Multi-axis CNC machines (4- or 5-axis) enable intricate tool paths, reducing setups and improving accuracy.
- Surface Finish: Rapid work hardening and built-up edge (BUE) formation can degrade surface quality. Fine-tuned parameters and sharp tools are critical.
For example, machining 316 stainless steel for medical implants requires specialized tools and low feed rates to maintain precision while avoiding surface imperfections.
Tool Wear and Breakage
Stainless steel’s hardness and carbide content accelerate tool wear, particularly in high-carbon grades. This increases downtime and costs. Mitigation strategies include:
- Using carbide or cobalt tools with wear-resistant coatings (e.g., TiAlN).
- Regularly inspecting and replacing worn tools to prevent breakage.
- Optimizing feed rates and depths of cut to reduce cutting forces.
Chip Formation and Evacuation
Stainless steel’s ductility leads to long, stringy chips that can clog tools and damage workpieces. Effective chip management involves:
- Using chip breakers on cutting tools to produce short, manageable chips.
- Employing peck drilling or trochoidal milling to facilitate chip removal.
- Applying lubricants to reduce friction and wash away residue.
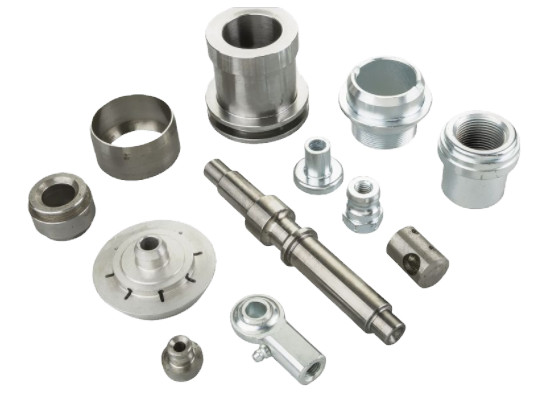
Recommended Machining Parameters
Optimizing machining parameters is critical for efficiency and quality. The following table provides general guidelines for key stainless steel grades and machining processes.
Process | Grade | Cutting Speed (m/min) | Feed Rate (mm/rev) | Depth of Cut (mm) |
---|---|---|---|---|
Milling | 303 | 120-200 | 0.05-0.15 | 0.5-2.0 |
Milling | 316 | 90-150 | 0.03-0.10 | 0.3-1.5 |
Turning | 304 | 100-180 | 0.06-0.20 | 0.5-2.5 |
Turning | 416 | 150-245 | 0.08-0.25 | 0.5-3.0 |
Drilling | 17-4 PH | 50-100 | 0.05-0.15 | 0.2-1.0 |
These parameters should be adjusted based on machine capabilities, tool condition, and part complexity. Always consult tool manufacturer recommendations and conduct test cuts for optimization.
Best Practices for Stainless Steel Machining
To achieve high-quality results, machinists should follow these best practices:
- Tool Selection: Use carbide or cobalt tools with appropriate coatings. Ensure tools are sharp and replaced promptly when worn.
- Coolant Use: Apply high-pressure coolant or MQL to manage heat and improve tool life.
- Machine Rigidity: Ensure robust machine setups to minimize vibration and tool chatter.
- Parameter Optimization: Adjust speeds, feeds, and depths of cut based on the stainless steel grade and machining process.
- Regular Maintenance: Inspect tools and machines frequently to prevent defects and downtime.
By adhering to these practices, machinists can overcome the inherent challenges of stainless steel and produce precise, durable components.

Kesu: Precision & Complex Stainless Steel Machining Solutions
Elevate your manufacturing with Kesu’s expert stainless steel machining services. We deliver high-precision components with unmatched durability, tailored to your specifications. From complex geometries to tight tolerances, our advanced CNC technology and skilled team ensure superior quality and efficiency for aerospace, medical, and industrial applications. Trust Kesu for reliable, cost-effective machining solutions that meet your toughest stainless steel machining challenges.
Conclusion
Stainless steel machining is a complex but essential process for creating high-performance parts across various industries. Understanding the material’s properties, selecting appropriate machining methods, and addressing difficulties like work hardening, heat buildup, and precision challenges are critical for success. By optimizing tools, parameters, and techniques, machinists can achieve high-quality results while minimizing costs and downtime. This guide provides a foundation for effective stainless steel machining, emphasizing technical precision and systematic approaches.