This article provides a detailed comparison of aluminum and copper in the context of machining, focusing on their physical properties, machinability, and practical applications. Both metals are widely used in industries such as aerospace, automotive, and electronics due to their unique characteristics. The following sections explore their differences systematically, supported by technical data and practical considerations to aid in material selection for machining processes.
Physical Properties of Aluminum and Copper
Understanding the physical properties of aluminum and copper is essential for determining their suitability for machining. These properties influence tool selection, machining parameters, and final product performance.
Aluminum is a lightweight, non-ferrous metal with a density of approximately 2.70 g/cm³. It has a melting point of 660°C and a thermal conductivity of 210 W/mK. Aluminum forms a natural oxide layer when exposed to air, which enhances its corrosion resistance, making it ideal for applications in harsh environments. Its electrical conductivity is about 61% that of copper, sufficient for many electrical applications.
Copper, in contrast, is denser at 8.96 g/cm³, with a higher melting point of 1083°C and superior thermal conductivity of 231 BTU/(hr·ft·°F) or approximately 401 W/mK. Copper’s electrical conductivity is among the highest of all metals, making it the preferred choice for electrical wiring and components. It is also highly ductile and malleable, allowing it to be shaped easily, but its softness can complicate machining processes.
Property | Aluminum | Copper |
---|---|---|
Density (g/cm³) | 2.70 | 8.96 |
Melting Point (°C) | 660 | 1083 |
Thermal Conductivity (W/mK) | 210 | 401 |
Electrical Conductivity (% IACS) | 61 | 100 |
Tensile Strength (MPa) | 90-250 (varies by alloy) | 200-400 (varies by alloy) |
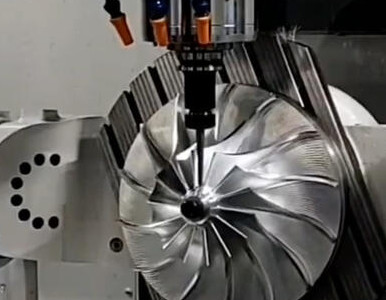
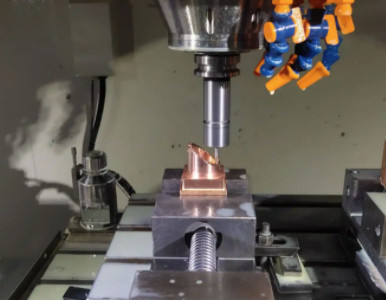
Machinability of Aluminum
Aluminum is renowned for its excellent machinability, making it a preferred material in CNC machining. Its low density and softness allow for high cutting speeds and efficient material removal. Common aluminum alloys, such as 6061 and 7075, offer a balance of strength, corrosion resistance, and ease of machining. Alloy 6061, with a tensile strength of approximately 124-290 MPa, is versatile and widely used for structural components, while 7075, with a tensile strength of up to 572 MPa, is favored for high-strength aerospace applications.
Aluminum’s lower thermal conductivity compared to copper (210 W/mK vs. 401 W/mK) results in less heat generation during machining, reducing tool wear. It produces short, manageable chips, which minimizes the risk of chip buildup and tool damage. Recommended cutting speeds for aluminum typically range from 800 to 1200 RPM, with feed rates of 0.05-0.2 mm/rev for turning and 0.1-0.3 mm/tooth for milling. Uncoated carbide or polished carbide tools with a positive rake angle are ideal for achieving smooth cuts and preventing material adhesion.
Aluminum’s natural oxide layer provides corrosion resistance, but it can cause slight abrasion on tools, necessitating the use of high-quality cutting fluids to maintain tool life. Additionally, aluminum’s low melting point requires careful control of machining parameters to avoid melting or deformation, particularly in thin-walled parts.
Machinability of Copper
Copper presents unique challenges in machining due to its high ductility and softness. Pure copper, such as C10100 (oxygen-free high-conductivity copper), has a machinability rating of approximately 20% compared to free-cutting brass (100%). Its tendency to form long, stringy chips can lead to tool clogging and poor surface finish. Copper alloys, such as brass (copper-zinc) or bronze (copper-tin), are often preferred for machining due to improved chip formation and machinability.
Copper’s high thermal conductivity (401 W/mK) causes rapid heat dissipation during machining, which can lead to tool overheating if not properly managed. Recommended cutting speeds for copper are lower, typically 300-400 RPM, with feed rates of 0.02-0.1 mm/rev for turning and 0.05-0.15 mm/tooth for milling. Sharp, high-speed steel (HSS) or carbide tools with a positive rake angle are essential to minimize material adhesion and ensure clean cuts. Lubricants, such as kerosene or water-based coolants, are critical to reducing heat and preventing the material from sticking to the tool.
Copper’s ductility can result in smearing or elongation during machining, particularly in high-precision applications. To mitigate this, machinists often use chip breakers or peck drilling techniques to control chip formation. Additionally, copper’s high density requires secure workholding to prevent vibrations and maintain dimensional accuracy.
Applications in CNC Machining
Aluminum and copper serve distinct roles in CNC machining based on their properties. Aluminum’s lightweight nature and corrosion resistance make it ideal for aerospace and automotive components, such as aircraft structural parts, engine components, and vehicle frames. Its machinability and cost-effectiveness also suit it for consumer electronics, including computer cases and heat sinks. Aluminum’s ability to be anodized enhances its aesthetic appeal and durability, making it suitable for decorative and functional parts.
Copper’s superior electrical and thermal conductivity makes it indispensable in electrical and electronic applications, such as wiring, connectors, and heat sinks. Its corrosion resistance and antibacterial properties are valuable in plumbing, medical equipment, and marine applications. Copper alloys, such as brass and bronze, are used for gears, bearings, and decorative hardware due to their improved machinability and strength.
Application | Aluminum | Copper |
---|---|---|
Aerospace | Aircraft structures, engine parts, impellers | Electrical connectors |
Automotive | Body panels, wheels | Motor coils, wiring |
Electronics | Heat sinks, enclosures | Conductors, circuit boards |
Plumbing | Pipes, fittings | Pipes, valves |
Key Considerations in Material Selection
Choosing between aluminum and copper for machining depends on the project’s requirements. Aluminum is preferred when weight reduction, cost-effectiveness, and ease of machining are priorities. Its lower density and excellent machinability make it suitable for high-volume production and complex geometries. However, its lower electrical conductivity limits its use in applications requiring maximum conductivity.
Copper is selected for projects prioritizing electrical and thermal conductivity, such as electrical components and heat exchangers. Its higher density and strength suit applications where durability is critical, but its machining challenges and higher material cost must be considered. Copper alloys, such as brass or bronze, can offer a compromise by improving machinability while retaining desirable properties.
Tool selection is a critical factor. For aluminum, uncoated carbide tools with a positive rake angle are recommended to minimize heat generation and ensure smooth cuts. For copper, sharp HSS or carbide tools with chip breakers are necessary to manage its ductility and prevent tool clogging. Coolant use is essential for both materials to reduce heat and extend tool life, but copper requires more aggressive cooling due to its higher thermal conductivity.
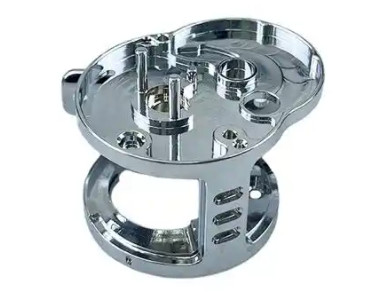
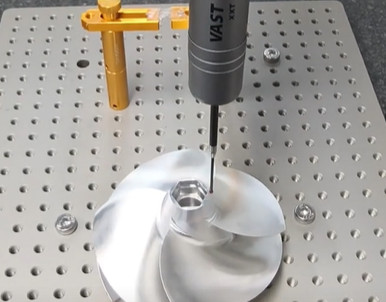
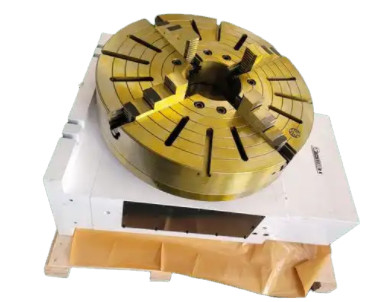
Practical Machining Techniques
To optimize machining outcomes, specific techniques are recommended for each metal. For aluminum, high spindle speeds (800-1200 RPM) and moderate feed rates (0.1-0.3 mm/tooth) are effective for achieving smooth surface finishes. Trochoidal milling can enhance material removal rates while reducing tool wear. Secure workholding is crucial to prevent distortion in thin-walled aluminum parts.
For copper, lower spindle speeds (300-400 RPM) and light depths of cut (0.02-0.1 mm/rev) help manage heat and prevent material adhesion. Peck drilling and chip breakers are essential to control chip formation and avoid tool damage. Using lubricants like kerosene or water-based coolants can improve surface finish and reduce tool wear. Machinists should also ensure rigid machine setups to counteract copper’s density and prevent vibrations.
Cost and Availability
Aluminum is generally more cost-effective than copper due to its abundance in the Earth’s crust, with prices typically ranging from $2 to $4 per pound compared to copper’s $5 to $10 per pound for common grades like C10100. Aluminum’s lower material cost and ease of machining make it a preferred choice for large-scale production. Copper’s higher cost is justified in applications requiring superior conductivity or corrosion resistance, but its alloys, such as brass, can offer cost savings with improved machinability.
Both metals are highly recyclable, contributing to sustainability. Aluminum recycling saves up to 95% of the energy required for primary production, while copper retains its properties through multiple recycling cycles, with over 80% of mined copper still in use.
Conclusion
Aluminum and copper are versatile metals with distinct machining properties and applications. Aluminum’s lightweight nature, excellent machinability, and cost-effectiveness make it ideal for aerospace, automotive, and consumer electronics. Copper’s superior electrical and thermal conductivity suit it for electrical and thermal management applications, though its machining requires careful parameter control. By understanding their properties, machinability, and practical applications, manufacturers can make informed decisions to optimize performance and cost in CNC machining projects.