Stainless steel and titanium are widely used metals in industries ranging from manufacturing to medical applications. Each material has distinct properties that make it suitable for specific uses. This article provides a detailed, technical comparison of stainless steel and titanium, focusing on their mechanical, physical, chemical, and processing characteristics, as well as their applications and limitations. The analysis is structured to offer a clear, systematic understanding of the differences between these materials.
Mechanical Properties
The mechanical properties of a material determine its performance under stress, strain, and wear. Below is a detailed comparison of the mechanical characteristics of stainless steel and titanium.
Strength and Hardness
Stainless steel, an iron-based alloy with at least 10.5% chromium, is known for its strength and durability. Its mechanical properties vary by grade (e.g., 304, 316, or 440). For instance, 304 stainless steel has a tensile strength of approximately 515-620 MPa and a yield strength of around 205 MPa. Its hardness, measured on the Rockwell B scale, typically ranges from 70-90 HRB.
Titanium, particularly Grade 5 (Ti-6Al-4V), offers a higher tensile strength of 900-1000 MPa and a yield strength of about 830 MPa. Despite its strength, titanium is less hard than some stainless steel grades, with a Rockwell C hardness of approximately 36 HRC. This makes titanium more susceptible to surface scratches but less likely to deform under high stress.
Strength-to-Weight Ratio
Titanium excels in its strength-to-weight ratio due to its lower density (4.5 g/cm³) compared to stainless steel (7.8-8 g/cm³). This makes titanium ideal for applications where weight reduction is critical, such as aerospace components. Titanium’s specific strength (strength divided by density) is approximately 200 kN·m/kg, while stainless steel’s is around 65-80 kN·m/kg for common grades.
Ductility and Formability
Stainless steel is generally more ductile than titanium, allowing it to be easily formed into complex shapes. Austenitic grades like 304 and 316 exhibit elongation at break values of 40-60%. Titanium, while still formable, has lower ductility (elongation at break of 10-15% for Grade 5), requiring more precise manufacturing techniques, such as hot forming, to avoid cracking.
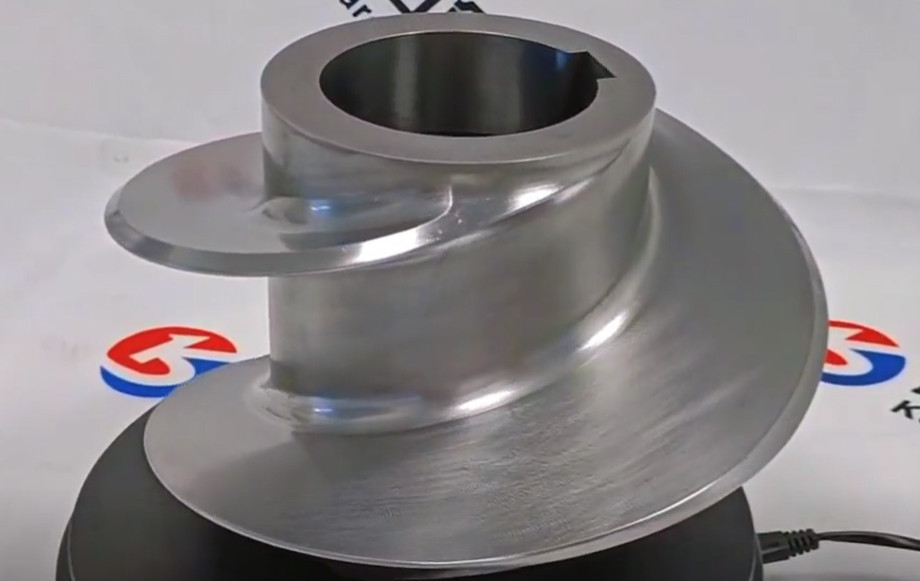
Physical and Chemical Properties
The physical and chemical properties of stainless steel and titanium significantly influence their performance in various environments.
Corrosion Resistance
Stainless steel’s corrosion resistance comes from its chromium content, which forms a passive oxide layer on the surface. Grades like 316, with added molybdenum (2-3%), offer superior resistance to pitting and crevice corrosion in chloride-rich environments, such as marine settings. However, stainless steel can corrode under extreme conditions, such as prolonged exposure to acidic or high-salinity environments.
Titanium’s corrosion resistance is exceptional due to its naturally forming titanium dioxide (TiO₂) layer, which is highly stable and self-healing. Titanium resists corrosion in seawater, acids, and aggressive chemicals like chlorine. Its corrosion rate in seawater is less than 0.01 mm/year, compared to 0.1-0.5 mm/year for stainless steel, depending on the grade.
Density and Weight
Titanium’s density (4.5 g/cm³) is significantly lower than that of stainless steel (7.8-8 g/cm³), making it approximately 40% lighter for the same volume. This is a critical factor in applications like aerospace, automotive, and medical implants where weight reduction is essential.
Thermal and Electrical Conductivity
Stainless steel has moderate thermal conductivity (15-20 W/m·K for 304 stainless steel) and electrical conductivity, making it suitable for applications like cookware and heat exchangers. Titanium has low thermal conductivity (7-10 W/m·K for Grade 5) and poor electrical conductivity, which can be advantageous in applications requiring thermal insulation but limiting in electrical applications.
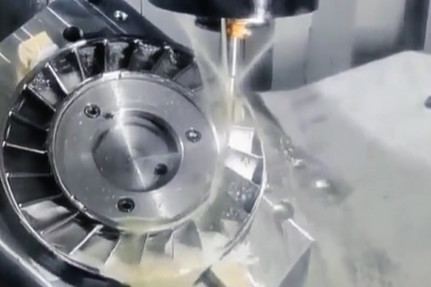
Processing Characteristics
The processing characteristics of stainless steel and titanium significantly affect their manufacturability, cost, and application suitability.
Machining
Stainless steel is relatively easy to machine, though its work-hardening properties can pose challenges. Austenitic grades like 304 and 316 tend to harden during machining, requiring sharp tools, adequate cooling, and slower cutting speeds to prevent tool wear. Typical machining parameters include cutting speeds of 30-60 m/min and feed rates of 0.1-0.3 mm/rev for turning operations.
Titanium is notoriously difficult to machine due to its low thermal conductivity and high strength. Heat generated during machining concentrates at the tool-workpiece interface, leading to rapid tool wear and potential workpiece damage. Machining titanium requires low cutting speeds (15-30 m/min), high-pressure coolant, and specialized tools like carbide or coated inserts. This increases machining time and cost compared to stainless steel.
Welding
Stainless steel is readily weldable using common techniques like TIG (Tungsten Inert Gas) and MIG (Metal Inert Gas) welding. Austenitic grades are particularly forgiving, though care must be taken to avoid sensitization (chromium carbide precipitation) in high-temperature welds, which can reduce corrosion resistance. Weld Imperfection Rates for stainless steel are typically low, around 1-3% for skilled operations.
Titanium welding requires strict control due to its reactivity with oxygen, nitrogen, and hydrogen at high temperatures. Techniques like TIG welding in an inert gas environment (e.g., argon shielding) are necessary to prevent contamination. Weld Imperfection Rates for titanium can be higher (5-10%) if not properly controlled, and post-weld heat treatment may be required to restore properties.
Forming and Fabrication
Stainless steel’s high ductility makes it suitable for forming processes like bending, stamping, and deep drawing. It can be cold-worked or hot-worked, with common forming temperatures for hot working ranging from 900-1200°C. Its versatility allows for complex shapes in applications like automotive panels or kitchen appliances.
Titanium’s lower ductility and higher strength require specialized forming techniques, often at elevated temperatures (600-900°C for hot forming). Cold forming is possible but limited due to titanium’s tendency to spring back or crack. Fabrication of titanium components often involves precision processes like superplastic forming, increasing production complexity and cost.
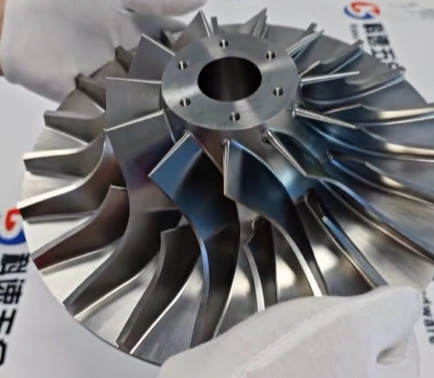
Applications
The distinct properties and processing characteristics of stainless steel and titanium lead to their use in different industries.
Stainless Steel Applications
Stainless steel is widely used in construction, automotive, and consumer goods due to its affordability, strength, and corrosion resistance. Common applications include:
- Kitchen appliances (e.g., sinks, cutlery, cookware)
- Architectural structures (e.g., railings, cladding)
- Industrial equipment (e.g., piping, tanks)
- Medical instruments (e.g., surgical tools)
Its ease of fabrication and lower cost make it a go-to material for large-scale manufacturing.
Titanium Applications
Titanium’s high strength-to-weight ratio, corrosion resistance, and biocompatibility make it ideal for specialized applications, including:
- Aerospace components (e.g., aircraft frames, engine parts)
- Medical implants (e.g., hip replacements, dental implants)
- Marine equipment (e.g., propellers, submarine hulls)
- High-performance sports equipment (e.g., bicycle frames)
Its biocompatibility is particularly valuable in medical applications where inertness is critical.
Cost and Availability
Cost and availability are critical factors in material selection.
Material Cost
Stainless steel is significantly more affordable, with costs ranging from $1-5 per kilogram for common grades like 304 or 316. Titanium, particularly high-purity or alloyed grades like Ti-6Al-4V, costs $20-50 per kilogram or more, depending on market conditions and processing requirements.
Processing Costs
Stainless steel’s ease of machining, welding, and forming results in lower processing costs. Standard equipment and techniques are sufficient, and its widespread use ensures cost-effective supply chains. Titanium’s processing challenges, including specialized tools, inert environments for welding, and high-temperature forming, significantly increase production costs. For example, machining titanium can take 2-3 times longer than stainless steel for similar components.
Availability
Stainless steel is widely available in various grades, forms (e.g., sheets, bars, tubes), and finishes, making it a staple in global supply chains. Titanium is less abundant, more expensive to extract, and requires specialized processing, limiting its availability and increasing lead times.
Limitations and Considerations
Both materials have limitations that must be considered during material selection.
Stainless Steel Limitations
Stainless steel’s higher density makes it less suitable for weight-sensitive applications. It is also susceptible to corrosion in extreme environments, such as prolonged exposure to highly acidic or chloride-rich conditions, leading to pitting or stress corrosion cracking in lower grades. During machining, work-hardening can increase tool wear and processing time.
Titanium Limitations
Titanium’s high cost and processing difficulties are its primary drawbacks. Its lower hardness makes it prone to surface scratches, which can be a concern in aesthetic applications. Machining and welding challenges, such as tool wear and reactivity at high temperatures, require specialized equipment and expertise, increasing production complexity.
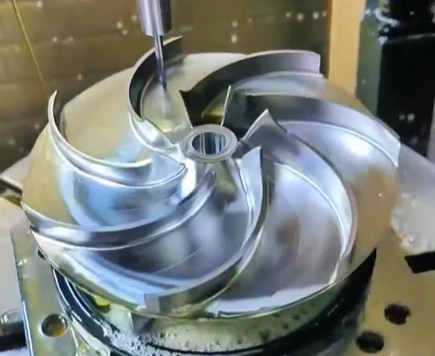
Technical Specifications Comparison
The following table summarizes the key properties of stainless steel (Grade 304) and titanium (Grade 5, Ti-6Al-4V).
Property | Stainless Steel (304) | Titanium (Grade 5) |
---|---|---|
Density (g/cm³) | 7.8-8.0 | 4.5 |
Tensile Strength (MPa) | 515-620 | 900-1000 |
Yield Strength (MPa) | 205 | 830 |
Hardness (Rockwell) | 70-90 HRB | 36 HRC |
Corrosion Rate in Seawater (mm/year) | 0.1-0.5 | <0.01 |
Thermal Conductivity (W/m·K) | 15-20 | 7-10 |
Cost ($/kg) | 1-5 | 20-50 |
Machining Speed (m/min) | 30-60 | 15-30 |
Choosing the Right Material
Selecting between stainless steel and titanium depends on the application’s requirements. Stainless steel is preferred for cost-sensitive projects, general-purpose manufacturing, and applications where weight is not a primary concern. Its ease of processing makes it suitable for high-volume production. Titanium is better suited for high-performance applications requiring lightweight materials, superior corrosion resistance, or biocompatibility, despite its higher cost and processing challenges.
For example, in marine environments, titanium’s corrosion resistance makes it ideal for components exposed to seawater, while stainless steel may suffice for less aggressive conditions. In aerospace, titanium’s strength-to-weight ratio is critical, whereas stainless steel is often used in ground-based industrial equipment due to its affordability and ease of fabrication.
Conclusion
Stainless steel and titanium are exceptional materials with distinct advantages and limitations. Stainless steel offers affordability, versatility, and good corrosion resistance, with straightforward processing characteristics, making it suitable for a wide range of applications. Titanium provides superior strength-to-weight ratio, excellent corrosion resistance, and biocompatibility but requires specialized processing techniques, increasing costs. By understanding their mechanical, physical, chemical, and processing properties, engineers and designers can make informed decisions to meet project demands.