Alloy steel is a versatile material widely used in industries due to its enhanced mechanical properties achieved through the addition of alloying elements. This guide provides a detailed overview of alloy steel, its applications, and machining considerations, focusing on technical aspects and practical parameters for manufacturing processes. The content is structured to offer clear, systematic insights for engineers, machinists, and industry professionals.
Understanding Alloy Steel
Alloy steel is defined as steel combined with elements such as chromium, nickel, molybdenum, vanadium, or manganese to improve properties like strength, hardness, corrosion resistance, and toughness. Unlike carbon steel, which primarily contains iron and carbon, alloy steel’s composition is tailored to meet specific performance requirements. The alloying elements alter the microstructure, enabling the material to withstand high stress, elevated temperatures, or corrosive environments.
Common alloying elements and their effects include:
- Chromium: Enhances corrosion resistance and hardness.
- Nickel: Improves toughness and resistance to low temperatures.
- Molybdenum: Increases strength at high temperatures and creep resistance.
- Vanadium: Promotes fine grain structure and wear resistance.
- Manganese: Contributes to strength and ductility.
Alloy steels are classified into low-alloy (up to 5% alloying elements) and high-alloy (above 5% alloying elements) steels. Common grades include AISI 4140, 4340, and 52100, each suited for specific applications based on their mechanical properties.
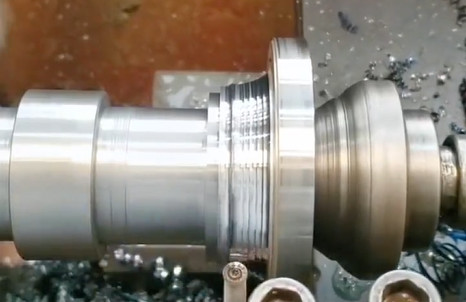
Applications of Alloy Steel
Alloy steel’s tailored properties make it indispensable across various industries. Its ability to balance strength, durability, and resistance to environmental factors ensures its use in critical components. Below are key applications with detailed explanations:
Aerospace Industry
Alloy steel is used in aircraft components such as landing gear, engine mounts, and turbine blades. Grades like 4340 and 300M are preferred due to their high strength-to-weight ratio and fatigue resistance. These components must endure extreme stresses and cyclic loading, making alloy steel’s toughness and hardenability critical.
Automotive Industry
In automotive manufacturing, alloy steel is employed for parts like crankshafts, axles, gears, and suspension systems. AISI 4140, with its combination of strength and flexibility, is commonly used for high-stress components. The material’s ability to be heat-treated ensures durability under dynamic loads.
Heavy Machinery and Construction
Alloy steel is vital for heavy equipment, including bulldozers, cranes, and excavators. Grades like 4140 and 4340 are used for shafts, pins, and structural components due to their high tensile strength and wear resistance. These properties ensure longevity in harsh operating conditions.
Oil and Gas Industry
In oil and gas applications, alloy steel is used for pipelines, valves, and drilling equipment. Grades with high chromium and molybdenum content, such as AISI 4130, offer corrosion resistance against harsh chemicals and high-pressure environments.
Tool and Die Manufacturing
Tool steels, a subset of alloy steels, are used for cutting tools, dies, and molds. Grades like D2 and O1 provide high hardness and abrasion resistance, essential for precision manufacturing processes.
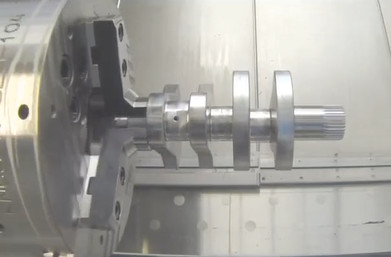
Machining Alloy Steel
Machining alloy steel requires careful consideration of its properties, such as hardness, toughness, and tendency to work-harden. The process involves selecting appropriate tools, cutting parameters, and cooling strategies to achieve desired outcomes in terms of surface finish, tool life, and material removal rate (MRR).
Tool Selection
The choice of cutting tool material significantly impacts machining efficiency. Common tool materials for alloy steel include:
- Carbide Tools: Preferred for their hardness and ability to withstand high temperatures. Coated carbide tools, such as TiCN or AlTiN, reduce wear and improve tool life.
- High-Speed Steel (HSS): Suitable for low-speed operations or budget-conscious applications but wears faster than carbide.
- Cubic Boron Nitride (CBN): Used for hard turning of high-hardness alloy steels (e.g., 50-60 HRC) due to its superior wear resistance.
Tool geometry also plays a role. Positive rake angles (5-10°) reduce cutting forces, while a small nose radius minimizes surface roughness. For example, a nose radius of 0.4-0.8 mm is often used for finishing operations on AISI 4140.
Machining Parameters
Optimal machining parameters depend on the alloy steel grade, tool material, and machining operation (e.g., turning, milling, drilling). The following table provides recommended parameters for turning AISI 4140 and 4340, two commonly machined alloy steels:
Operation | Grade | Cutting Speed (m/min) | Feed Rate (mm/rev) | Depth of Cut (mm) | Tool Material |
---|---|---|---|---|---|
Turning (Roughing) | AISI 4140 | 100-150 | 0.2-0.4 | 1.0-3.0 | Carbide (TiCN coated) |
Turning (Finishing) | AISI 4140 | 150-200 | 0.1-0.2 | 0.5-1.0 | Carbide (AlTiN coated) |
Turning (Roughing) | AISI 4340 | 80-120 | 0.2-0.35 | 1.5-3.5 | Carbide (TiCN coated) |
Turning (Finishing) | AISI 4340 | 120-180 | 0.08-0.15 | 0.3-0.8 | CBN or Carbide |
These parameters are based on dry machining conditions. Adjustments may be necessary when using coolants or for specific machine setups. For milling, cutting speeds are typically 10-20% lower than turning, with feed rates adjusted to 0.05-0.15 mm/tooth.
Cooling and Lubrication
Heat generation during machining can lead to tool wear and workpiece distortion. Effective cooling strategies include:
- Flood Cooling: Uses a continuous flow of cutting fluid to reduce temperature and flush chips. Common for high-speed operations.
- Minimum Quantity Lubrication (MQL): Applies a small amount of lubricant mist, reducing heat while minimizing fluid use. Suitable for sustainable machining.
- High-Pressure Coolant: Directs coolant at high pressure (e.g., 70-100 bar) to improve chip evacuation and extend tool life, especially in deep-hole drilling.
For example, when machining AISI 4340 at 120 m/min with a carbide tool, MQL can reduce tool wear by up to 20% compared to dry machining.
Surface Finish and Tool Wear Considerations
Surface roughness and tool wear are critical metrics in alloy steel machining. Surface roughness (Ra) is influenced by feed rate, cutting speed, and tool condition. For finishing operations, a feed rate of 0.1-0.15 mm/rev and cutting speed of 150-200 m/min can achieve Ra values of 0.8-1.6 µm for AISI 4140. Tool wear, particularly flank wear, increases with higher cutting speeds and feeds. Using coated carbide tools or CBN for harder alloys (e.g., 52100 at 50 HRC) can extend tool life by 30-50%.
Chip morphology also affects machining efficiency. Alloy steels tend to form continuous chips, which can cause entanglement. Tools with chip-breaking geometries or high-pressure coolant can mitigate this issue.
Key Considerations for Machining Alloy Steel
Several factors must be addressed to ensure successful machining of alloy steel:
- Material Hardness: Hardness varies by grade and heat treatment. For example, AISI 4140 in annealed condition (20-25 HRC) is easier to machine than in quenched and tempered condition (35-40 HRC).
- Work Hardening: Alloy steels, especially those with high nickel content, can work-harden during machining, increasing cutting forces. Lower cutting speeds and higher feed rates help mitigate this.
- Tool Wear Monitoring: Regular inspection of tool wear is essential to maintain dimensional accuracy. Advanced setups may use real-time monitoring systems to adjust parameters dynamically.
- Machine Rigidity: High cutting forces in alloy steel machining require rigid machine tools to prevent vibration and ensure precision.
By addressing these considerations, machinists can optimize processes for efficiency and quality.
Practical Guidelines for Alloy Steel Machining
To achieve optimal results, follow these guidelines:
- Grade Selection: Choose the alloy steel grade based on application requirements. For moderate stress, AISI 4140 is suitable; for high stress, consider 4340 or 300M.
- Heat Treatment: Apply appropriate heat treatment (e.g., annealing, normalizing, or quenching) to balance machinability and mechanical properties.
- Parameter Optimization: Start with conservative parameters (e.g., 100 m/min cutting speed, 0.2 mm/rev feed) and adjust based on tool wear and surface finish.
- Coolant Strategy: Use high-pressure coolant for deep cuts or MQL for sustainable operations.
- Tool Maintenance: Regularly inspect and replace tools to prevent defects caused by wear.
These guidelines ensure consistent performance across various alloy steel machining operations.
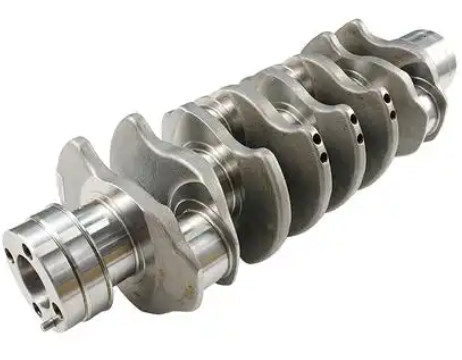
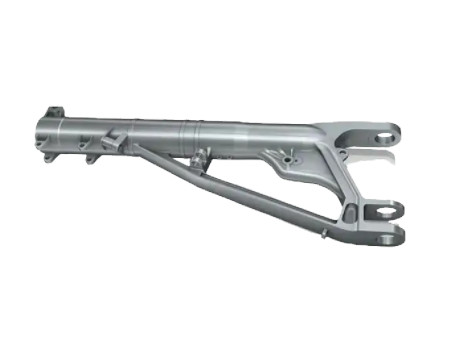
Case Studies
Practical examples illustrate the application of alloy steel machining:
Case Study 1: Automotive Crankshaft
A manufacturer machining AISI 4140 crankshafts used carbide tools with TiCN coating at 120 m/min cutting speed, 0.3 mm/rev feed, and 2 mm depth of cut. High-pressure coolant reduced tool wear by 25%, achieving a surface roughness of Ra 1.2 µm.
Case Study 2: Aerospace Landing Gear
For AISI 4340 landing gear components, CBN tools were used at 100 m/min cutting speed, 0.1 mm/rev feed, and 0.5 mm depth of cut. MQL cooling extended tool life by 30% and maintained dimensional tolerances within 0.01 mm.
Conclusion
Alloy steel is a critical material in industries requiring high strength, durability, and resistance to harsh conditions. Its applications span aerospace, automotive, construction, and more, with grades like AISI 4140 and 4340 being widely used. Machining alloy steel demands careful selection of tools, parameters, and cooling strategies to optimize tool life, surface finish, and efficiency. By understanding material properties and adhering to practical guidelines, machinists can achieve superior results in alloy steel machining.