Tesla, Inc. produces a range of electric vehicles (EVs) designed to meet diverse market needs, from luxury sedans to heavy-duty trucks. Each vehicle class requires specific precision machining technologies, materials, and prototyping methods to achieve high performance, durability, and efficiency. This article provides a systematic and technical overview of Tesla’s vehicle classifications and the precision machining processes involved in their production, focusing on materials, prototyping, and manufacturing techniques. The content is structured to detail each vehicle class and the associated technologies without speculative trends or challenges, ensuring a professional and technical focus.
Tesla Vehicle Classifications
Tesla’s vehicle lineup is categorized based on vehicle type, market segment, and functionality. The classifications include luxury sedans, crossover SUVs, semi-trucks, autonomous vehicles, and sports cars. Each class has unique design requirements, influencing the choice of materials, prototyping methods, and precision machining technologies. Below is a detailed breakdown of each vehicle class, including their specifications and manufacturing considerations.
Luxury Sedans: Model S and Model 3
The Model S and Model 3 are Tesla’s luxury and mid-range sedans, respectively, designed for performance and efficiency. The Model S, a full-size sedan, features a dual-motor, all-wheel-drive layout with a range of up to 405 miles (EPA estimated). The Model 3, a compact sedan, offers single- or dual-motor configurations with a range of up to 341 miles. Both models utilize lightweight aluminum bodies reinforced with boron steel for structural integrity.
Materials: The Model S and Model 3 use aluminum extrusions for body panels, formed from 6000-series aluminum alloys (e.g., 6061-T6, yield strength ~240 MPa) for high strength-to-weight ratio. Boron steel (e.g., 22MnB5, tensile strength ~1500 MPa) reinforces critical areas like the A-pillars and roof rails. Interior components include vegan leather (PVC-polyurethane blend) for seats and dashboards, and glass for panoramic roofs.
Prototyping: Prototyping for these sedans involves computer-aided design (CAD) modeling using software like CATIA or SolidWorks to create 3D models with tolerances of ±0.1 mm. Rapid prototyping employs additive manufacturing (e.g., fused deposition modeling with ABS or nylon) for interior components and CNC machining for metal parts. Functional prototypes are tested for aerodynamics (drag coefficient ~0.208 for Model S) and crashworthiness.
Precision Machining: CNC milling and turning are used for aluminum body panels, with 5-axis CNC machines achieving tolerances of ±0.01 mm for complex geometries like suspension mounts. Laser cutting (CO2 or fiber lasers, power ~4 kW) shapes boron steel reinforcements with edge accuracy of ±0.05 mm. Robotic welding (e.g., resistance spot welding) joins aluminum and steel components, ensuring structural rigidity.
Crossover SUVs: Model X and Model Y
The Model X, a mid-size luxury crossover SUV, and Model Y, a compact crossover, cater to families and cost-conscious consumers. The Model X features falcon-wing doors and a range of up to 348 miles, while the Model Y shares ~75% of its components with the Model 3 and offers a range of up to 326 miles. Both vehicles use a combination of aluminum and steel for structural efficiency.
Materials: The Model X and Model Y employ 6000-series aluminum for body panels and chassis components, with high-strength steel (e.g., DP980, tensile strength ~980 MPa) for subframes. The Model X’s falcon-wing doors require lightweight carbon-fiber-reinforced polymers (CFRP, modulus ~230 GPa) for hinges. Battery packs use lithium-ion 2170 cells (energy density ~260 Wh/kg) for Model 3 and Y, and 18650 cells for older Model X units.
Prototyping: Prototyping involves 3D modeling with parametric CAD for iterative design adjustments. Additive manufacturing creates CFRP hinge prototypes using stereolithography (SLA) with photopolymer resins. Metal prototypes for subframes are produced via CNC machining or investment casting, with dimensional accuracy of ±0.02 mm. Crash testing validates structural integrity (e.g., IIHS Top Safety Pick+ for Model Y).
Precision Machining: Giga Press die-casting machines (clamping force ~6000 tons) produce large aluminum underbody castings, reducing part count by ~70 for Model Y. CNC machining refines casting surfaces to tolerances of ±0.015 mm. Laser welding (fiber lasers, power ~6 kW) joins aluminum castings to steel subframes, ensuring seam strength of ~10 kN/cm. The falcon-wing doors require precision milling for CFRP components with surface finish Ra ~0.8 µm.

Semi-Truck: Tesla Semi
The Tesla Semi is a Class 8 electric truck designed for heavy-duty transport, featuring a tri-motor, rear-wheel-drive layout and a range of ~500 miles. It is built to handle payloads up to 80,000 lbs (gross vehicle weight rating).
Materials: The Semi’s exoskeleton uses high-strength stainless steel (e.g., 301 SS, tensile strength ~1200 MPa) for durability. Aluminum alloys (e.g., 7075-T6, yield strength ~500 MPa) are used for lightweight components like suspension arms. The battery pack employs 4680 lithium-ion cells (energy density ~300 Wh/kg) for enhanced range.
Prototyping: Prototyping involves finite element analysis (FEA) to simulate load-bearing capacity (e.g., maximum stress ~400 MPa). 3D-printed prototypes (using powder bed fusion with stainless steel powder) test exoskeleton components. CNC-machined aluminum prototypes ensure precise fit for suspension interfaces (tolerances ±0.05 mm).
Precision Machining: CNC machining (5-axis mills) produces stainless steel exoskeleton parts with tolerances of ±0.02 mm. Laser cutting (fiber lasers, power ~10 kW) shapes thick steel plates (4–5 mm) with edge accuracy of ±0.03 mm. Robotic welding (MIG/TIG) joins exoskeleton sections, achieving weld strength of ~15 kN/cm. Battery pack assembly uses automated precision placement systems for 4680 cells with alignment accuracy of ±0.1 mm.
Autonomous Vehicles: Cybercab and Robovan
The Tesla Cybercab (Robotaxi) is a two-passenger, fully autonomous vehicle with no steering wheel or pedals, unveiled as a concept in October 2024. The Robovan is an autonomous electric van designed for up to 20 passengers, also in development. Both aim for full autonomy using advanced sensor suites.
Materials: The Cybercab uses a lightweight aluminum chassis (6061-T6) and composite panels (CFRP, modulus ~200 GPa) for weight reduction. The Robovan employs high-strength steel (DP1180, tensile strength ~1180 MPa) for structural components and aluminum for non-load-bearing parts. Sensor housings use polycarbonate (impact strength ~850 J/m).
Prototyping: Prototyping relies on digital twins for virtual testing of autonomous systems. 3D printing (multi-jet fusion with nylon) creates sensor housing prototypes with tolerances of ±0.1 mm. CNC machining produces aluminum chassis components for functional testing. Iterative prototyping validates sensor integration (e.g., LiDAR accuracy ~2 cm).
Precision Machining: CNC milling (4-axis) machines aluminum chassis parts with tolerances of ±0.01 mm. Laser cutting shapes composite panels with precision of ±0.05 mm. Automated assembly systems align sensors with positional accuracy of ±0.02 mm. Surface finishing (anodizing, Ra ~0.4 µm) enhances aluminum durability.
Sports Car: Tesla Roadster
The original Tesla Roadster (2008–2012) was a two-seater sports car based on the Lotus Elise chassis, with a range of ~245 miles. The upcoming Roadster 2.0, still in development, promises a range of ~620 miles and a top speed exceeding 250 mph.
Materials: The Roadster 2.0 uses a carbon-fiber monocoque (modulus ~300 GPa) for weight reduction and rigidity. Aluminum alloys (7075-T6) form suspension components, and lithium-ion 4680 cells power the vehicle. Glass and polycarbonate are used for aerodynamic windows.
Prototyping: Prototyping involves SLA 3D printing for carbon-fiber body panels and CNC machining for aluminum suspension parts (tolerances ±0.02 mm). FEA simulates aerodynamic performance (drag coefficient ~0.20). Functional prototypes test battery integration and thermal management.
Precision Machining: 5-axis CNC milling machines carbon-fiber components with tolerances of ±0.015 mm. Laser cutting (fiber lasers, power ~5 kW) shapes monocoque panels with edge accuracy of ±0.03 mm. Automated bonding systems apply adhesives (shear strength ~25 MPa) for carbon-fiber assembly. Battery pack machining ensures cell alignment within ±0.05 mm.
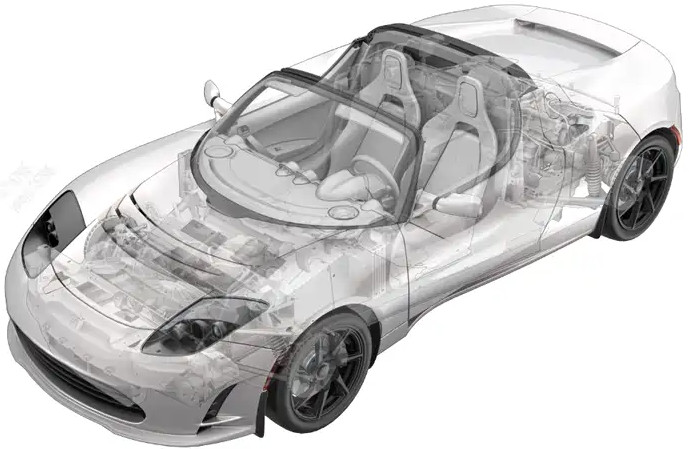
Precision Machining Technologies Across Tesla Vehicles
Precision machining is critical to Tesla’s manufacturing process, enabling high-quality components with tight tolerances. The following technologies are applied across vehicle classes, tailored to specific material and design requirements.
CNC Machining
CNC machining (milling, turning, and drilling) is used for aluminum, steel, and composite components. 5-axis CNC machines achieve complex geometries with tolerances of ±0.01–0.05 mm, critical for suspension mounts, battery pack housings, and sensor interfaces. For example, the Model Y’s aluminum castings are machined to a surface finish of Ra ~0.8 µm for structural integrity.
Giga Press Die-Casting
Tesla’s Giga Press machines (clamping force 5500–6200 tons) produce large aluminum castings for Model Y and Cybertruck underbodies, reducing part count by up to 70. Post-casting CNC machining refines surfaces to tolerances of ±0.015 mm, ensuring precise fitment. The process uses 6000-series aluminum alloys with a yield strength of ~240 MPa.
Laser Cutting and Welding
Fiber laser cutting (power 4–10 kW) shapes aluminum, steel, and composite panels with edge accuracy of ±0.03–0.05 mm. Laser welding (fiber lasers, power ~6 kW) joins dissimilar materials (e.g., aluminum to steel) with seam strength of ~10–15 kN/cm, used in Model S and Semi exoskeleton assembly.
Additive Manufacturing
Additive manufacturing (e.g., SLA, multi-jet fusion) supports prototyping of interior components, sensor housings, and complex geometries. Materials include nylon, ABS, and photopolymer resins with tolerances of ±0.1 mm. For production, limited additive manufacturing is used for low-volume, high-complexity parts like Cybercab sensor mounts.
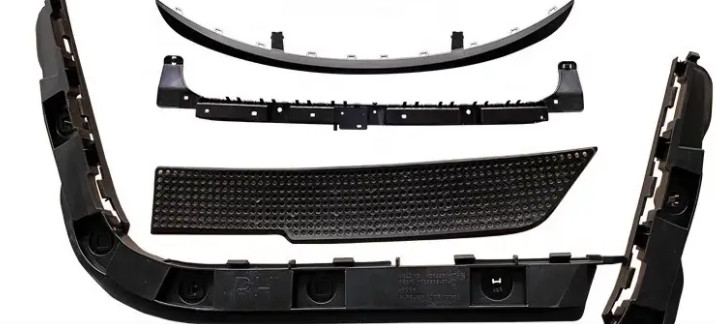
Material and Prototyping Summary
The following table summarizes the materials and prototyping methods used across Tesla’s vehicle classes, highlighting their specific applications.
Vehicle Class | Primary Materials | Prototyping Methods |
---|---|---|
Luxury Sedans (Model S, Model 3) | Aluminum (6061-T6), Boron Steel (22MnB5), Vegan Leather | CAD Modeling, FDM 3D Printing, CNC Machining |
Crossover SUVs (Model X, Model Y) | Aluminum (6061-T6), High-Strength Steel (DP980), CFRP | CAD Modeling, SLA 3D Printing, Investment Casting |
Semi-Truck (Tesla Semi) | Stainless Steel (301 SS), Aluminum (7075-T6), Lithium-Ion 4680 Cells | FEA, Powder Bed Fusion, CNC Machining |
Autonomous Vehicles (Cybercab, Robovan) | Aluminum (6061-T6), CFRP, Polycarbonate | Digital Twins, Multi-Jet Fusion, CNC Machining |
Sports Car (Roadster) | Carbon Fiber, Aluminum (7075-T6), Lithium-Ion 4680 Cells | SLA 3D Printing, CNC Machining, FEA |
Conclusion
Tesla’s vehicle classifications—luxury sedans, crossover SUVs, semi-trucks, autonomous vehicles, and sports cars—require tailored precision machining technologies to meet performance and efficiency goals. Materials like aluminum, high-strength steel, carbon fiber, and lithium-ion cells are selected for their mechanical properties, while prototyping methods like CAD modeling, 3D printing, and CNC machining ensure accurate design validation. Precision machining techniques, including CNC milling, Giga Press die-casting, and laser cutting, enable high-quality production with tight tolerances. This systematic approach underscores Tesla’s ability to deliver diverse, high-performance electric vehicles through advanced manufacturing processes.
Frequently Asked Questions (FAQ)
What are the main vehicle classes Tesla produces?
Tesla’s vehicle lineup includes five primary classes:
Luxury sedans (Model S, Model 3)
Crossover SUVs (Model X, Model Y)
Semi-trucks (Tesla Semi)
Autonomous vehicles (Cybercab, Robovan)
Sports cars (Roadster, upcoming Roadster 2.0)
Each class is designed for specific market needs, from daily commuting to heavy-duty transport, with unique engineering requirements.
How do Tesla’s luxury sedans (Model S and Model 3) differ in materials and manufacturing?
Model S: A full-size luxury sedan with a dual-motor layout and up to 405 miles of range. It uses 6000-series aluminum alloys (e.g., 6061-T6) for body panels and boron steel (22MnB5) for structural reinforcement.
Model 3: A compact mid-range sedan with up to 341 miles of range. It shares material technologies with the Model S (aluminum extrusions and boron steel) but is optimized for cost and efficiency, with a simpler production process.
Both use CNC machining and laser cutting for precision components, with tolerances as tight as ±0.01 mm for critical parts like suspension mounts.
What materials are unique to Tesla’s autonomous vehicles (Cybercab and Robovan)?
Autonomous models prioritize lightweighting and sensor integration:
Aluminum chassis (6061-T6) for weight reduction
CFRP panels (modulus ~200 GPa) for durability and low mass
Polycarbonate sensor housings (impact strength ~850 J/m) to protect LiDAR and cameras
Prototyping uses digital twins for virtual testing and multi-jet fusion 3D printing for sensor mounts (tolerances ±0.1 mm).
How does CNC machining contribute to Tesla’s vehicle quality?
CNC machining (milling, turning) enables tight tolerances (±0.01–0.05 mm) for critical components:
Suspension mounts and battery housings require precision to ensure fit and safety.
5-axis CNC machines handle complex geometries, such as the Roadster 2.0’s carbon-fiber monocoque (tolerances ±0.015 mm).
Surface finishes as smooth as Ra ~0.8 µm (e.g., Model Y castings) enhance structural strength and aesthetics.