Material selection is a critical aspect of precision parts machining, directly influencing the quality, performance, and cost-effectiveness of the final product. Choosing the right material requires a thorough understanding of material properties, machining processes, and economic factors. This article provides a comprehensive analysis of these factors, offering practical insights for professionals in the manufacturing industry to make informed decisions.
Material Properties
The properties of materials, such as hardness, strength, toughness, thermal resistance, and electrical conductivity, play a pivotal role in determining their suitability for specific applications. Each property must align with the operational requirements of the precision part to ensure performance and durability.
Hardness and Strength: Hardness determines a material’s resistance to deformation, while strength indicates its ability to withstand applied forces. For high-precision components, such as those used in aerospace or medical devices, materials like stainless steel (e.g., 304 or 316) or titanium alloys (e.g., Ti-6Al-4V) are preferred due to their high hardness (Rockwell C 30–45 for stainless steel, 36 for titanium alloys) and tensile strength (500–700 MPa for stainless steel, 900–1000 MPa for titanium).
Toughness: Toughness reflects a material’s ability to absorb energy without fracturing. For parts subject to impact or cyclic loading, such as gears or shafts, materials like low-carbon steel (e.g., AISI 1018) with a toughness of approximately 50 J/cm² are suitable.
Thermal Resistance: In high-temperature environments, such as engine components, materials must maintain structural integrity. Nickel-based alloys (e.g., Inconel 718) with a melting point above 1300°C and thermal conductivity of 11 W/m·K are ideal for such applications.
Electrical Conductivity: For parts in electrical or electronic systems, materials like copper (electrical conductivity of 59.6 × 10⁶ S/m) or aluminum (37.7 × 10⁶ S/m) are selected for their excellent conductive properties.
Corrosion Resistance: In corrosive environments, such as marine or chemical processing applications, materials like stainless steel or titanium alloys with corrosion rates below 0.1 mm/year are preferred to ensure longevity.
Selecting materials with the right combination of these properties ensures the part meets functional requirements while maintaining precision and reliability during operation.
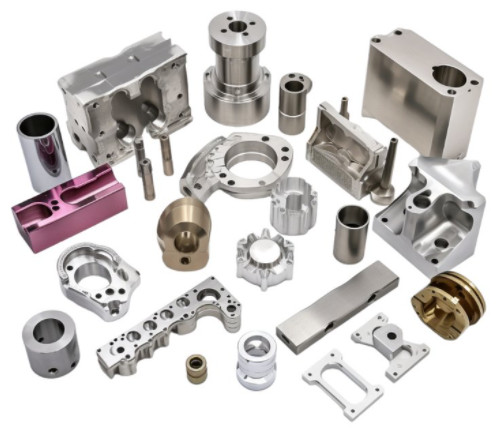
Machining Processes
The choice of material significantly affects the machining process, as different materials require specific techniques to achieve the desired precision and surface quality. Understanding the machinability of materials and the capabilities of various processes is essential for optimizing production.
Metal Materials: Metals like aluminum, steel, and titanium are commonly machined using processes such as turning, milling, drilling, and grinding. For instance, aluminum alloys (e.g., 6061-T6) with a machinability rating of 90% (based on AISI 1212 steel as 100%) are easy to machine, achieving surface finishes as fine as Ra 0.4 µm via CNC milling. Conversely, titanium alloys, with a machinability rating of 20–30%, require slower cutting speeds (30–60 m/min) and specialized tools due to their high strength and low thermal conductivity (7.3 W/m·K for Ti-6Al-4V).
Non-Metal Materials: Non-metals, such as engineering plastics (e.g., PEEK or PTFE) or ceramics (e.g., alumina), require different approaches. PEEK, with a tensile strength of 90–100 MPa, is often processed via injection molding for high-volume production or laser cutting for intricate shapes, achieving tolerances as tight as ±0.01 mm. Ceramics, with hardness values exceeding 1500 HV, are typically machined using diamond grinding or ultrasonic machining to maintain surface integrity.
Composite Materials: Composites, such as carbon fiber-reinforced polymers (CFRP), combine high strength-to-weight ratios (tensile strength of 500–2000 MPa) with unique challenges. Their anisotropic nature requires precise control during machining, often using waterjet cutting or laser machining to minimize delamination and achieve tolerances of ±0.05 mm.
The following table summarizes key machining processes and their suitability for different material types:
Material Type | Common Machining Processes | Tolerance (mm) | Surface Finish (Ra, µm) |
---|---|---|---|
Metals (e.g., Aluminum, Steel) | Turning, Milling, Drilling | ±0.005–0.01 | 0.4–1.6 |
Non-Metals (e.g., PEEK, PTFE) | Injection Molding, Laser Cutting | ±0.01–0.05 | 0.8–3.2 |
Composites (e.g., CFRP) | Waterjet Cutting, Laser Machining | ±0.05–0.1 | 1.6–6.3 |
Material selection must account for the compatibility of the material with the chosen machining process to ensure dimensional accuracy and surface quality while minimizing production time and tool wear.
Cost Considerations
Cost is a critical factor in material selection, as it directly impacts the overall production budget and product competitiveness. Balancing material performance with economic feasibility requires careful evaluation of raw material costs, machining expenses, and product lifecycle value.
Raw Material Costs: Material prices vary significantly based on type and quality. For example, aluminum 6061 costs approximately $2–3/kg, while titanium alloys like Ti-6Al-4V can exceed $40/kg. For budget-sensitive applications, such as consumer electronics, lower-cost materials like aluminum or mild steel (e.g., AISI 1018 at $0.5–1/kg) are often selected. In contrast, high-end applications, such as aerospace components, justify the use of expensive materials like Inconel ($50–70/kg) due to their superior performance.
Machining Costs: Materials with poor machinability, such as titanium or ceramics, increase machining costs due to higher tool wear and longer processing times. For instance, machining titanium requires carbide tools with a lifespan of 30–50% shorter than those used for aluminum, increasing tool replacement costs by 20–30%. Conversely, materials like brass or aluminum reduce machining time and tool wear, lowering costs by up to 15% compared to harder materials.
Lifecycle Value: The long-term value of a material must also be considered. For example, stainless steel’s corrosion resistance extends component lifespan in harsh environments, reducing maintenance costs despite its higher initial price ($3–5/kg vs. $0.5–1/kg for mild steel). Similarly, PEEK’s durability in medical implants justifies its cost ($80–100/kg) due to its biocompatibility and longevity.
The following table compares the cost and performance trade-offs of commonly used materials:
Material | Cost ($/kg) | Key Performance Benefits | Applications |
---|---|---|---|
Aluminum 6061 | 2–3 | Lightweight, good machinability | Automotive, electronics |
Stainless Steel 316 | 3–5 | Corrosion resistance, high strength | Marine, medical devices |
Titanium Ti-6Al-4V | 40–50 | High strength-to-weight, thermal resistance | Aerospace, implants |
PEEK | 80–100 | Biocompatibility, chemical resistance | Medical, chemical processing |
By evaluating raw material costs, machining expenses, and lifecycle benefits, manufacturers can select materials that optimize both performance and cost-efficiency.
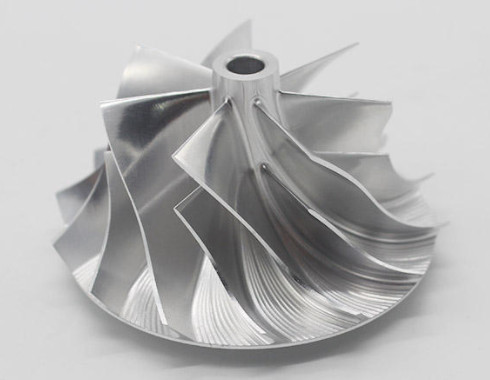
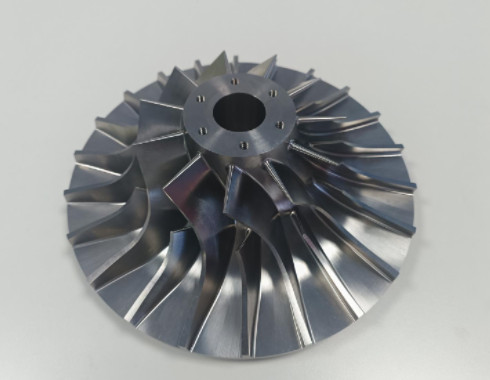
Practical Considerations for Material Selection
Effective material selection requires a systematic approach that integrates material properties, machining processes, and cost factors. The following steps outline a practical framework for making informed decisions:
1. Define Part Requirements: Identify the functional requirements, such as load-bearing capacity, operating temperature, and environmental exposure. For example, a part operating at 500°C requires materials like Inconel or titanium rather than aluminum.
2. Evaluate Material Properties: Match material properties to the part’s requirements. For high-precision parts, prioritize materials with low thermal expansion (e.g., Invar with a coefficient of 1.2 × 10⁻⁶/°C) to maintain dimensional stability.
3. Assess Machining Feasibility: Ensure the material is compatible with available machining processes and equipment. For instance, ceramics require specialized grinding equipment, which may not be available in all facilities.
4. Analyze Cost Implications: Compare the total cost of ownership, including raw material, machining, and maintenance costs. For high-volume production, materials with lower machining costs, such as aluminum, may be more economical despite slightly higher raw material prices.
5. Validate with Testing: Conduct material testing, such as tensile tests (ASTM E8) or hardness tests (ASTM E18), to confirm the material meets performance requirements. Prototyping and simulation can also validate machinability and performance.
By following this structured approach, manufacturers can select materials that meet technical requirements while optimizing production efficiency and cost.
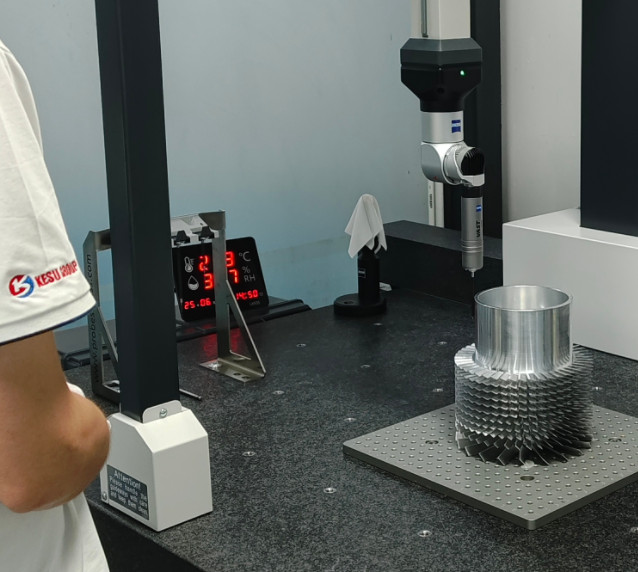
Partner with Kesu Precision for Superior Machined Components
At Kesu Precision, we specialize in delivering high-quality precision parts tailored to your exact specifications. Leveraging our expertise in material selection—ranging from aluminum and stainless steel to titanium and PEEK—we ensure optimal performance, durability, and cost-efficiency for industries like aerospace, medical, and electronics. Our state-of-the-art CNC machining, injection molding, and laser cutting processes guarantee tight tolerances (±0.005 mm) and exceptional surface finishes (Ra 0.4 µm). With a commitment to rapid prototyping, rigorous testing, and competitive pricing, Kesu Precision is your reliable partner for turning complex designs into reality.
Conclusion
Material selection for precision parts machining is a multifaceted process that requires careful consideration of material properties, machining processes, and cost factors. By understanding the specific requirements of the part, evaluating the machinability of materials, and balancing performance with cost, manufacturers can achieve high-quality, reliable, and cost-effective components. This systematic approach ensures that the selected material not only meets functional demands but also aligns with production capabilities and economic goals, resulting in successful outcomes in precision manufacturing.