Explore the art and science of CNC milling for producing high-precision parts. This guide covers tool selection, programming techniques, and process control strategies to achieve superior accuracy and efficiency.
Introduction to CNC Milling for Precision Parts
CNC milling is a versatile machining process used to create complex, high-precision parts with exceptional accuracy. From intricate geometries to tight tolerances, CNC milling is ideal for producing components like housings, connectors, and structural parts, including those with precision holes. This makes it indispensable in industries such as aerospace, medical, automotive, and electronics, where precision is critical.
Achieving high-precision parts requires careful consideration of three key areas: tool selection, programming techniques, and process control. By optimizing these elements, manufacturers can produce parts that meet stringent specifications while minimizing waste and production time.
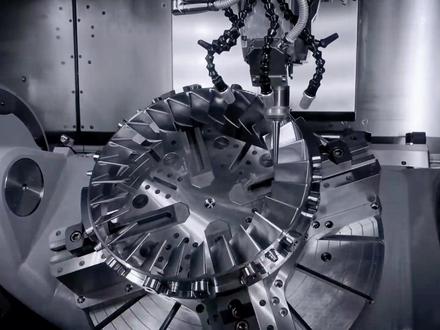
Why Precision Matters in Parts Manufacturing
Precision is essential for components like turbine blades, medical implants, and electronic connectors. Tolerances as tight as ±0.0002 inches (±5 microns) ensure functionality, reliability, and safety. Deviations can lead to assembly issues, performance failures, or safety risks, making precision a non-negotiable aspect of CNC milling.
Overview of CNC Milling Machines
CNC milling machines range from 3-axis to 5-axis systems, with higher-axis machines offering flexibility for complex part geometries. Key components include:
- Spindle: Rotates the cutting tool at speeds up to 20,000 RPM.
- Tool Changer: Automatically switches tools for multi-operation tasks.
- Worktable: Secures the workpiece with precision fixtures.
- CNC Controller: Executes programmed instructions for tool paths.
Tool Selection for Precision CNC Milling
The choice of cutting tools is critical for successful CNC milling of high-precision parts. The right tool ensures accuracy, extends tool life, and enhances surface quality across various part types, including those with holes, slots, or contours.
Types of Tools for Parts Machining
Several tool types are used for milling precision parts:
- End Mills: Ideal for slotting, profiling, and creating features like pockets or holes with flat bottoms. Available in 2-4 flutes for different materials.
- Drills: Designed for creating precise holes, with diameters from 0.01 to 2 inches.
- Reamers: Used for finishing holes to achieve tight tolerances and smooth surfaces.
- Face Mills: Create flat surfaces on large parts, ensuring perpendicularity.
Tool Material and Coatings
Tool material and coatings impact performance:
- Carbide: Offers high hardness for metals like stainless steel and titanium.
- High-Speed Steel (HSS): Cost-effective for softer materials like aluminum.
- Diamond-Coated Tools: Ideal for composites, extending tool life by up to 10x.
- TiAlN Coating: Enhances heat resistance for high-speed machining of alloys.
For example, a carbide end mill with a TiAlN coating can achieve a surface finish of Ra 0.4 µm when machining titanium at 6,000 RPM.
Tool Geometry and Parameters
Tool geometry affects chip evacuation and cutting efficiency. Key parameters include:
- Flute Count: 2 flutes for soft materials, 4 flutes for harder metals.
- Helix Angle: 30-40° for general-purpose milling, 45° for high-speed aluminum machining.
- Corner Radius: 0.005-0.02 inches for end mills to reduce stress and improve tool life.
Typical cutting parameters for a 0.5-inch carbide end mill in stainless steel include a spindle speed of 4,000 RPM, feed rate of 0.003 inches per revolution, and depth of cut of 0.05 inches per pass.
CNC Programming for High-Precision Parts
Effective CNC programming is essential for achieving precision in parts machining. It involves creating tool paths, optimizing feed rates, and minimizing cycle times while ensuring dimensional accuracy for features like holes, contours, and surfaces.
G-Code and CAM Software
CNC milling machines are controlled using G-code, a programming language that dictates tool movements. Computer-Aided Manufacturing (CAM) software like Fusion 360, Mastercam, or Siemens NX generates G-code automatically, offering:
- Tool Path Simulation: Visualizes machining to prevent collisions.
- Adaptive Clearing: Optimizes tool paths for efficient material removal.
- Multi-Axis Support: Enables complex part geometries on 4- or 5-axis machines.
Programming Techniques for Precision
Several programming techniques enhance precision in parts machining:
- Contour Milling: Creates smooth, accurate surfaces using continuous tool paths.
- Helical Interpolation: Mills circular features like holes using a spiral tool path.
- Trochoidal Milling: Reduces tool load for high-speed machining of tough materials.
For example, a contour milling program for a complex aerospace part might use a 0.375-inch end mill at 7,000 RPM, with a 0.01-inch radial engagement and 0.05-inch axial depth per pass.
Optimizing Feed and Speed
Feed and speed settings balance precision and efficiency. Typical parameters include:
- Spindle Speed: 5,000-15,000 RPM for metals, 2,000-8,000 RPM for plastics.
- Feed Rate: 0.001-0.005 inches per revolution for precision cuts.
- Cutting Depth: 0.01-0.1 inches per pass, depending on material and tool.
CAM software calculates optimal settings, reducing trial-and-error.
Process Control in CNC Milling
Process control ensures consistency and accuracy during CNC milling, minimizing defects and maintaining tight tolerances for all part features.
Workholding and Fixturing
Secure workholding prevents vibration and ensures repeatability. Common methods include:
- Vises: For rectangular workpieces, offering clamping forces up to 5,000 lbs.
- Vacuum Chucks: For thin or flat parts, providing uniform holding pressure.
- Custom Fixtures: Designed for complex geometries, ensuring precise alignment.
Fixtures maintain positional accuracy within ±0.0005 inches.
In-Process Monitoring
Real-time monitoring detects issues like tool wear or thermal expansion. Technologies include:
- Tool Condition Monitoring: Sensors measure vibration and cutting forces.
- Probing Systems: In-machine probes measure dimensions with ±0.0001-inch accuracy.
- Thermal Compensation: Adjusts for spindle or material expansion.
For example, a Renishaw probe verifies feature dimensions to within ±0.0002 inches in seconds.
Quality Assurance
Post-machining checks ensure parts meet specifications. Common tools include:
- Coordinate Measuring Machines (CMM): Measure dimensions with ±0.0001-inch accuracy.
- Calipers and Micrometers: Verify external and internal features to ±0.0002 inches.
- Surface Profilometers: Assess surface finish, targeting Ra 0.2-0.8 µm.
Statistical Process Control (SPC) tracks variations, ensuring production stability.
Applications of Precision CNC Milling for Parts
Precision CNC milling serves critical applications across industries, producing parts with complex features and tight tolerances.
Aerospace Industry
Aerospace components like turbine blades and structural brackets require tolerances of ±0.0002 inches. CNC milling produces:
- Cooling Holes: Small, angled holes for thermal management.
- Mounting Features: For high-strength fasteners in titanium alloys.
Medical Industry
Medical devices like implants and surgical tools rely on precision parts:
- Implant Components: With Ra 0.4 µm finishes for biocompatibility.
- Instrument Features: Precision contours for minimally invasive tools.
Electronics Industry
Electronics require miniature parts for connectors and circuit boards:
- Connector Housings: With tolerances of ±0.0003 inches.
- Micro Features: For PCB vias and mounting points, often <0.01 inches.
Optimizing CNC Milling for Maximum Precision
To achieve the highest precision in parts machining, manufacturers must integrate best practices across tool selection, programming, and process control.
Tool Optimization
Select tools based on material and part specifications. For example, a 0.5-inch carbide end mill with a 0.01-inch corner radius is ideal for stainless steel, operating at 4,000 RPM and 0.003 inches/rev feed rate. Regular tool inspection prevents defects.
Programming Best Practices
Use CAM software to simulate tool paths and optimize parameters. For complex parts, adaptive clearing reduces tool load, improving surface finish. Helical interpolation for holes minimizes stress, ensuring accuracy.
Process Control Strategies
Implement in-process probing to verify dimensions mid-cycle, reducing scrap. Thermal compensation adjusts for temperature-induced errors, ensuring ±0.0002-inch accuracy. SPC targets CpK > 1.33 for critical features.
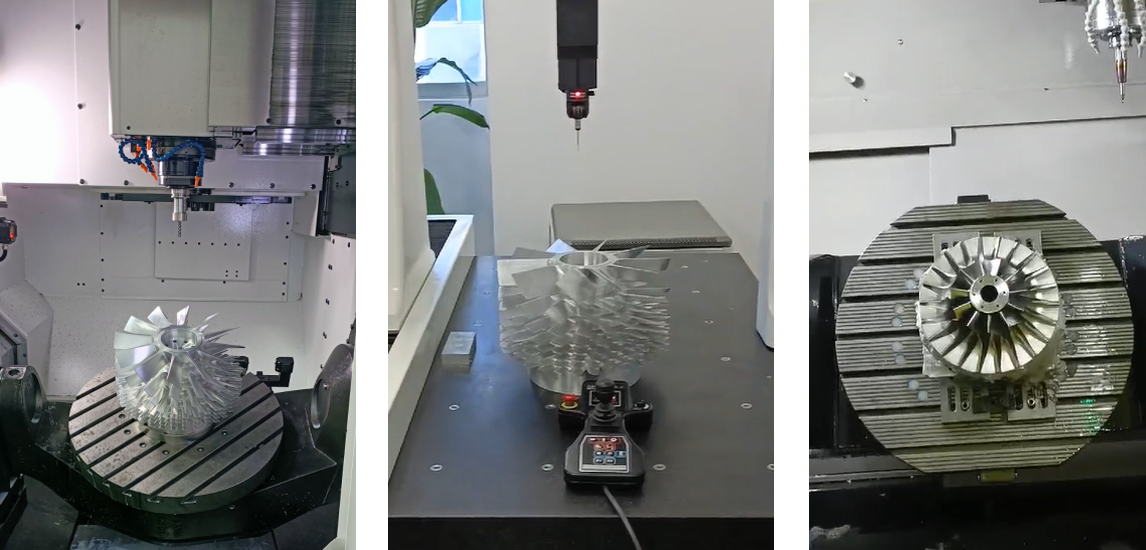
How KeSu can Help?
CNC milling for precision parts combines advanced tools, sophisticated programming, and robust process control to deliver unparalleled accuracy. By mastering these elements, manufacturers can meet the demands of high-stakes industries.
Designed a product that requires milling machining? Or maybe custom parts with tight tolerances? Reach out to KeSu for precision CNC milling services.
With 3-axis, 4-axis, and 5-axis milling capabilities, we handle even the most complex or intricate designs. Whether you need rapid prototypes or a large production run, we ensure accuracy in your products (metals, plastics, or alloys). Get an instant quote today. Just upload your design and let our experts turn your vision into reality!
Emerging Innovations in CNC Milling for Precision Parts
Advancements in technology are driving new innovations in CNC milling, enhancing precision and efficiency for high-precision parts.
Smart Manufacturing
Industry 4.0 technologies like IoT sensors and AI-driven analytics monitor tool wear and optimize parameters in real time, improving consistency.
Advanced Tooling
Polycrystalline diamond (PCD) end mills and ceramic tools offer superior hardness, enabling faster machining of composites and superalloys.
Automation
Robotic tool changers and automated workholding systems enable lights-out manufacturing for high-volume parts with minimal human intervention.
Frequently Asked Questions
What tools are best for CNC milling precision parts?
Carbide end mills, drills, and reamers with TiAlN or diamond coatings are ideal, offering durability and smooth finishes for materials like stainless steel and titanium.
How does CNC programming affect part precision?
Techniques like contour milling, helical interpolation, and optimized feed/speed settings ensure accurate tool paths, minimizing deflection and achieving ±0.0002-inch tolerances.
What is the role of process control in CNC milling?
Process control involves secure workholding, in-process monitoring (e.g., probes, sensors), and quality assurance (e.g., CMM) to maintain dimensional accuracy and surface quality.
Which industries rely on precision parts machining?
Aerospace, medical, and electronics industries use CNC milling for parts like turbine blades, implants, and connectors, requiring tight tolerances and reliability.
Can CNC milling produce micro features?
Yes, CNC milling can produce micro features as small as 0.01 inches using specialized tools and high-precision 5-axis machines, ideal for electronics and medical applications.