Multi-variety, small-batch production is common in industries like aerospace, medical devices, and automotive, where customization and precision are critical. CNC service providers face unique demands in this environment, requiring efficient processes to handle diverse parts in limited quantities while maintaining high quality and cost-effectiveness. This guide provides a detailed, technical approach to optimizing CNC operations for multi-variety, small-batch production, focusing on practical strategies that enhance productivity, reduce setup times, and ensure precision.
Streamline CNC Programming for Flexibility
Efficient CNC programming is essential for managing diverse part designs in small-batch production. Programs must be adaptable to handle varying geometries, materials, and tolerances without extensive reprogramming.
- Use Parametric Programming: Parametric programming allows operators to create flexible CNC programs that can be adjusted for different part specifications by changing variables like dimensions or tool paths. This reduces the need to write new programs for each part variant.
- Leverage CAD/CAM Software: Advanced CAD/CAM systems, such as Fusion 360 or Mastercam, enable rapid generation of tool paths for complex geometries. These systems integrate design and manufacturing, allowing seamless updates when part designs change.
- Standardize Program Templates: Develop reusable program templates for common operations like drilling, milling, or turning. Templates reduce programming time by providing a consistent framework that can be modified for specific parts.
- Simulate Programs: Run simulations using CAM software to identify potential issues like tool collisions or inefficient paths before machining begins. This minimizes errors and ensures programs are optimized for each batch.
By implementing these strategies, CNC service providers can reduce programming time by up to 30% and improve adaptability to diverse part requirements.
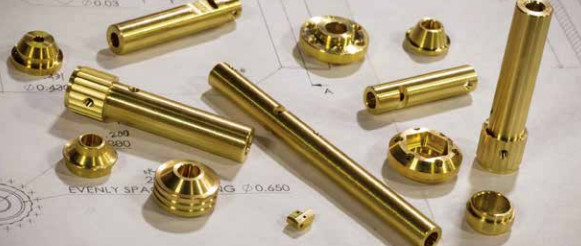
Optimize Tooling Strategies for Quick Changeovers
Tool changes are a significant bottleneck in small-batch production due to frequent setup adjustments. Optimizing tooling strategies minimizes downtime and maintains precision across varied production runs.
- Invest in Multi-Tool Holders: Automatic tool changers (ATCs) or multi-tool spindles allow seamless switching between tools without stopping the machine. For example, a 24-tool ATC can reduce tool change time to under 5 seconds per swap.
- Standardize Tool Presets: Pre-set tools off-machine using tool presetters to ensure consistent tool lengths and diameters. This reduces setup time by up to 50% compared to manual adjustments.
- Select Versatile Tools: Use tools with broad applicability, such as carbide end mills with variable helix angles, to handle multiple materials (e.g., aluminum, stainless steel) without frequent changes.
- Implement Tool Management Systems: Use software to track tool life, wear, and inventory. Systems like TDM (Tool Data Management) provide real-time data, ensuring tools are replaced before they cause defects.
Tooling Strategy | Benefit | Implementation Example |
---|---|---|
Multi-Tool Holders | Reduces tool change time to <5 seconds | 24-tool ATC on a 5-axis CNC mill |
Tool Presetting | Cuts setup time by up to 50% | Zoller presetter for offline tool measurement |
Versatile Tools | Minimizes tool swaps across materials | Carbide end mill with TiAlN coating |
These tooling strategies enable CNC service providers to achieve faster changeovers, reducing downtime by 20-40% in small-batch environments.
Enhance Setup Efficiency with Standardized Fixtures
Fixtures play a critical role in securing workpieces during machining. In multi-variety production, standardized and modular fixturing systems reduce setup times and ensure repeatability.
- Use Modular Fixtures: Modular fixturing systems, such as those from Jergens or Schunk, allow quick reconfiguration for different part sizes and shapes. These systems use interchangeable components to adapt to various workpieces.
- Implement Zero-Point Clamping: Zero-point clamping systems provide precise, repeatable positioning, reducing setup time by up to 70%. For example, a Lang Technik zero-point system can align parts within 0.005 mm.
- Design Custom Fixture Plates: Create fixture plates with pre-drilled patterns for common part families. This allows operators to quickly mount parts without designing new fixtures for each batch.
- Document Setup Procedures: Maintain detailed setup sheets with photos and measurements to ensure consistency across operators and shifts. Digital setup guides stored in a centralized system improve accessibility.
Standardized fixturing reduces setup times from hours to minutes, improving throughput for small-batch production.
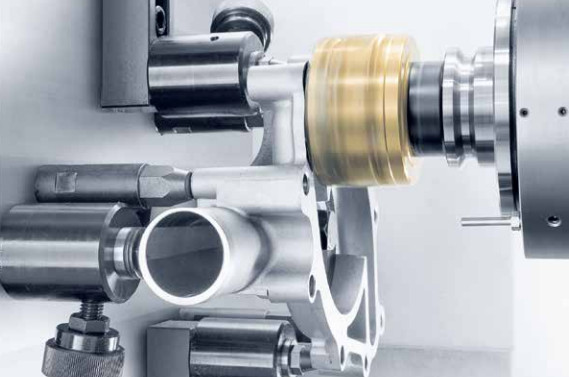
Optimize Machining Parameters for Efficiency
Selecting appropriate machining parameters, such as spindle speed, feed rate, and depth of cut, is critical for balancing efficiency, tool life, and part quality in small-batch production.
- Adjust Spindle Speed and Feed Rate: Optimize parameters based on material properties. For example, aluminum 6061 typically requires a spindle speed of 8,000-12,000 RPM and a feed rate of 100-200 mm/min for milling.
- Use High-Efficiency Milling (HEM): HEM strategies, such as trochoidal milling, reduce tool wear and improve material removal rates by up to 50% compared to conventional milling.
- Control Depth of Cut: Limit depth of cut to 1-2 times the tool diameter for roughing operations to minimize deflection and maintain precision.
- Monitor Cutting Forces: Use sensors to measure cutting forces in real-time, adjusting parameters to prevent tool overload or workpiece damage.
Material | Spindle Speed (RPM) | Feed Rate (mm/min) | Depth of Cut (mm) |
---|---|---|---|
Aluminum 6061 | 8,000-12,000 | 100-200 | 1-3 |
Stainless Steel 304 | 2,000-4,000 | 50-100 | 0.5-1.5 |
Titanium Ti-6Al-4V | 1,000-2,000 | 30-60 | 0.3-1.0 |
Optimized parameters improve machining efficiency while maintaining part quality across diverse materials.
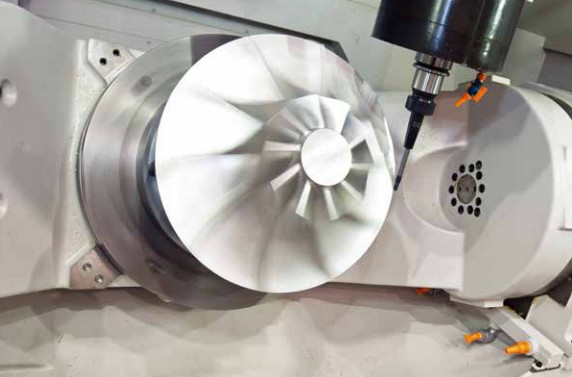
Implement Data-Driven Process Control
Data management and real-time monitoring enhance process control, enabling CNC service providers to identify inefficiencies and maintain consistency in small-batch production.
- Use Manufacturing Execution Systems (MES): MES software, like MachineMetrics, provides real-time visibility into machine status, cycle times, and production bottlenecks, enabling data-driven decisions.
- Track Key Performance Indicators (KPIs): Monitor metrics such as Overall Equipment Effectiveness (OEE), cycle time, and scrap rate to assess performance and identify areas for improvement.
- Centralize Data Storage: Store CNC programs, setup sheets, and tool data in a centralized database to ensure consistency and reduce errors during batch transitions.
- Analyze Production Data: Use analytics to identify trends, such as recurring setup delays or tool wear patterns, and implement corrective actions to optimize workflows.
Data-driven process control can improve OEE by 15-25%, ensuring efficient production across multiple part types.
Train Operators for Versatility and Precision
Skilled operators are critical for managing the complexities of multi-variety, small-batch production. Comprehensive training ensures consistency and adaptability.
- Cross-Train Operators: Train operators on multiple CNC machines (e.g., mills, lathes, routers) to handle diverse tasks and reduce reliance on specialized personnel.
- Focus on Setup Efficiency: Provide training on standardized setup procedures and fixturing systems to minimize errors and reduce setup times.
- Teach Data Interpretation: Equip operators to interpret real-time data from MES or machine sensors, enabling quick adjustments to maintain quality.
- Update Skills Regularly: Conduct ongoing training to keep operators updated on new software, tools, and machining techniques.
Well-trained operators can reduce setup errors by 20% and improve overall production efficiency.
Integrate Automation for Scalability
Automation reduces manual intervention, enabling CNC service providers to handle small-batch production with greater consistency and scalability.
- Use Robotic Loading Systems: Robotic arms can load and unload workpieces, reducing setup time and enabling lights-out operation for small batches.
- Implement Pallet Changers: Automatic pallet changers allow continuous machining by swapping workpieces without stopping the machine, reducing downtime by up to 30%.
- Integrate Bar Feeders: For lathe operations, bar feeders automate material loading, enabling longer unattended runs for small-batch parts.
- Adopt In-Process Inspection: Use probes or laser systems to perform in-process quality checks, reducing manual inspection time and ensuring part accuracy.
Automation increases throughput and allows CNC service providers to scale production without proportional increases in labor costs.
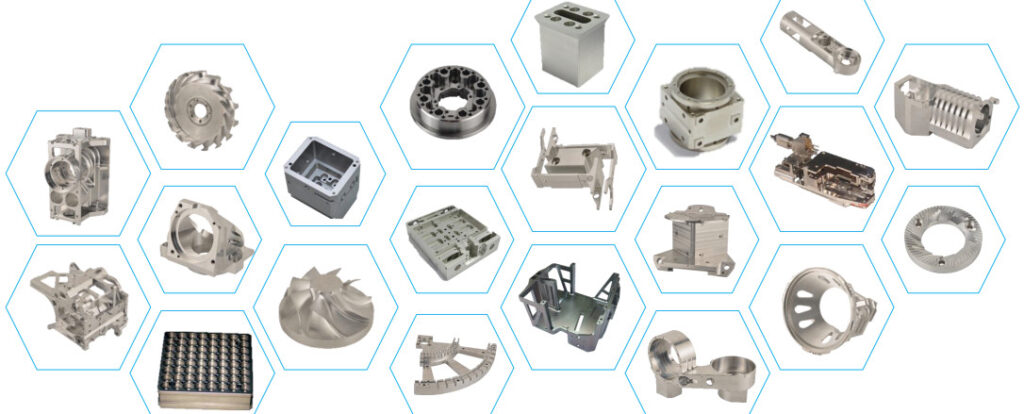
Maintain Equipment for Consistent Performance
Regular maintenance ensures CNC machines perform reliably, minimizing downtime and maintaining precision in small-batch production.
- Schedule Preventive Maintenance: Perform regular checks on spindles, coolant systems, and linear guides to prevent unexpected failures. For example, lubricate linear guides every 500 hours of operation.
- Calibrate Machines Regularly: Calibrate machines every 6-12 months to maintain accuracy within 0.01 mm, critical for precision parts.
- Monitor Coolant Levels: Ensure proper coolant concentration (e.g., 5-10% for water-based coolants) to prevent tool overheating and workpiece distortion.
- Replace Worn Components: Inspect and replace wear items like belts and bearings to maintain machine reliability.
Proactive maintenance reduces unplanned downtime by up to 40% and ensures consistent part quality.
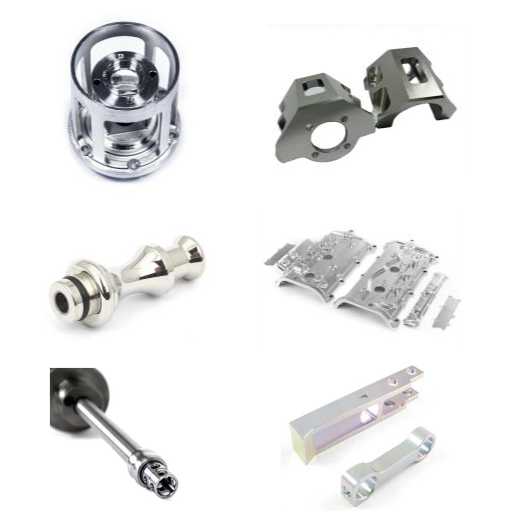
Kesu: Master Multi-Variety, Small-Batch CNC Production with Unmatched Precision & Efficiency
Kesu's tailored solutions streamline programming with parametric flexibility, slash changeover times via advanced tooling and zero-point fixturing, and optimize every parameter to balance speed, quality, and cost. Backed by data-driven insights, skilled operator training, and scalable automation, Kesu ensures you handle diverse parts in small batches with ease—reducing downtime by up to 40%, boosting OEE by 25%, and delivering precision that sets industry standards. Elevate your production agility: Choose Kesu, where complexity meets seamless efficiency.
Conclusion
Optimizing CNC operations for multi-variety, small-batch production requires a systematic approach that integrates efficient programming, tooling, fixturing, parameter optimization, data-driven control, operator training, automation, and maintenance. By implementing these strategies, CNC service providers can achieve faster setups, higher precision, and improved cost-effectiveness, meeting the demands of diverse industries while maintaining competitive edge.