A turbine rotor is a critical component in various turbine systems, converting fluid energy into mechanical work. This guide provides a detailed examination of turbine rotor design, functionality, and applications across industries, focusing on technical specifications, materials, and operational parameters.
Overview of Turbine Rotors
Turbine rotors are rotating components that harness energy from a moving fluid—such as steam, gas, or water—to produce mechanical power. They consist of a shaft and attached blades or buckets, which interact with the fluid to generate rotational motion. Rotors are integral to power generation, aviation, and industrial processes, with designs tailored to specific turbine types and operational conditions.
Key functions include energy conversion, torque transmission, and maintaining structural integrity under high-speed and high-temperature conditions. Rotors must withstand centrifugal forces, thermal stresses, and aerodynamic loads, making their design a complex engineering task.
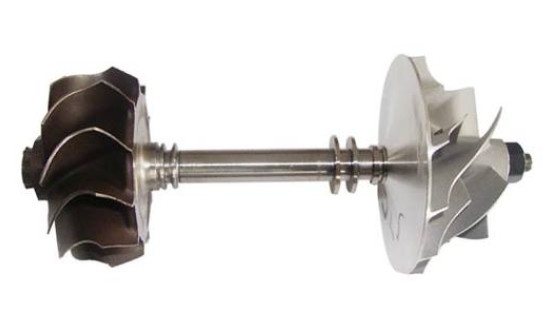
Types of Turbine Rotors
Turbine rotors vary based on the turbine type and application. The main types include:
- Steam Turbine Rotors: Used in power plants, these rotors operate with high-pressure steam. They are typically forged from alloy steels to handle temperatures up to 600°C and pressures up to 250 bar.
- Gas Turbine Rotors: Found in jet engines and industrial gas turbines, these rotors endure extreme temperatures (up to 1,500°C) and require materials like nickel-based superalloys.
- Hydro Turbine Rotors: Used in hydroelectric plants, these rotors interact with water flow. They are designed for lower speeds (50–300 RPM) but high torque, often using stainless steel for corrosion resistance.
- Wind Turbine Rotors: These convert wind energy into mechanical power, with rotor diameters ranging from 40 to 200 meters, depending on the turbine capacity (1–10 MW).
Each type demands specific design considerations, such as blade geometry, material selection, and balancing techniques, to optimize performance.
Design Principles of Turbine Rotors
Turbine rotor design involves balancing aerodynamic efficiency, structural integrity, and manufacturability. Key parameters include:
- Blade Geometry: Blade shape, angle, and twist affect fluid flow and energy transfer. For example, steam turbine blades may have a taper ratio of 0.6–0.8 to minimize losses.
- Shaft Design: The shaft must resist torsional stress and bending. Typical diameters range from 0.3 to 1.5 meters, depending on the turbine size.
- Balancing: Rotors are dynamically balanced to reduce vibrations, with allowable imbalances as low as 0.01 mm/s for high-speed turbines.
- Cooling Systems: Gas turbine rotors often incorporate internal cooling channels to manage temperatures, with coolant flow rates up to 10% of the main gas flow.
Design processes rely on computational fluid dynamics (CFD) and finite element analysis (FEA) to simulate performance under operational loads. For instance, a gas turbine rotor may experience centrifugal forces exceeding 10,000 g, requiring precise stress analysis.
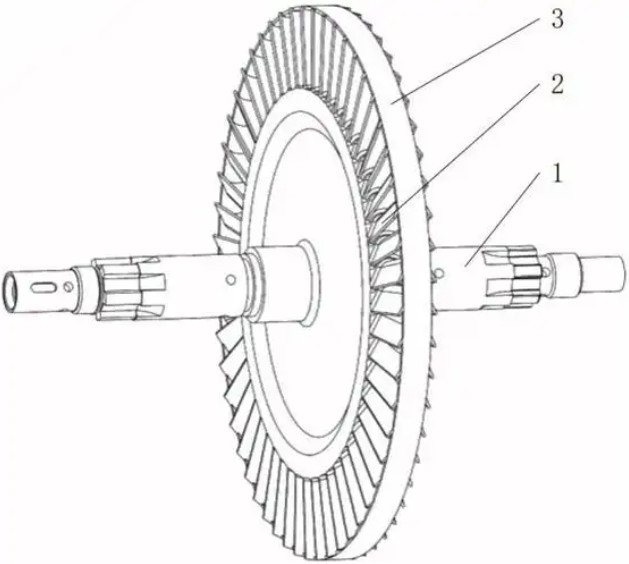
Materials Used in Turbine Rotors
Material selection is critical for turbine rotors due to extreme operating conditions. Common materials include:
Material | Application | Properties | Typical Use |
---|---|---|---|
Alloy Steel (e.g., Cr-Mo-V) | Steam Turbines | High strength, creep resistance up to 600°C | Shafts, low-pressure blades |
Nickel-Based Superalloys (e.g., Inconel 718) | Gas Turbines | High-temperature strength, oxidation resistance up to 1,500°C | High-pressure blades, discs |
Stainless Steel (e.g., 17-4 PH) | Hydro Turbines | Corrosion resistance, high toughness | Runners, buckets |
Composite Materials (e.g., Carbon Fiber) | Wind Turbines | Lightweight, high stiffness | Blades |
Material choice depends on factors like operating temperature, corrosion potential, and fatigue life. For example, nickel-based superalloys have a yield strength of 1,000 MPa at 800°C, making them ideal for gas turbines.
Manufacturing Processes
Turbine rotor manufacturing involves precision techniques to ensure reliability and performance. Key processes include:
- Forging: Used for rotor shafts and discs, forging ensures uniform grain structure. Forged components can withstand stresses up to 1,200 MPa.
- Casting: Impellers or Blades for gas turbines are often investment-cast to achieve complex geometries, with tolerances as tight as ±0.05 mm.
- Machining: CNC machining refines blade profiles and shaft surfaces, achieving surface roughness values below Ra 0.8 µm.
- Joining: Blades are attached to the rotor disc via fir-tree or dovetail roots, designed to handle shear stresses up to 500 MPa.
Non-destructive testing (NDT), such as ultrasonic and X-ray inspection, ensures defect-free components. For example, cracks smaller than 0.1 mm can be detected to prevent fatigue failure.
Operational Parameters and Performance
Turbine rotor performance is governed by parameters such as rotational speed, power output, and efficiency. Typical values include:
Turbine Type | Rotational Speed (RPM) | Power Output (MW) | Efficiency (%) |
---|---|---|---|
Steam Turbine | 3,000–3,600 | 50–1,000 | 35–45 |
Gas Turbine | 3,000–15,000 | 20–400 | 30–40 |
Hydro Turbine | 50–300 | 10–800 | 85–95 |
Wind Turbine | 10–20 | 1–10 | 40–50 |
Performance is optimized by minimizing losses, such as aerodynamic drag and tip leakage, which can reduce efficiency by 2–5%. Regular maintenance, including blade cleaning and balancing, is essential to sustain performance.
Applications of Turbine Rotors
Turbine rotors are used in diverse industries, each with specific requirements:
- Power Generation: Steam and hydro turbine rotors drive generators in coal, nuclear, and hydroelectric plants, producing up to 1,000 MW per unit.
- Aviation: Gas turbine rotors power jet engines, delivering thrust ranging from 20,000 to 100,000 pounds in commercial aircraft.
- Industrial Processes: Gas turbines drive compressors and pumps in oil and gas facilities, with rotor speeds up to 15,000 RPM.
- Renewable Energy: Wind turbine rotors convert wind energy into electricity, with modern designs achieving capacities up to 10 MW.
Each application demands tailored rotor designs to meet operational demands, such as high efficiency in hydro turbines or compact size in aviation turbines.
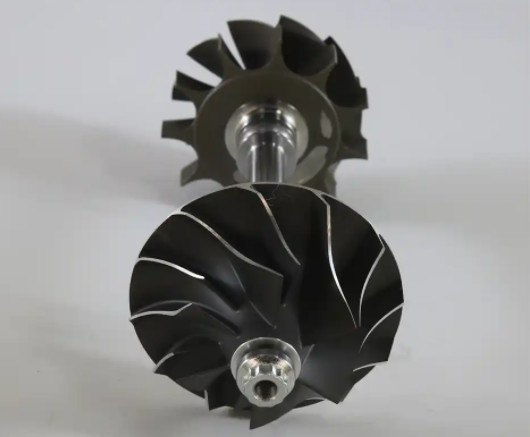
Maintenance and Inspection
Regular maintenance ensures rotor longevity and performance. Key activities include:
- Vibration Monitoring: Sensors detect imbalances, with thresholds typically set at 2–4 mm/s for high-speed rotors.
- Blade Inspection: Visual and NDT methods identify cracks or erosion, particularly in steam and gas turbines exposed to harsh conditions.
- Coating Application: Thermal barrier coatings (TBCs) are applied to gas turbine blades to extend life, with thicknesses of 0.1–0.5 mm.
- Balancing: Periodic rebalancing corrects mass distribution, ensuring vibration levels remain below 0.02 mm/s.
Maintenance intervals vary by turbine type, typically every 8,000–25,000 operating hours for gas turbines and 5–10 years for hydro turbines.
Operational Considerations
While turbine rotors are robust, certain operational factors require attention:
- Thermal Fatigue: Repeated thermal cycling in gas turbines can lead to crack initiation, with fatigue life often limited to 100,000 cycles.
- Corrosion: Hydro turbine rotors face pitting corrosion in saline environments, requiring coatings or cathodic protection.
- Blade Fouling: Deposits on blades reduce efficiency by 1–3%, necessitating regular cleaning.
Addressing these factors through design and maintenance minimizes downtime and extends rotor life.
Conclusion
Turbine rotors are essential components that enable efficient energy conversion across industries. Their design, material selection, and manufacturing processes are tailored to meet specific operational demands, from high-temperature gas turbines to corrosion-resistant hydro turbines. By understanding rotor types, design principles, and maintenance requirements, engineers can optimize performance and reliability in diverse applications.