Superhard material complex parts, critical in aerospace applications, present unique machining challenges due to their intricate geometries, high hardness (40–45 HRC), and stringent dimensional and geometric tolerances. These parts, typically quenched forgings, are prone to deformation, severe tool wear, and difficulties in achieving precise feature geometries. This document details a systematic process improvement strategy that employs a tension-based positioning fixture, axial micro-progressive milling, and stress-release techniques to ensure stable and reliable machining quality. The approach addresses clamping difficulties, tool wear, and precision issues without relying on trend-based or speculative solutions, focusing instead on practical, technically robust methods.
Part Structure Analysis
The parts are irregular forgings with complex structures, including ribs, grooves, holes, steps, arcs, and angular features. Post-quenching, the material hardness reaches 40–45 HRC, classifying it as difficult-to-machine. Key specifications include a groove bottom to datum hole distance of 103 mm, a total part length of 127 mm, and a minimum rib thickness of 10 mm. Spatial features are referenced to datum holes and axes, with strict dimensional tolerances (≤0.02 mm) and geometric tolerances (e.g., symmetry ≤0.05 mm). Heat treatment introduces significant deformation, complicating the maintenance of precision between holes, grooves, and surfaces.
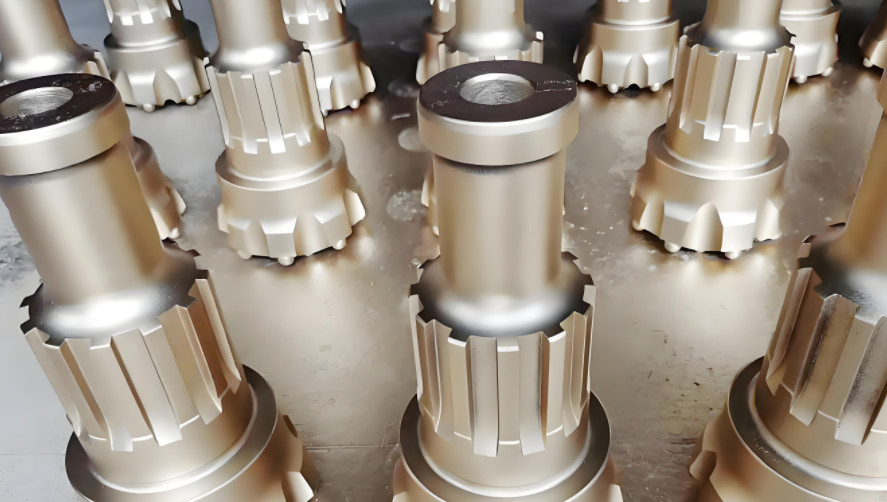
Processing Difficulties
The machining process encounters several technical challenges:
- Clamping-Induced Deformation: Traditional flat-jaw vise clamping applies force to flat surfaces, causing micro-deformations. Upon clamp release, elastic recovery disrupts dimensional and geometric accuracy, with deviations exceeding tolerances.
- Material Hardness and Tool Wear: The high hardness leads to poor machinability, causing tool sticking and cutting edge buildup. This results in dimensional drifts (≥0.02 mm) and symmetry errors (≥0.15 mm), compromising surface roughness and geometric precision.
- Radial Cutting Forces: Radial milling with cylindrical cutters generates forces that induce part bending, vibration, and minor taper deformations. Tool helix angle effects exacerbate elastic deformation, causing dimensional drift.
- Residual Stress Release: High material removal rates and uneven stock removal disrupt internal stress balance, leading to deformation. Removing clamping allowances in the final step causes sudden stress release, affecting tolerances.
Process Improvement Solutions
A systematic approach was developed to address these challenges, focusing on fixturing, milling strategies, and stress management. The solutions prioritize precision, reliability, and repeatability in a five-axis CNC machining environment.
Tension-Based Positioning Fixture
A custom tension-based positioning fixture was designed to replace traditional vise clamping, enabling single-setup, multi-feature machining on a five-axis CNC machine. This fixture ensures precise alignment and minimizes deformation.
- Fixture Design: The fixture adheres to the one-face-two-pin positioning principle. It features a datum surface with threaded process holes at the top. Corresponding internal threaded holes are machined into the part’s clamping base, secured with screws for tension-based positioning.
- Interference Management: Clearance grooves beneath the threaded holes accommodate screw-tightening forces. Angled fixture surfaces prevent collisions between the tool, part, and fixture during five-axis operations, considering machine stroke and swing angles.
- Performance: This design reduces clamping-induced elastic deformation, ensures stable positioning, and supports multi-angle machining, maintaining symmetry tolerances within ≤0.05 mm.
Pre-Machining Stress Relief Grooves
To mitigate deformation from stress release during final stock removal, grooves are machined into the clamping allowance area before quenching. This approach balances internal stresses and prevents precision loss.
- Groove Configuration: Grooves are cut into the part’s base to release residual stresses while retaining sufficient material for tension-based clamping. Rounded corners at the groove base prevent stress concentration and potential part fracture.
- Process Timing: Grooves are machined prior to heat treatment, ensuring stress balance is maintained during subsequent steps, reducing deformation risks in finishing operations.
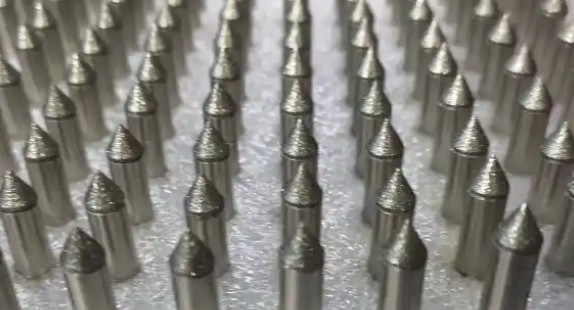
Axial Micro-Progressive Milling
For planar feature machining, a small-diameter, short-flute milling cutter is used with axial micro-progressive milling to minimize radial cutting forces and control stress release.
- Tool Selection: A 6 mm diameter cutter with short flutes ensures high rigidity, reducing radial forces and deflection. This improves dimensional stability and tool life.
- Milling Technique: Axial micro-progressive milling involves incremental depth cuts (0.05–0.1 mm), allowing gradual stress release. This method minimizes radial pulling forces from side-blade cutting, maintaining dimensional and geometric tolerances.
Optimized milling parameters are detailed below:
Parameter | Value |
---|---|
Cutter Diameter (mm) | 6 |
Spindle Speed (rpm) | 8000–10000 |
Feed Rate (mm/min) | 200–300 |
Axial Depth of Cut (mm) | 0.05–0.1 |
Coolant | High-pressure emulsion |
Uniform Stock Removal Strategy
To control deformation from uneven stress release, the machining process follows a uniform stock removal principle, except for the clamping allowance area.
- Roughing and Semi-Finishing: Traditional vise clamping is used with multiple part reorientations to remove stock efficiently. Roughing leaves a 3 mm allowance, while semi-finishing reduces it to 0.3 mm.
- Finishing: The tension-based fixture enables five-axis machining of all features in a single setup. Stock removal is incrementally reduced, ensuring uniform stress distribution and maintaining tolerances.
Implementation and Workflow
The machining process is structured to optimize precision and efficiency. The workflow is as follows:
- Pre-Processing: Machine stress relief grooves in the clamping allowance area before quenching to balance internal stresses.
- Roughing: Use traditional vise clamping on a five-axis machine, removing stock to a 3 mm allowance through multiple setups.
- Semi-Finishing: Reduce stock to a 0.3 mm allowance, maintaining uniform removal to minimize stress-induced deformation.
- Finishing: Employ the tension-based fixture for single-setup machining. Use axial micro-progressive milling to finish planar features, ensuring dimensional accuracy (≤0.02 mm) and symmetry (≤0.05 mm).
- Final Stock Removal: Remove clamping allowance with controlled cuts to avoid sudden stress release, preserving precision.
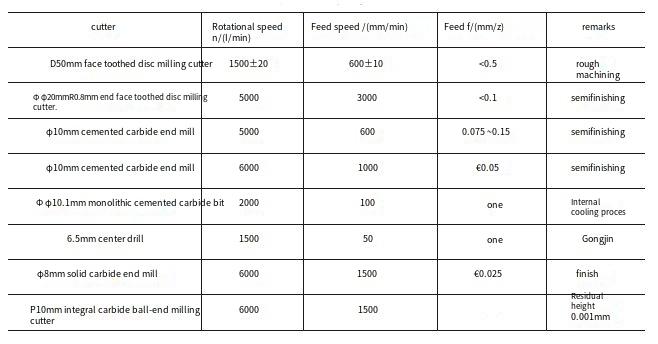
The workflow, illustrated as above, ensures all features are machined within tolerances while minimizing deformation and tool wear.
Stage | Clamping Method | Stock Allowance (mm) | Key Objective |
---|---|---|---|
Roughing | Vise | 3 | Efficient stock removal |
Semi-Finishing | Vise | 0.3 | Uniform stock reduction |
Finishing | Tension Fixture | 0 | Precision and tolerance control |
Conclusion
The proposed process improvements for CNC machining of superhard material complex parts address critical challenges through targeted solutions. The tension-based positioning fixture eliminates clamping-induced deformation, axial micro-progressive milling reduces tool wear and radial forces, and pre-machining stress relief grooves manage residual stresses. The uniform stock removal strategy ensures consistent precision across all machining stages. These methods collectively enhance machining quality, achieving dimensional accuracy (≤0.02 mm) and geometric tolerances (e.g., symmetry ≤0.05 mm), providing a reliable framework for similar high-precision applications.