Cold forging, encompassing processes like cold die forging, cold extrusion, and cold heading, is a metal forming technique performed below the material’s recrystallization temperature, typically at room temperature. Unlike hot forging, cold forging does not involve heating the billet, resulting in distinct advantages and challenges. This process induces work hardening due to the accumulation of dislocations in the metal, which become entangled, restricting movement and increasing hardness. The grains elongate along the deformation direction, forming a textured structure that heightens crack sensitivity during multiple forging steps.
Cold forging offers superior surface quality and dimensional accuracy, often replacing machining processes. It enhances metal strength through work hardening, improves component durability, and avoids defects associated with heated metal, such as oxidation. Additionally, it enables high-precision near-net-shape forming, reducing material waste and manufacturing costs. As a room-temperature process, cold forging is environmentally friendly and supports high-volume production of mechanical components.
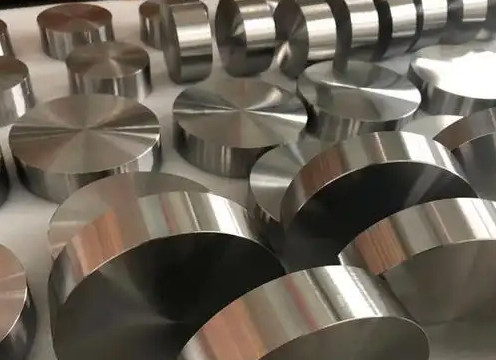
Cold Forging Materials and Their Requirements
Cold forging demands materials with low deformation resistance and high ductility at room temperature. Commonly used materials include aluminum, select aluminum alloys, copper, select copper alloys, low-carbon steel, medium-carbon steel, and low-alloy structural steels. Materials with low deformation resistance and high deformability are ideal for cold forging. To achieve a softened state and reduce deformation resistance, materials often undergo softening or spheroidizing annealing before forging.
Low-carbon and carburizing steels with high ferrite content can be cold forged in their as-rolled state due to their softness and ductility. However, high-carbon steels, high-strength steels, and bearing steels typically require spheroidizing annealing to enhance forgeability. Even after annealing, variations in chemical composition can lead to differences in deformation resistance. For materials undergoing multiple deformations, additional recrystallization annealing or auxiliary processes may be necessary to manage work hardening.
Surface quality is critical in cold forging. Machined surfaces are preferred to minimize defects post-forging. Surface decarburization can cause fine cracks, reduce fatigue strength, or lead to insufficient hardness after quenching and tempering. Therefore, standards specify permissible decarburization depths. Conversely, surface carburization can enhance surface energy, offsetting residual tensile stresses and improving deformation capacity. The forgeability of steel is often evaluated based on spheroidization quality, as ductile fracture during plastic deformation typically initiates at non-metallic inclusions, secondary phases, or precipitates.
Pretreatment in Cold Forging: Purpose and Necessity
Pretreatment, such as softening or spheroidizing annealing, is essential to prepare materials for cold forging. These processes reduce deformation resistance, enhance ductility, and mitigate the risk of cracking due to work hardening. Without pretreatment, the high deformation forces required could exceed equipment capacity or cause material failure. Annealing also ensures a uniform microstructure, which is critical for consistent mechanical properties and dimensional accuracy in the final component.
For high-carbon or alloy steels, spheroidizing annealing transforms the microstructure into a soft, ductile state by forming spherical carbides, reducing internal stresses, and improving formability. This is particularly important for complex geometries, where high deformation resistance could lead to defects. Pretreatment also minimizes surface imperfections, such as decarburization, which could compromise the component’s performance during subsequent heat treatments like carburizing and quenching.
Post-Cold Forging Heat Treatment
After cold forging, components often undergo heat treatments like carburizing and quenching to achieve the desired strength and hardness. However, the strain induced by cold forging can cause issues during these processes, such as abnormal grain growth, resulting in coarse or mixed-grain structures that reduce strength. To mitigate this, normalization (isothermal or standard) is performed to eliminate residual stresses and restore a uniform microstructure.
Normalization involves heating the component to a specific temperature, holding it to allow austenite transformation, and cooling it in air or under controlled conditions. This process refines the microstructure, reduces internal stresses, and prepares the material for carburizing. In some cases, alloying elements like aluminum, niobium, or titanium are added to form carbonitrides, which pin grain boundaries and prevent excessive grain growth during heat treatment.
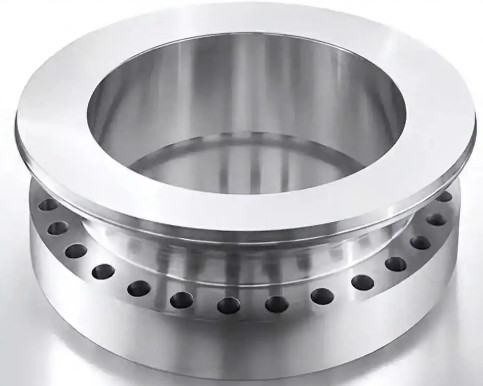
Case Study: Normalization Issues with 16MnCr5 Steel
In production, a cold-forged shaft made of 16MnCr5 steel exhibited inconsistent normalization results. After a single normalization at 940°C, 10–20% of components showed mixed-grain structures, indicating abnormal grain growth. A second normalization improved the microstructure, and subsequent carburizing and quenching yielded a normal core structure without coarse grains. However, components with mixed grains after the first normalization exhibited coarse structures post-carburizing, compromising mechanical properties.
The normalization process used a furnace with a conveyor speed of 30 ± 5 Hz, air-cooling speed of 20 ± 5 Hz, fan frequencies of 35 ± 5 Hz, and an isothermal speed of 30 ± 5 Hz. The standard normalization temperature was 940 ± 10°C, while carburizing was performed at 860 ± 10°C. To reduce energy consumption and oxidation, a lower normalization temperature of 900 ± 5°C was tested. A batch of 100 components was split evenly between the two temperatures, and their metallographic structures were compared post-normalization and post-carburizing.
Process Parameter | 940°C Normalization | 900°C Normalization |
---|---|---|
Conveyor Speed (Hz) | 30 ± 5 | 30 ± 5 |
Air-Cooling Speed (Hz) | 20 ± 5 | 20 ± 5 |
Fan Frequency (Hz) | 35 ± 5 | 35 ± 5 |
Isothermal Speed (Hz) | 30 ± 5 | 30 ± 5 |
Metallographic Result | 10–20% mixed grains | Comparable to 940°C |
Metallographic analysis showed no significant difference between the 900°C and 940°C normalization structures, both meeting requirements. However, post-carburizing analysis revealed that components normalized at 900°C exhibited inferior microstructures compared to those normalized at 940°C, particularly in the worst-case samples.
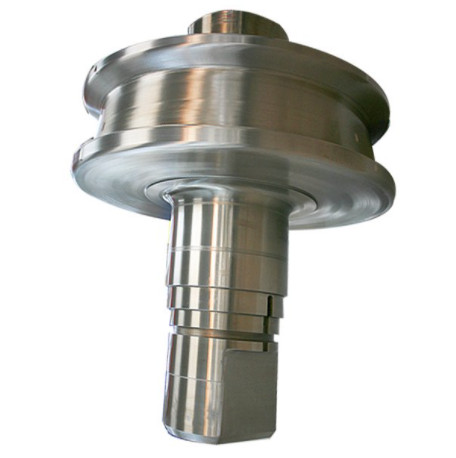
Metallographic Analysis and Findings
The inconsistent normalization results stem from the thermodynamics of cold-deformed metals. During cold forging, most deformation energy dissipates as heat, but 2–10% is stored as elastic strain energy and crystal defects (vacancies and dislocations), increasing the material’s free energy. This creates a metastable state, making the material prone to abnormal grain growth during heat treatment. When heated, cold-deformed metals undergo recovery, recrystallization, and grain growth. Higher normalization temperatures (e.g., 940°C) provide sufficient atomic mobility to eliminate defects and restore a stable microstructure, while lower temperatures (e.g., 900°C) may not fully achieve this, leading to suboptimal structures post-carburizing.
The presence of alloying elements like Al, Nb, and Ti influences recrystallization behavior. Variations in their content across batches may explain why some components required a second normalization. Higher normalization temperatures facilitate complete recrystallization, reducing defect density and ensuring a uniform microstructure for subsequent carburizing.
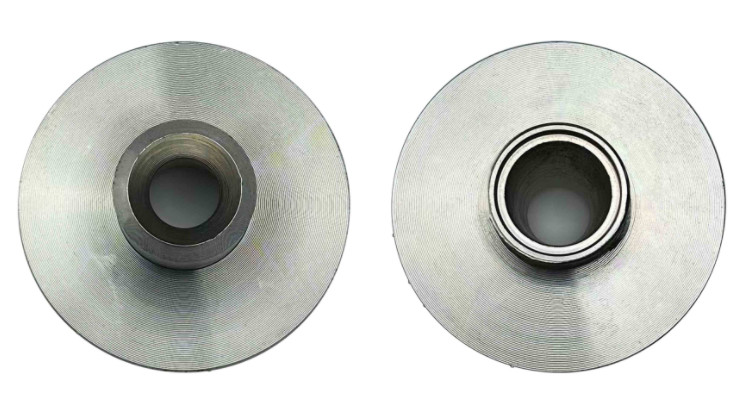
Preventive Measures for Production
To address normalization issues and ensure consistent quality, the following measures are recommended:
- Standardize Normalization Temperature: Set the normalization temperature at 940 ± 10°C for 16MnCr5 steel to ensure sufficient defect elimination and uniform microstructure. Avoid lower temperatures like 900°C unless validated for specific applications.
- Increase Metallographic Inspection: For cold-forged components, increase the sampling rate for metallographic analysis compared to hot-forged parts. This ensures early detection of mixed-grain structures.
- Monitor Alloy Composition: Regularly analyze the content of grain-refining elements (Al, Nb, Ti) in incoming materials to predict normalization behavior and adjust processes accordingly.
- Implement Secondary Normalization: For batches showing mixed grains after the first normalization, perform a second normalization before carburizing to eliminate residual defects.
- Control Surface Quality: Ensure billets have minimal decarburization and high surface quality before forging to reduce crack sensitivity and improve fatigue performance.
Preventive Measure | Action | Expected Outcome |
---|---|---|
Standardize Temperature | Use 940 ± 10°C for normalization | Uniform microstructure, reduced defects |
Increase Inspection | Higher sampling rate for cold-forged parts | Early detection of mixed grains |
Monitor Alloy Content | Analyze Al, Nb, Ti levels | Predict and adjust normalization needs |
Secondary Normalization | Apply if mixed grains detected | Eliminate residual defects |
Surface Quality Control | Minimize decarburization | Improved fatigue strength |
Conclusion
Pretreatment in cold forging is critical to reduce deformation resistance, enhance ductility, and ensure defect-free components. For 16MnCr5 steel, normalization at 940°C is more effective than 900°C in eliminating cold-forging-induced defects, ensuring a uniform microstructure post-carburizing. Variations in alloy composition and insufficient normalization temperatures contribute to mixed-grain issues. Implementing standardized temperatures, increased inspections, and alloy monitoring can prevent these problems, ensuring high-quality cold-forged components.