Ultrasonic Machining (USM), also known as Ultrasonic Vibration Machining, is a non-traditional subtractive manufacturing process that uses high-frequency, low-amplitude vibrations to remove material from a workpiece. Unlike conventional machining methods that rely on direct cutting action, USM employs the abrasive action of microscopic particles suspended in a slurry to abrade material from the workpiece surface. This unique mechanism makes it particularly effective for machining hard, brittle, and non-conductive materials that are difficult or impossible to process with traditional methods.
How Ultrasonic Machining Works
The core principle of ultrasonic machining revolves around the rapid, vertical vibration of a tool in the presence of an abrasive slurry. This process, often referred to as "abrasive grinding with ultrasonic assistance," is a mechanical erosion process rather than a thermal or electrical one.
The fundamental components of a USM system include:
- A Power Source: This converts standard line frequency (e.g., 60 Hz) into a high-frequency electrical signal, typically in the range of 19 to 25 kHz.
- A Transducer: The high-frequency electrical signal is fed into a magnetostrictive or piezoelectric transducer. A magnetostrictive transducer uses the change in shape of a ferromagnetic material (like nickel) when exposed to a magnetic field, while a piezoelectric transducer uses the property of certain crystals (like quartz or lead zirconate titanate) to change shape when an electric field is applied. This converts the electrical energy into mechanical vibrations at the same high frequency.
- A Mechanical Amplifier (Booster): The low-amplitude vibrations from the transducer are often amplified by a booster. This component is designed to resonate at the same frequency as the transducer, effectively increasing the amplitude of the vibration.
- A Tool Holder (Horn/Sonotrode): The booster is connected to a tool holder, which transfers the amplified vibrations to the cutting tool. The horn is a critical component, as its geometry and material must be carefully selected to maximize the efficiency of energy transfer.
- A Tool: The cutting tool is attached to the horn. Unlike conventional tools, the USM tool does not need to be harder than the workpiece; it simply needs to be able to withstand the vibrations and act as a hammer. Common tool materials include soft steel and nickel.
- An Abrasive Slurry: This mixture of abrasive particles and a liquid medium is the actual cutting agent. The slurry is continuously fed into the gap between the tool and the workpiece.
The machining process begins when the high-frequency vibrations from the tool strike the abrasive particles in the slurry. These particles are then accelerated and strike the workpiece surface with significant force. This repeated, high-speed hammering action causes microscopic chips and flakes of material to be abraded or "chipped away" from the workpiece. The liquid in the slurry (often water) serves several purposes: it acts as a carrier for the abrasive particles, flushes away the abraded material, and dissipates some of the heat generated. The overall material removal process is a result of the collective impact of countless tiny particles, leading to a clean, precise cut.
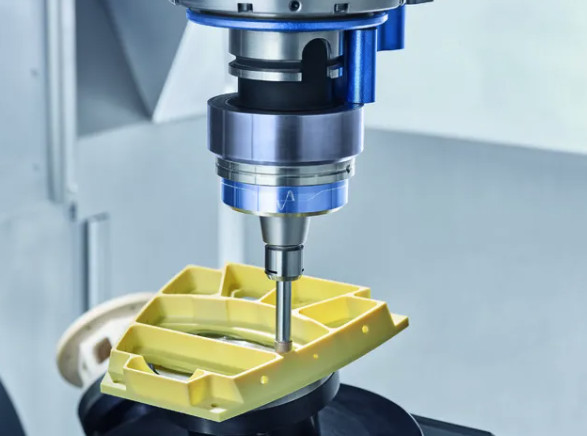
The Abrasive Slurry and Its Role
The abrasive slurry is a key element that dictates the performance of the USM process. Its composition and properties directly influence the material removal rate (MRR), surface finish, and tool wear.
Abrasive Particles: The particles are the primary cutting medium. Their properties, including hardness, size, and shape, are crucial. Common abrasive materials include:
- Boron Carbide (B4C): Extremely hard, it is a preferred choice for machining very hard ceramics and tungsten carbide.
- Silicon Carbide (SiC): Hard and durable, it is widely used for machining glass, quartz, and various ceramics.
- Aluminum Oxide (Al2O3): A cost-effective option for softer materials.
- Diamond: Used for machining extremely hard materials like synthetic diamond and hardened steels.
Abrasive Particle Size (Grit Size): This parameter is a critical determinant of both material removal rate and surface finish. Abrasive particle size is often denoted by a grit number, with a higher number indicating a smaller particle size.
- Larger Particles (Lower Grit Number): Result in a higher material removal rate but a rougher surface finish. They create larger indentations and chips, removing more material per unit of time.
- Smaller Particles (Higher Grit Number): Lead to a lower material removal rate but produce a much smoother, higher-quality surface finish. They create smaller, more precise indentations.
A typical range for abrasive particle size is from 100 to 1000 grit, but can extend beyond this depending on the specific application requirements.
Slurry Concentration and Viscosity: The concentration of abrasive particles in the liquid medium affects how efficiently the particles can be delivered to the work zone. An optimal concentration ensures a sufficient number of particles for effective cutting without becoming too viscous and impeding the flushing of debris. The viscosity of the liquid also plays a role; a lower viscosity allows used abrasives to be more easily flushed away and replaced by fresh slurry.
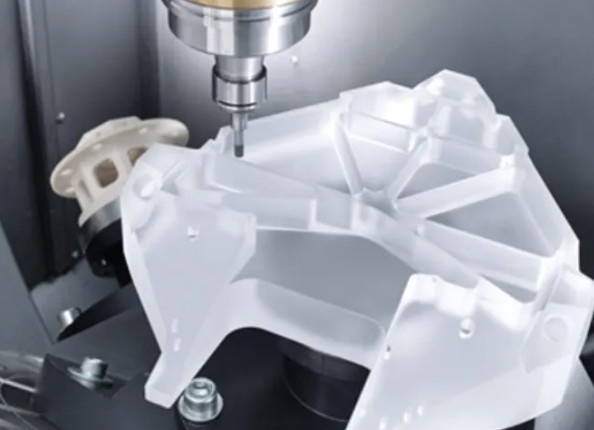
Process Parameters and Their Effects
The outcome of an ultrasonic machining operation is governed by a number of interrelated process parameters. Understanding these relationships is essential for process optimization.
Tool Amplitude: This is the peak-to-peak displacement of the tool's vibration. It is a fundamental parameter that directly affects the force with which the abrasive particles impact the workpiece. A higher amplitude generally leads to a higher material removal rate but can also result in faster tool wear and a rougher surface finish. Typical amplitudes range from 0.05 to 0.125 mm (0.002 to 0.005 inches).
Frequency of Vibration: The frequency is the rate at which the tool vibrates. Most USM systems operate at a frequency between 19 and 25 kHz. While the frequency is generally fixed for a given machine, its consistency is crucial for maintaining the resonant state of the system, which is necessary for efficient energy transfer.
Static Force: This is the constant downward pressure applied to the tool. It ensures that the tool maintains contact with the abrasive particles and the workpiece. An optimal static force balances the need for effective abrasion with the risk of "damping" the tool's vibrations. Excessive force can reduce the amplitude of the vibrations, decreasing the MRR, while insufficient force may not provide enough energy for efficient cutting.
Slurry Flow Rate: The rate at which the abrasive slurry is fed into the gap between the tool and workpiece. A sufficient flow rate is necessary to continuously supply fresh abrasive particles to the cutting zone and flush away the spent particles and debris. An inadequate flow rate can lead to a reduction in MRR and a poor surface finish.
Advantages of Ultrasonic Machining
Ultrasonic machining offers several distinct advantages, particularly when dealing with specific material types and geometric requirements.
- Machining Hard and Brittle Materials: USM is the go-to process for machining materials with high hardness and low fracture toughness, such as advanced ceramics, glass, quartz, and single-crystal silicon. The process works by inducing microscopic cracks and chipping, which is a highly effective mechanism for these material types.
- No Heat-Affected Zone (HAZ): Unlike thermal machining processes like laser or electrical discharge machining (EDM), USM is a mechanical process. There is no significant heat generation in the workpiece, which prevents the formation of a heat-affected zone, micro-cracks, or changes in the material's microstructure. This is a crucial advantage for heat-sensitive materials.
- High-Quality Surface Finish and Dimensional Accuracy: The use of fine abrasive particles and the non-thermal nature of the process allow for the achievement of excellent surface finishes (typically 0.1−0.8μm Ra) and tight dimensional tolerances ($ \pm 0.005 mm$ or better). This makes it suitable for applications requiring high precision.
- Ability to Machine Complex Geometries: USM can be used to create intricate and complex shapes, including non-circular holes, cavities, and fine features, which would be challenging to produce with conventional drilling or milling. The shape of the tool is replicated in the workpiece, enabling the creation of custom forms.
- Non-Conductive Materials: Since the process does not rely on electrical or thermal energy transfer, it can be used to machine electrically non-conductive materials, opening up applications in the electronics and semiconductor industries.

Applications of Ultrasonic Machining
The unique capabilities of USM have led to its adoption in a wide range of industries for various applications.
- Electronics and Semiconductors: Machining of micro-electromechanical systems (MEMS) components, precise features on glass wafers, and other brittle semiconductor materials.
- Medical and Dental: Drilling and shaping of hard materials for medical implants, and creating intricate features on dental ceramics.
- Aerospace: Machining of complex ceramic and composite components used in high-temperature environments.
- Jewelry: Cutting and shaping of gemstones, including diamonds and sapphires, with high precision.
- Tool and Die Making: Creating intricate die cavities in hardened steel, though the material removal rate is slow.
- General Manufacturing: Drilling holes of various shapes, creating intricate engravings, and performing trepanning (core drilling) on brittle materials like glass, quartz, and ferrite.
Typical USM Process Parameters | Value Range |
Frequency (f) | 19−25 kHz |
Tool Amplitude (A) | 0.005−0.125 mm (0.002−0.005 inches) |
Abrasive Grit Size | 100−1000 (higher grit = smaller particles) |
Static Force (Fs) | 2.5−45 N |
Slurry Concentration | 20%−50% by weight |
Gap between Tool and Workpiece | 0.025−0.1 mm |
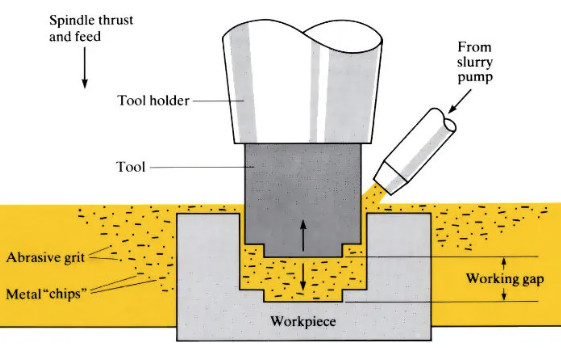
Obstacles in Ultrasonic Machining
While USM is a powerful process, it is not without its limitations and practical challenges that need to be considered.
- Low Material Removal Rate (MRR): Compared to conventional machining processes like milling or turning, the material removal rate in USM is significantly slower. This makes it less suitable for large-scale material removal from bulky workpieces and often relegates its use to finishing operations or creating fine features.
- Tool Wear: The process of repeated hammering against abrasive particles and the workpiece causes the tool to wear down. The wear rate is dependent on the tool material, workpiece material, and process parameters. This tool wear can affect the accuracy of the machined features and necessitates frequent tool replacement or compensation.
- Cost: The initial investment for USM equipment can be high. Additionally, the cost of abrasives and tooling adds to the overall operational expenses.
- Limited Depth of Machining: Ultrasonic machining is not well-suited for creating deep holes or cavities. As the depth increases, it becomes difficult to effectively flush the abrasive slurry and debris, leading to a significant drop in material removal efficiency. This limitation restricts its use for certain applications.
- Slurry Management: The abrasive slurry needs to be continuously managed, which involves a pump and a collection system. The proper concentration and flow rate must be maintained to ensure consistent performance.
Summary
Ultrasonic machining is a specialized and highly effective manufacturing process that carves a unique niche in the world of material removal. By leveraging high-frequency vibrations and the abrasive action of a slurry, it can precisely machine hard, brittle, and non-conductive materials that are a significant challenge for conventional methods. While its material removal rate is slow, its ability to produce intricate geometries with a high-quality surface finish and no thermal damage makes it an indispensable tool in industries ranging from aerospace and medical to electronics and jewelry. Its advantages in precision and versatility for difficult materials far outweigh its limitations in specific applications.
FAQ about Ultrasonic Machining (USM)
What is Ultrasonic Machining (USM)?
Ultrasonic Machining (USM) is a non-traditional subtractive manufacturing process that removes material from a workpiece using high-frequency, low-amplitude vibrations. Unlike conventional machining, which relies on direct cutting, USM uses the abrasive action of microscopic particles suspended in a slurry to abrade material from the workpiece surface. It is particularly effective for hard, brittle, and non-conductive materials that are challenging to process with traditional methods.
What are the key components of a USM system?
Power Source: Converts standard line frequency (e.g., 60 Hz) into a high-frequency electrical signal (19–25 kHz).
Transducer: Converts the high-frequency electrical signal into mechanical vibrations. It can be magnetostrictive (using ferromagnetic materials like nickel) or piezoelectric (using crystals like quartz or lead zirconate titanate).
Mechanical Amplifier (Booster): Amplifies the low-amplitude vibrations from the transducer while maintaining resonance with the system.
Tool Holder (Horn/Sonotrode): Transfers amplified vibrations to the tool. Its geometry and material are critical for efficient energy transfer.
Tool: Does not need to be harder than the workpiece but must withstand vibrations. Common materials include soft steel and nickel.
Abrasive Slurry: A mixture of abrasive particles and liquid (e.g., water) that acts as the cutting medium, continuously fed into the gap between the tool and workpiece.
What are the main advantages of Ultrasonic Machining?
Suitable for Hard/Brittle Materials: Effective for ceramics, glass, quartz, and non-conductive materials.
No Heat-Affected Zone (HAZ): Mechanical process with minimal heat, preserving material microstructure (ideal for heat-sensitive materials).
High Precision and Surface Quality: Achieves fine finishes (0.1–0.8 μm Ra) and tight tolerances (±0.005 mm).
Complex Geometry Capability: Machines intricate shapes (e.g., non-circular holes, cavities) that are difficult with traditional methods.
Non-Conductive Material Compatibility: Works on materials that resist electrical or thermal machining.
What are the limitations of Ultrasonic Machining?
Low Material Removal Rate (MRR): Much slower than conventional methods (e.g., milling), limiting use to finishing or fine features.
Tool Wear: High-frequency vibration and abrasive impact cause tool degradation, reducing precision and increasing replacement costs.
High Costs: Significant initial investment in equipment, plus ongoing expenses for abrasives and tooling.
Limited Depth: Deep holes/cavities are challenging due to poor slurry circulation and reduced efficiency.
Slurry Management Complexity: Requires consistent concentration and flow to maintain process stability.
How does USM differ from traditional machining (e.g., milling, grinding)?
Mechanism
Ultrasonic Machining (USM): Utilizes high-frequency mechanical vibrations (15–70 kHz) of a tool, paired with an abrasive slurry (e.g., boron carbide) between the tool and workpiece. Material is removed through micro-chipping via abrasive impacts.
Traditional Machining (Milling/Grinding): Relies on direct contact between a hard tool/abrasive (e.g., milling cutter, grinding wheel) and the workpiece. Material is removed by cutting, shearing, or abrasion via tool rotation/feed.
Suitable Materials
USM: Ideal for hard, brittle, and non-conductive materials such as ceramics, glass, silicon, and quartz. Ineffective for ductile materials (they absorb vibrations).
Traditional Machining: Works well with ductile materials like metals (steel, aluminum), plastics, and softer alloys. Less effective for extremely hard/brittle materials (may cause tool wear or workpiece fracture).
Thermal Impact
USM: No significant heat generation. No thermal damage, heat-affected zones (HAZ), or alterations to material properties (e.g., warping, oxidation).
Traditional Machining: Generates substantial heat due to friction, leading to HAZ, thermal distortion, or changes in material microstructure (e.g., annealing, hardening).
Tool Hardness
USM: Tool material does not need to be harder than the workpiece. Tools are often made of softer materials (e.g., brass, steel) since abrasives perform the cutting.
Traditional Machining: Tool/abrasive must be harder than the workpiece (e.g., carbide cutters for metals, diamond wheels for hard materials) to ensure effective material removal.
Material Removal Rate (MRR)
USM: Low MRR, making it ideal for precision tasks (e.g., micro-holes, intricate shapes) rather than bulk material removal.
Traditional Machining: High MRR, suitable for large-scale material removal in mass production or roughing operations.