Zinc, a versatile metal, is widely utilized in manufacturing due to its favorable mechanical properties, corrosion resistance, and machinability. This guide provides a detailed overview of zinc and its alloys, their applications across industries, and the machining processes used to shape them. Emphasis is placed on machining techniques, precision, complexity, and processing considerations, offering a systematic and technical resource for engineers and manufacturers.
Properties of Zinc and Its Alloys
Zinc (Zn) is a non-magnetic metal commonly alloyed with aluminum, magnesium, and copper to enhance its mechanical properties. These alloys, such as Zamak and ZA series, are known for their strength, ductility, and corrosion resistance. The following properties make zinc a preferred material in various applications:
- High Machinability: Zinc alloys have a machinability index exceeding 90%, resulting in low tool wear and efficient material removal.
- Corrosion Resistance: Zinc’s natural resistance to corrosion, enhanced by coatings like chromate conversion, ensures durability in harsh environments.
- Low Melting Point: At approximately 419.5°C, zinc’s low melting point facilitates casting and molding of intricate shapes.
- Ductility: Zinc alloys allow for complex component designs without compromising structural integrity.
- Thermal Conductivity: With a conductivity of ~116 W/m·K, zinc dissipates heat effectively during machining, reducing the need for extensive cooling.
Common zinc alloys include Zamak 3, Zamak 5, ZA-8, and EZAC, each tailored for specific applications based on their composition. For instance, Zamak 3, composed of 3.5–4.3% aluminum, 0.02–0.05% magnesium, and trace copper, is widely used in North America for its balance of strength and castability. Zamak 5, with 1% copper, offers higher tensile strength (~330 MPa) and hardness (91–100 HB).
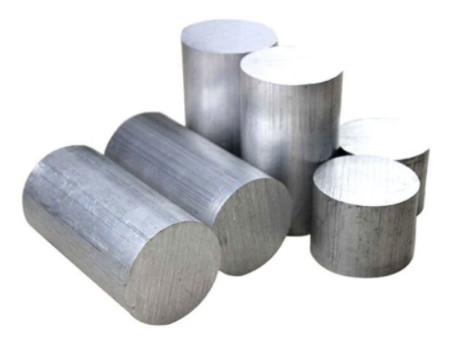
Applications of Zinc and Its Alloys
Zinc alloys are employed across multiple industries due to their cost-effectiveness, durability, and aesthetic versatility. Below are key applications:
- Automotive Industry: Zinc alloys are used for engine blocks, gearbox housings, brackets, and carburetor bodies due to their strength and corrosion resistance.
- Consumer Goods: Products like jewelry, zippers, hinges, and musical instruments leverage zinc’s aesthetic appeal and low cost.
- Electronics: Zinc alloys form robust housings and enclosures for devices, ensuring precision and durability.
- Construction: Architectural hardware, such as door locks and structural brackets, benefits from zinc’s strength and corrosion resistance.
- Telecommunications: Antenna components and communication device parts utilize zinc for precision and reliability.
The ability to apply surface finishes like electroplating, powder coating, and polishing enhances zinc’s suitability for both functional and decorative applications.
Machining Processes for Zinc Alloys
Zinc’s machinability makes it ideal for various machining processes, including CNC machining, die casting, and electrical discharge machining (EDM). Each method addresses specific requirements for precision, complexity, and production volume. Below is a detailed examination of these processes, focusing on precision, complexity, and processing considerations.
CNC Machining
Computer Numerical Control (CNC) machining is a cornerstone for zinc alloy processing, offering high precision and repeatability. CNC milling and turning are commonly used to create complex geometries and tight tolerances.
- CNC Milling: Utilizes rotating cutting tools to remove material, producing features like slots, holes, and contours. Advanced 5-axis CNC milling enables the creation of intricate shapes with tolerances as tight as ±0.02 mm. Key parameters include spindle speeds of 6,000–12,000 RPM and feed rates of 0.1–0.3 mm/rev to balance efficiency and surface quality.
- CNC Turning: Rotates the workpiece against a stationary cutting tool to produce cylindrical parts like shafts and bushings. Modern CNC lathes with multi-axis capabilities support turn-milling operations, achieving surface finishes of Ra ≤ 0.8 µm.
- Drilling and Tapping: Used for creating holes and threads, requiring sharp drill bits and water-based coolants to prevent heat buildup. Typical drilling speeds range from 50–100 m/min with feed rates of 0.05–0.15 mm/rev.
Precision and Complexity: CNC machining excels in achieving tolerances of ±0.005 in. (±0.13 mm) for general applications and ±0.002 in. (±0.05 mm) with precision setups. It handles complex geometries, such as those required for aerospace brackets and medical device components, with minimal re-fixturing.
Processing Considerations: Zinc’s low melting point can lead to thermal softening, causing material to stick to cutting tools (gumminess). Moderate feed rates and effective coolant systems mitigate this issue. High-aluminum alloys, like ZA-27, may exhibit brittleness, necessitating tools with optimized edge geometry to prevent chipping.
Die Casting
Die casting involves injecting molten zinc into molds under high pressure to produce near-net-shape parts with minimal secondary machining. Hot-chamber die casting is particularly effective due to zinc’s low melting point.
- Process Details: Molten zinc at 420–430°C is injected into steel molds at pressures of 10–20 MPa, enabling thin-walled components (0.5–2 mm) with tolerances of ±0.05 mm.
- Applications: Ideal for high-volume production of small, intricate parts like fasteners, brackets, and electronic housings.
Precision and Complexity: Die casting achieves high precision with minimal post-processing, suitable for complex geometries with thin features. Zamak 3 and EZAC are preferred for their fluidity, reducing porosity and ensuring dimensional stability.
Processing Considerations: High initial mold costs (tens of thousands of dollars) make die casting cost-effective only for large production runs. Proper mold design, including draft angles (1–3°) and uniform wall thickness, prevents warping and ensures part release.
Electrical Discharge Machining (EDM)
EDM uses electrical discharges to shape conductive materials, making it suitable for zinc alloys due to their excellent electrical conductivity.
- Process Details: A controlled spark erodes material, achieving tolerances of ±0.01 mm. Effective dielectric flushing removes debris to maintain stability.
- Applications: Used for prismatic components and intricate features in prototypes or small-scale production.
Precision and Complexity: EDM is ideal for high-precision applications requiring complex geometries, such as optical housings and precision instruments, where traditional machining is impractical.
Processing Considerations: EDM is slower and more costly than CNC machining, making it less suitable for high-volume production. Proper electrode selection and dielectric fluid management are critical for consistent results.
Surface Finishing for Zinc Alloys
Surface finishing enhances zinc’s corrosion resistance, wear resistance, and aesthetic appeal. Common techniques include:
Finishing Technique | Description | Applications |
---|---|---|
Electroplating | Deposits metals like chromium or nickel to improve corrosion and wear resistance. | Automotive fittings, consumer goods. |
Powder Coating | Applies a protective powder cured under heat, forming a durable layer. | Outdoor components, decorative hardware. |
Polishing | Mechanically smooths surfaces to reduce roughness (Ra ≤ 0.4 µm). | Jewelry, architectural hardware. |
Precision and Complexity: Finishing processes maintain dimensional accuracy while enhancing functionality. Electroplating adds a thin layer (5–20 µm), suitable for tight-tolerance parts.
Processing Considerations: Surface preparation, such as removing machining marks and oils, is essential for effective adhesion. Finishing costs vary, with electroplating costing $10–50/m² depending on the metal used.
Material Selection Guide for Zinc Alloys
Choosing the right zinc alloy depends on the application’s mechanical and aesthetic requirements. The following table summarizes key alloys and their properties:
Alloy | Composition | Yield Strength (MPa) | Hardness (HB) | Applications |
---|---|---|---|---|
Zamak 3 | Zn, 3.5–4.3% Al, 0.02–0.05% Mg | ~280 | 82–91 | Fasteners, consumer goods |
Zamak 5 | Zn, 3.5–4.3% Al, 1% Cu | ~330 | 91–100 | Automotive components |
ZA-8 | Zn, 8.4% Al, 1% Cu | ~374 | 100–106 | Structural parts |
Zamak 3 is the most versatile for general applications, while Zamak 5 and ZA-8 are chosen for higher strength requirements. EZAC is used for demanding applications like automotive safety components due to its superior creep resistance.
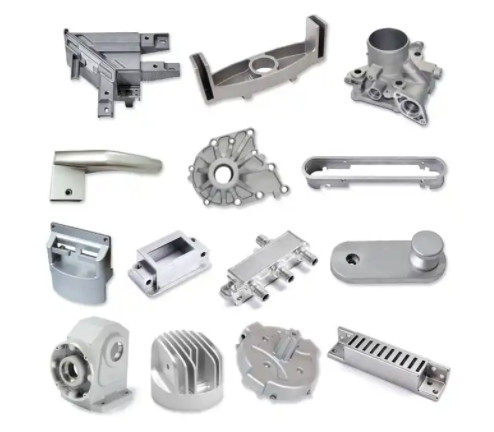
Design Considerations for Zinc Machining
Effective design enhances machinability and part performance. Key considerations include:
- Draft Angles: Incorporate 1–3° draft angles in die-cast parts to facilitate mold release and prevent warping.
- Uniform Wall Thickness: Maintain consistent wall thickness (1–3 mm) to ensure even cooling and reduce defects.
- Rounded Corners: Use radii of 0.5–1 mm to minimize stress concentrations and prevent cracking.
- Feature Orientation: Align ribs and bosses with load directions to enhance strength and simplify machining.
Design for Manufacturability (DFM) feedback during prototyping can optimize tool access and material removal, reducing production time and costs.
Conclusion
Zinc and its alloys are indispensable in modern manufacturing due to their machinability, corrosion resistance, and versatility. CNC machining, die casting, and EDM enable the production of precise, complex components for industries ranging from automotive to consumer goods. By understanding zinc’s properties, selecting appropriate alloys, and optimizing machining and finishing processes, manufacturers can achieve high-quality parts with tight tolerances and cost efficiency. This guide serves as a technical resource for professionals seeking to leverage zinc’s potential in their projects.