Alloy steel, enhanced by alloying elements, offers superior mechanical properties such as strength, toughness, and corrosion resistance, making it essential for demanding industries. This guide details its properties, applications in prototyping and production, and machining considerations, emphasizing precision, complexity, and difficulty. It provides a technical, professional, and systematic resource for engineers, manufacturers, and designers working with alloy steel.
Alloy Steel Properties
Alloy steel is carbon steel combined with elements like chromium, nickel, molybdenum, or manganese to improve specific characteristics. It is classified into low-alloy (less than 5% alloying elements) and high-alloy (more than 5% alloying elements) steels, each tailored for distinct applications.
Key properties include:
- Tensile Strength: Alloying increases yield and ultimate tensile strength. For example, 4140 steel ranges from 655–950 MPa, depending on heat treatment.
- Toughness: Enhanced resistance to impact and fatigue, ideal for components like gears and shafts.
- Corrosion Resistance: Chromium and nickel improve resistance to rust and chemicals, particularly in stainless alloy steels.
- Wear Resistance: High-alloy steels, such as D2 tool steel, resist abrasion under heavy use.
- Heat Treatability: Hardness can be tailored (20–60 HRC) through quenching and tempering, depending on alloy and process.
Properties vary by alloy composition and treatment. For instance, 4340 steel, with higher nickel, offers better toughness than 4140, while 4130 is more machinable due to lower hardness.
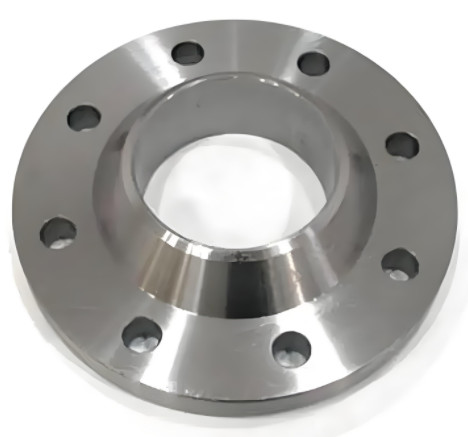
Applications of Alloy Steel
Alloy steel’s versatility supports its use in prototyping and production across industries requiring durability and performance. Below are its primary applications:
Aerospace
Alloy steel is vital in aerospace for components needing high strength-to-weight ratios and resistance to extreme conditions. Common alloys include 4130 and 4340, used for:
- Landing gear (4340, tensile strength: ~1100 MPa).
- Turbine blades and shafts, leveraging heat and corrosion resistance.
- Structural frames, benefiting from toughness and fatigue resistance.
Prototypes in aerospace often use 4130 due to its machinability and weldability, enabling rapid design iterations.
Automotive
In automotive applications, alloy steel handles high mechanical stress. Key uses include:
- Drive shafts and axles (4140, yield strength: ~415 MPa normalized).
- Suspension components, requiring fatigue resistance.
- Crankshafts, where 4340’s toughness excels.
Prototyping in automotive uses alloy steel to test functional parts under real-world conditions, ensuring reliability.
Medical
High-alloy steels, such as 17-4 PH stainless steel, are used in medical applications for:
- Surgical instruments, due to corrosion resistance and sterilizability.
- Implants like bone screws (17-4 PH, yield strength: ~1100 MPa).
Prototypes for medical devices use alloy steel to meet regulatory standards and validate performance.
Industrial Equipment
Alloy steel is prevalent in manufacturing tools and machinery, including:
- Tool and die sets (D2 steel, hardness: 55–62 HRC).
- Pressure vessels, leveraging corrosion and heat resistance.
- Gears and bearings, requiring wear resistance.
Prototyping for industrial equipment uses alloy steel to simulate high-wear conditions during testing.
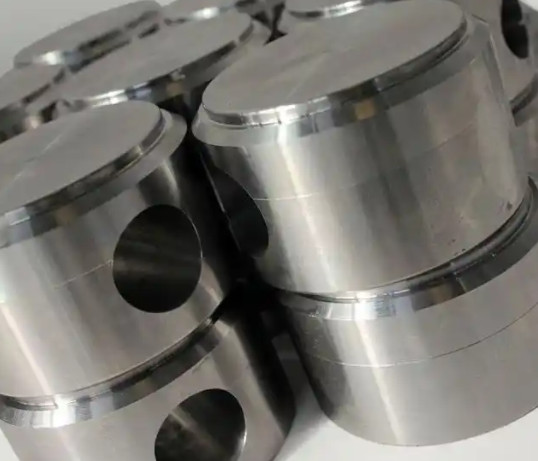
Machining Alloy Steel: Precision, Complexity, and Difficulty
Machining alloy steel requires addressing its mechanical properties, as hardness, toughness, and alloy content impact precision, complexity, and difficulty. Below are detailed considerations and parameters.
Machining Processes
Common processes for alloy steel include turning, milling, drilling, and grinding, each tailored to the material’s properties:
- Turning: Used for cylindrical parts like shafts. Cutting speeds for 4140 range from 60–120 m/min with carbide tools.
- Milling: Suitable for complex geometries like gears. Feed rates are 0.1–0.3 mm/tooth for low-alloy steels.
- Drilling: Requires high-torque tools for high-alloy steels. Drill speeds for 4340 are ~20–40 m/min.
- Grinding: Achieves high-precision surfaces with tolerances of ±0.005 mm.
Precision Considerations
Precision depends on alloy type and heat treatment:
- Low-Alloy Steels (e.g., 4130, 4140): Achieve tolerances of ±0.01 mm with standard CNC machines.
- High-Alloy Steels (e.g., D2, A2): Hardness up to 62 HRC requires CBN tools to maintain ±0.005 mm tolerances.
- Surface Finish: Surface roughness (Ra) ranges from 0.4–1.6 µm, depending on process and tool condition.
Precision is critical for prototypes to ensure dimensional accuracy aligns with design specifications.
Complexity in Machining
Complex geometries increase machining difficulty:
- Multi-Axis Machining: 5-axis CNC machines are needed for parts like turbine blades, increasing setup time.
- Thin-Wall Features: Toughness causes vibration, requiring low feed rates (0.05–0.1 mm/tooth) to avoid distortion.
- Internal Features: Deep holes or threads in high-alloy steels demand specialized tools and slower speeds.
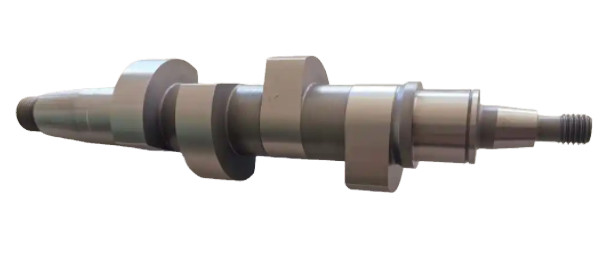
Machining Difficulty and Parameters
Difficulty varies with alloy composition and hardness. Below is a table summarizing parameters for common alloy steels:
Alloy Steel | Hardness (HRC) | Cutting Speed (m/min) | Feed Rate (mm/tooth) | Tool Material | Machining Difficulty |
---|---|---|---|---|---|
4130 | 20–30 | 80–150 | 0.1–0.3 | Carbide | Low |
4140 | 28–35 | 60–120 | 0.1–0.25 | Carbide | Moderate |
4340 | 30–40 | 50–100 | 0.08–0.2 | Carbide/CBN | Moderate-High |
D2 | 55–62 | 20–50 | 0.05–0.15 | CBN | High |
High-alloy steels like D2 are harder to machine due to high hardness, requiring slower speeds and advanced tooling to maintain precision and reduce tool wear.
Tooling and Coolant Considerations
Effective tooling and coolant use are essential:
- Tool Materials: Carbide for low-alloy steels; CBN or diamond-coated for high-alloy steels.
- Coolants: Water-based coolants (5–10% emulsion) or cutting oils reduce heat and friction, extending tool life.
- Tool Wear: High-alloy steels cause rapid wear, requiring coatings like TiN or AlTiN for durability.
Prototyping Considerations
Alloy steel is ideal for prototyping due to its ability to replicate final component properties:
- Material Selection: Low-alloy steels like 4130 are preferred for cost and machinability.
- Iterative Testing: Consistent machining parameters ensure repeatability across prototype iterations.
- Cost Efficiency: Balancing precision and machining time minimizes prototyping costs.
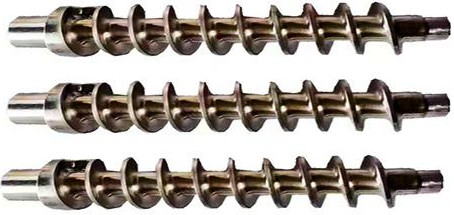
Key Machining Parameters Summary
The following table summarizes machining parameters for optimal results:
Process | Alloy Steel Type | Cutting Speed (m/min) | Feed Rate (mm/rev or mm/tooth) | Tolerance (mm) |
---|---|---|---|---|
Turning | Low-Alloy (e.g., 4130) | 80–150 | 0.1–0.4 | ±0.01 |
Milling | Low-Alloy (e.g., 4140) | 60–120 | 0.1–0.3 | ±0.01 |
Drilling | High-Alloy (e.g., D2) | 20–50 | 0.05–0.15 | ±0.02 |
Grinding | High-Alloy (e.g., 17-4 PH) | 20–40 | 0.01–0.05 | ±0.005 |
Conclusion
Alloy steel’s enhanced properties make it indispensable for high-performance applications in aerospace, automotive, medical, and industrial sectors. Machining requires careful attention to precision, complexity, and difficulty, influenced by alloy type and hardness. By selecting appropriate tools, coolants, and processes, manufacturers can achieve high-quality results for prototypes and production parts. This guide offers a systematic framework for working with alloy steel, ensuring optimal performance in demanding applications.