3D printing and CNC machining are two prominent manufacturing technologies used for prototyping and production. 3D printing, an additive manufacturing process, builds parts layer by layer, while CNC machining, a subtractive method, removes material from a solid block to create components.
Manufacturing Process and Workflow
3D printing and CNC machining differ fundamentally in their approach to creating parts. 3D printing constructs objects by depositing material layer by layer based on a digital model, typically requiring minimal operator intervention. CNC machining, in contrast, involves cutting away material from a workpiece using computer-controlled tools, demanding precise programming and setup.
In 3D printing, the workflow begins with a 3D CAD model, which is processed through slicing software to generate G-code. This code instructs the printer to deposit materials, such as thermoplastics or metal powders, in layers ranging from 0.01 mm to 0.3 mm in thickness, depending on the technology (e.g., FDM, SLS, or DMLS). The process is highly automated, with setup times often under 30 minutes, and printing can take hours to days based on part size and complexity.
CNC machining starts with a CAD model converted into G-code via CAM software. The machine, equipped with tools like mills, lathes, or grinders, removes material with spindle speeds up to 20,000 RPM and feed rates of 10–50 mm/s, depending on the material and tool. Setup can take 1–4 hours, involving tool selection, fixturing, and programming, with machining times ranging from minutes for simple parts to hours for complex geometries.
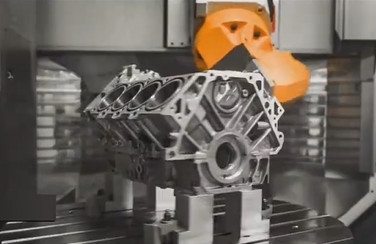
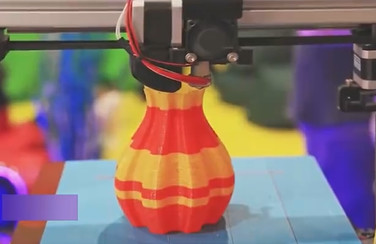
Material Compatibility and Properties
Material selection is a critical factor in choosing between 3D printing and CNC machining, as it affects part strength, durability, and application suitability.
3D printing supports a range of materials, including thermoplastics (e.g., ABS, PLA, Nylon), photopolymers, and metals (e.g., aluminum, titanium, stainless steel). However, material properties in 3D-printed parts can be anisotropic due to layer-by-layer construction. For example, FDM parts in ABS may achieve only 10–40% of the ultimate tensile strength (UTS) of injection-molded ABS (approximately 40 MPa vs. 100 MPa). Metal 3D printing, such as DMLS, can achieve near-isotropic properties but often requires post-processing like heat treatment to reach 90–100% of native material strength (e.g., 1100 MPa for titanium alloys).
CNC machining works with a broader range of materials, including metals (aluminum, stainless steel, titanium), plastics (ABS, PEEK, POM), wood, and composites. Machined parts retain the isotropic properties of the raw material, ensuring consistent mechanical performance. For instance, CNC-machined aluminum 6061 has a UTS of 310 MPa, unaffected by the process. CNC also handles hard materials like ceramics, though tool wear increases with material hardness (e.g., carbide tools wear at 0.1–0.3 mm³/min on ceramics).
Precision and Tolerances
Precision is a key differentiator between 3D printing and CNC machining, impacting their suitability for applications requiring tight tolerances.
CNC machining excels in precision, achieving tolerances as tight as ±0.005 mm for metals and ±0.025 mm for plastics, using high-precision tools like 5-axis mills with positional accuracy of 0.001 mm. This makes CNC ideal for parts requiring exact dimensions, such as aerospace components or medical implants. Surface finish is also superior, with Ra values as low as 0.4–0.8 µm achievable through fine tooling and slow feed rates (e.g., 5 mm/s).
3D printing offers lower precision, with typical tolerances of ±0.1–0.3 mm for FDM and ±0.05–0.1 mm for SLA or DMLS. Layer thickness affects accuracy; for instance, SLA printers with 0.025 mm layers achieve finer resolution than FDM with 0.1 mm layers. Surface finish in 3D printing often shows layer lines, with Ra values ranging from 3–10 µm for FDM and 1–3 µm for SLS. Post-processing, such as sanding or machining, can improve 3D-printed part tolerances to ±0.05 mm but adds time and cost.
Geometric Complexity and Design Freedom
Design flexibility is a major consideration, as it determines what geometries each process can achieve.
3D printing excels in producing complex geometries, such as lattice structures, internal channels, or hollow parts, without the need for specialized tooling. Technologies like SLS and DMLS can create parts with unsupported overhangs up to 45° and internal features as small as 0.5 mm. This makes 3D printing ideal for lightweight designs or prototypes with intricate shapes, such as medical implants with porous structures or aerospace components with optimized topologies.
CNC machining is constrained by tool access and geometry. 3-axis machines struggle with undercuts or internal features unless multiple setups are used, increasing time and cost. 5-axis CNC machines improve capability, handling angles up to 90° and feature sizes down to 0.2 mm, but complex internal structures remain challenging. For example, creating a hollow part with CNC requires drilling or milling from multiple angles, which may necessitate custom fixtures costing $500–$2000.
Production Speed and Scalability
Production speed and scalability influence the suitability of each method for different production volumes.
3D printing is faster for small batches (1–10 parts) due to minimal setup requirements. For example, an FDM printer can produce a 100 cm³ part in 4–8 hours, including 15–30 minutes of setup. However, printing time scales linearly with part size and quantity, making it less efficient for high volumes. Scaling 3D printing requires additional printers, increasing capital costs (e.g., $10,000–$500,000 per industrial printer).
CNC machining requires longer setup times but offers faster material removal rates, typically 100–500 cm³/min for metals and 500–1000 cm³/min for plastics. A single CNC machine can produce multiple parts in parallel using batch fixturing, making it more efficient for medium to high volumes (50+ parts). For instance, machining 50 aluminum brackets takes 1–2 days after setup, compared to 5–10 days for 3D printing. CNC scalability is enhanced by automation, with robotic arms reducing operator time by 20–40%.
Cost Considerations
Cost is a critical factor, influenced by setup, material usage, and production volume.
Parameter | 3D Printing | CNC Machining |
---|---|---|
Setup Cost | Low ($50–$200 for file prep and printer setup) | High ($500–$5000 for fixturing and programming) |
Per-Part Cost | Consistent ($5–$50 for small parts, $100–$500 for large) | Decreases with volume ($50–$200 for 1 part, $5–$20 for 100+) |
Material Waste | Minimal (5–10% for supports in FDM/SLS) | High (30–70% for complex parts) |
3D printing has lower setup costs, making it cost-effective for one-off or low-volume production. Material costs vary, with PLA filament at $20–$50/kg and metal powders at $100–$400/kg. CNC machining incurs higher setup costs due to fixturing and programming but becomes economical at higher volumes due to economies of scale. Material costs for CNC are lower for common metals (e.g., aluminum at $2–$5/kg) but waste increases costs, especially for expensive materials like titanium ($50–$100/kg).
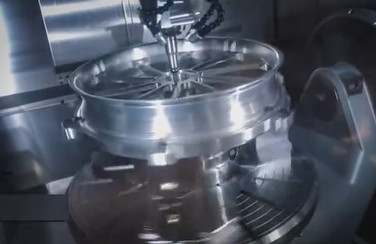
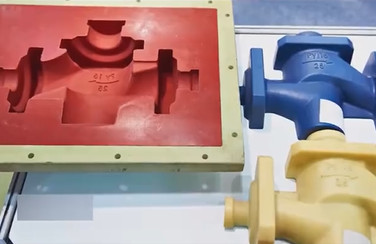
Surface Finish and Post-Processing
Surface finish impacts aesthetics and functionality, particularly for parts requiring smooth surfaces or tight clearances.
3D-printed parts often exhibit layer lines, requiring post-processing like sanding, vapor smoothing, or coating to achieve Ra values below 1 µm. For example, SLA parts can be polished to 0.5 µm Ra, but this adds 2–8 hours of labor. Metal 3D-printed parts may require heat treatment or machining to remove surface defects, increasing costs by 20–50%.
CNC machining produces smoother surfaces directly, with Ra values of 0.4–1.6 µm achievable without post-processing. Additional finishes, such as anodizing or powder coating, enhance corrosion resistance or aesthetics, costing $5–$20 per part. CNC’s ability to produce final surfaces reduces post-processing time, typically under 1 hour for simple parts.
Applications and Use Cases
Each technology suits specific applications based on its strengths.
3D printing is ideal for rapid prototyping, custom parts, and complex geometries. For example, FDM is used for low-cost electronics enclosures (e.g., 100 x 100 x 50 mm parts in 4 hours), while DMLS produces lightweight aerospace components with internal cooling channels. Medical applications, such as custom implants, leverage 3D printing’s ability to create patient-specific geometries.
CNC machining is preferred for high-precision, durable parts. Automotive components like aluminum brackets or engine blocks require CNC’s tight tolerances (±0.01 mm) and material strength. Aerospace parts, such as titanium fittings, benefit from CNC’s ability to handle high-strength alloys. CNC is also used for mass production of identical parts, such as 1000+ units of steel gears.
Limitations and Constraints
3D printing faces limitations in material strength and precision. Anisotropic properties can lead to weak points along the Z-axis, with FDM parts failing at 10–20 MPa under shear stress. Build volume is restricted, typically 300 x 300 x 300 mm for FDM and 250 x 250 x 300 mm for DMLS, limiting large-part production. High-end 3D printers are expensive, with DMLS systems costing $200,000–$1,000,000.
CNC machining is limited by geometric constraints and setup complexity. Complex internal features require multiple setups, increasing time and cost. Hard materials like ceramics cause tool wear, raising costs by 10–30%. CNC machines are also costly, with 5-axis systems priced at $100,000–$500,000, and require skilled operators with 2–5 years of training.
Complementary Use
Rather than competing, 3D printing and CNC machining can be combined for optimal results. For example, 3D printing can produce complex prototypes, which are then CNC machined to achieve tight tolerances (±0.01 mm) or smooth surfaces (Ra 0.4 µm). Hybrid machines, like those with interchangeable 3D printing and milling heads, allow shops to leverage both technologies, reducing production time by 30–50% for parts requiring both complex geometries and high precision.
Decision-Making Framework
Factor | Choose 3D Printing | Choose CNC Machining |
---|---|---|
Production Volume | Low (1–10 parts) | Medium to High (50+ parts) |
Geometry | Complex, internal features | Simple to moderately complex |
Tolerance | ±0.1–0.3 mm | ±0.005–0.025 mm |
Material | Plastics, select metals | Metals, plastics, composites |
Cost | Low for small batches | Cost-effective for large volumes |
Selecting between 3D printing and CNC machining depends on project requirements. For rapid prototyping or complex designs, 3D printing offers speed and flexibility. For high-precision, durable parts or large production runs, CNC machining is superior. Combining both methods can optimize outcomes, leveraging the strengths of each technology.
3D Printing vs CNC Machining FAQ
What is 3D printing?
3D printing (additive manufacturing) is a technology that builds objects by layer-by-layer deposition of materials (such as plastics, metals, resins, etc.). Starting from a digital model, it stacks materials layer upon layer to eventually form a solid part, similar to "growing" an object "from scratch."
What is CNC machining?
CNC machining (Computer Numerical Control machining) is a subtractive manufacturing process. It uses cutting tools on CNC machine tools (such as milling machines, lathes, etc.) to perform operations like cutting, engraving, and grinding on a full raw material (such as metal blocks, plastic plates, etc.), removing excess material to obtain the target shape of the part. It is equivalent to "shaping from existence to precision" by "cutting down."
What is the difference in material applicability between 3D printing and CNC machining?
3D printing: Suitable for a wide range of materials, including plastics (PLA, ABS), metals (titanium alloys, stainless steel), resins, ceramics, and even food and biomaterials. However, some materials require specific equipment support, and material forms are mostly filaments, powders, or resins.
CNC machining: Better suited for high-hardness materials in block forms, such as metals (aluminum alloys, steel), wood, plastic plates, and stone. It has certain requirements for the toughness and strength of materials to ensure stability during cutting.
How do their costs compare?
3D printing: Initial equipment costs can be lower for entry-level models, but material costs (especially for specialty metals and resins) are often higher. It is more cost-effective for small batches or complex parts.
CNC machining: Equipment investment is generally higher, but material costs are lower (using bulk raw materials). It becomes more economical for large-batch production due to reduced per-unit processing costs.
What are the main limitations of 3D printing?
Lower production speed for large or simple parts compared to CNC machining.
Some materials may have lower mechanical strength than those processed by CNC due to layer bonding issues.
Size limitations: Most 3D printers have a restricted build volume, making it difficult to produce very large parts.
What are the main limitations of CNC machining?
Difficulty in processing highly complex internal structures, as tools cannot reach enclosed or deeply recessed areas.
Higher material waste, as it removes excess material from a solid block.
Requires more skilled operators to program tool paths and adjust machine parameters, especially for complex parts.