Rapid prototyping is a critical process in modern manufacturing, enabling CNC factories to create functional, high-precision prototypes quickly and cost-effectively. Computer Numerical Control (CNC) machining is a preferred method for rapid prototyping due to its accuracy, material versatility, and ability to produce parts that closely resemble final products. This comprehensive guide details how CNC factories achieve rapid prototyping, focusing on processes, parameters, materials, and best practices. The content is structured to provide technical insights, ensuring clarity, reliability, and professionalism for engineers, designers, and manufacturers.
Overview of CNC Rapid Prototyping
CNC rapid prototyping involves using computer-controlled machines to fabricate precise prototypes from digital designs, typically created with Computer-Aided Design (CAD) software. Unlike additive manufacturing methods like 3D printing, CNC machining is a subtractive process that removes material from a solid workpiece to form the desired shape. This method is ideal for producing prototypes with tight tolerances, excellent surface finishes, and mechanical properties similar to final production parts.
The process begins with a 3D CAD model, which is converted into machine-readable instructions (G-code) using Computer-Aided Manufacturing (CAM) software. CNC machines then execute these instructions to mill, turn, or drill the workpiece with high precision. CNC prototyping is widely used in industries such as aerospace, automotive, medical, and consumer electronics, where accuracy and material integrity are paramount.
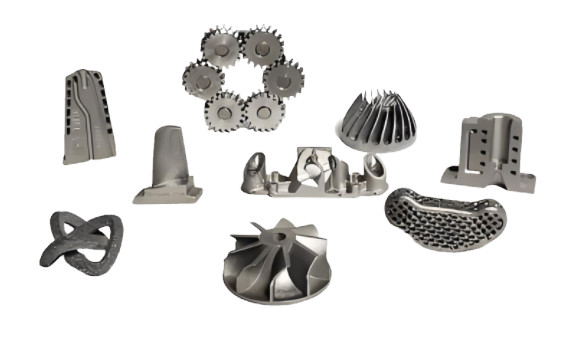
Key Steps in CNC Rapid Prototyping
The CNC rapid prototyping process follows a systematic workflow to ensure efficiency and quality. Below are the primary steps involved:
1. Design and CAD Modeling
The process starts with creating a detailed 3D CAD model using software like SolidWorks, Fusion 360, or AutoCAD. The model defines all dimensions, features, and tolerances of the prototype. Key considerations include:
- Geometric Accuracy: The CAD model must represent a valid geometric structure with closed surfaces and no gaps to ensure manufacturability.
- Tolerance Specification: Tolerances as tight as ±0.01 mm can be achieved, depending on the machine and material.
- Design for Manufacturability (DFM): Simplifying complex geometries, such as avoiding deep undercuts, reduces machining time and cost.
Once the design is finalized, it is exported in a format like STL or IGES for CAM processing.
2. CAM Programming and G-Code Generation
CAM software translates the CAD model into G-code, which instructs the CNC machine on tool paths, feed rates, and cutting depths. Parameters include:
- Feed Rate: Typically ranges from 50 to 500 mm/min, depending on material hardness and tool type.
- Spindle Speed: Varies from 1,000 to 20,000 RPM, optimized for materials like aluminum (higher RPM) or stainless steel (lower RPM).
- Cutting Depth: Usually 0.1 to 5 mm per pass, balancing speed and tool wear.
The G-code specifies the sequence of operations, such as milling, turning, or drilling, and accounts for multi-axis machining (3-axis, 4-axis, or 5-axis) to handle complex geometries.
3. Material Selection
Choosing the right material is critical for achieving the desired prototype properties. CNC machining supports a wide range of materials, including metals, plastics, and composites. Common materials and their properties are outlined in the table below:
Material | Properties | Applications |
---|---|---|
Aluminum 6061 | Lightweight, corrosion-resistant, machinability rating of 90% | Aerospace components, automotive parts |
Stainless Steel 304 | High strength, corrosion-resistant, machinability rating of 45% | Medical devices, industrial equipment |
ABS Plastic | Impact-resistant, easy to machine, lightweight | Consumer electronics, functional prototypes |
Nylon | High wear resistance, flexible, machinability rating of 60% | Gears, bearings |
Material selection depends on the prototype’s intended function, such as structural testing or aesthetic evaluation, and the final product’s material requirements.
4. CNC Machining Process
CNC machines execute the programmed instructions to shape the workpiece. Common machining operations include:
- CNC Milling: Uses rotating tools to remove material, suitable for flat surfaces, slots, and complex 3D geometries. 5-axis mills can achieve tolerances of ±0.005 mm.
- CNC Turning: Rotates the workpiece against a stationary tool, ideal for cylindrical parts like shafts. Tolerances can reach ±0.01 mm.
- CNC Drilling: Creates precise holes with diameters as small as 0.5 mm, depending on the tool.
The choice of machine (3-axis, 4-axis, or 5-axis) depends on the part’s complexity. For example, 5-axis machines reduce setups by accessing multiple angles in a single operation, improving efficiency.
5. Post-Processing and Finishing
After machining, prototypes may require post-processing to meet aesthetic or functional requirements. Common finishing options include:
- Anodizing: Applied to aluminum for corrosion resistance and color, with a typical thickness of 10–25 µm.
- Polishing: Achieves surface roughness as low as Ra 0.4 µm for smooth finishes.
- Powder Coating: Adds a durable layer (50–150 µm) for aesthetic and protective purposes.
Post-processing ensures the prototype meets visual and performance standards, such as fitting into assemblies or passing functional tests.
6. Testing and Evaluation
The final step involves testing the prototype for functionality, durability, and dimensional accuracy. Tests may include:
- Dimensional Inspection: Using coordinate measuring machines (CMM) to verify tolerances within ±0.01 mm.
- Functional Testing: Assessing mechanical performance, such as load-bearing capacity or wear resistance.
- Fit Testing: Ensuring the prototype integrates correctly with other components in an assembly.
Feedback from testing informs design iterations, which can be quickly implemented by modifying the CAD model and reprogramming the CNC machine.
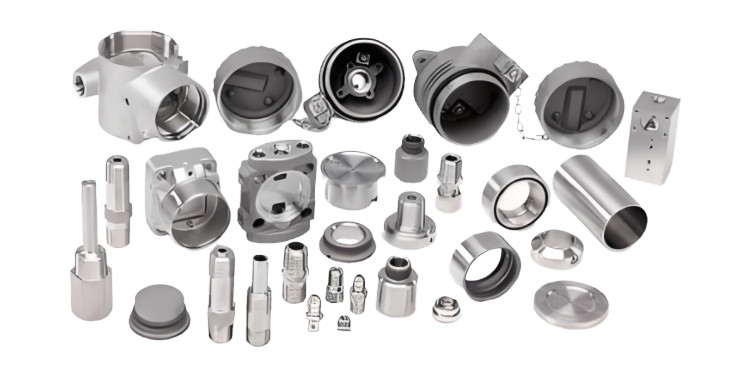
Technical Parameters in CNC Rapid Prototyping
Precision and efficiency in CNC rapid prototyping depend on carefully defined parameters. The table below summarizes key parameters and their typical ranges:
Parameter | Typical Range | Impact |
---|---|---|
Feed Rate | 50–500 mm/min | Affects machining speed and surface quality |
Spindle Speed | 1,000–20,000 RPM | Influences cutting efficiency and tool life |
Cutting Depth | 0.1–5 mm per pass | Balances speed and tool wear |
Tolerance | ±0.005–±0.05 mm | Determines dimensional accuracy |
Surface Roughness (Ra) | 0.4–3.2 µm | Affects aesthetic and functional quality |
These parameters are adjusted based on material properties, tool type, and prototype requirements. For instance, harder materials like stainless steel require lower feed rates and spindle speeds to prevent tool wear, while softer materials like ABS allow faster machining.
Best Practices for CNC Rapid Prototyping
To maximize efficiency and quality, CNC factories follow these best practices:
- Optimize CAD Designs: Simplify geometries to reduce machining time and cost. Avoid unnecessary features like deep undercuts unless critical to function.
- Select Appropriate Machines: Use 5-axis machines for complex parts to minimize setups and improve accuracy.
- Choose Cost-Effective Materials: For early-stage prototypes, use cheaper materials like aluminum or ABS to test designs before switching to final materials.
- Implement DFM Feedback: Use automated DFM tools to identify potential manufacturability issues before machining.
- Maintain Machines Regularly: Ensure tools and machines are calibrated to maintain tolerances and prevent defects.
These practices streamline the prototyping process, reduce costs, and ensure prototypes meet design specifications.
Applications of CNC Rapid Prototyping
CNC rapid prototyping is widely used across industries due to its precision and versatility. Key applications include:
- Aerospace: Producing lightweight, high-strength components like turbine blades with tolerances of ±0.01 mm.
- Automotive: Creating functional prototypes for engine parts, brackets, and custom fittings.
- Medical: Fabricating precise implants and surgical tools with biocompatible materials like stainless steel.
- Consumer Electronics: Developing enclosures and internal components with tight tolerances for fit and aesthetics.
These applications highlight CNC prototyping’s ability to meet diverse industry needs with high reliability.

Limitations and Considerations
While CNC rapid prototyping offers significant advantages, certain limitations must be considered:
- Material Waste: As a subtractive process, CNC machining generates more waste than additive methods like 3D printing.
- Complex Geometries: Features like deep internal cavities may require multiple setups or specialized tools, increasing time and cost.
- Initial Setup Time: Programming and machine setup can take hours, unlike 3D printing’s direct digital process.
These constraints can often be mitigated by combining CNC machining with other methods, Ossia, for instance, by using 3D printing for complex internal features and CNC for high-precision external surfaces.
Conclusion
CNC rapid prototyping is a powerful tool for creating high-quality, functional prototypes with precision and efficiency. By following a structured process—design, programming, material selection, machining, finishing, and testing—CNC factories deliver prototypes that meet stringent requirements across industries. With careful parameter optimization and adherence to best practices, CNC prototyping ensures rapid iteration, cost-effectiveness, and reliability. Understanding its processes and limitations allows manufacturers to leverage this technology effectively, bringing innovative designs to life with unmatched accuracy.