This guide provides a comprehensive overview of lead screws, also known as power screws or translation screws, focusing on their types, applications, material selection, and machining processes. Designed for engineers, machinists, and manufacturers, it emphasizes technical accuracy, material compatibility, and machining parameters for prototyping and production. The content is structured systematically to ensure clarity and practical utility, with detailed insights into precision engineering.
Types of Lead Screws and Their Characteristics
Lead screws are mechanical components that convert rotary motion into linear motion, widely used in precision positioning systems. Their design, including thread profiles and material composition, varies to meet specific functional requirements. Below is a detailed exploration of lead screw types and their properties.
Acme Lead Screws: Acme screws feature a trapezoidal thread profile with a 29-degree thread angle, offering a balance of strength and efficiency. They are commonly used in CNC machines, actuators, and industrial presses, with diameters ranging from 6 mm to 50 mm. Acme screws are typically made from steel or bronze, providing durability and moderate friction resistance.
Square Thread Lead Screws: Square thread screws have a 0-degree flank angle, maximizing efficiency in motion transfer due to minimal radial forces. They are ideal for high-load applications like jacks and heavy machinery but are more complex to manufacture. Materials include hardened steel or stainless steel for high strength.
Ball Screws: Though technically distinct, ball screws are often grouped with lead screws due to their similar function. They use ball bearings in a helical raceway to reduce friction, offering high efficiency (up to 90%) and precision. Ball screws are used in high-speed CNC systems and robotics, with materials like chrome-plated steel or stainless steel.
Miniature Lead Screws: These screws, with diameters as small as 2 mm, are designed for micro-positioning in medical devices and electronics. They typically feature fine Acme or metric threads and are made from stainless steel or polymers for low-friction applications.
Lead Screw Type | Thread Profile | Typical Materials | Primary Applications |
---|---|---|---|
Acme Screw | Trapezoidal, 29° | Steel, bronze | CNC machines, actuators, presses |
Square Thread Screw | Square, 0° | Hardened steel, stainless steel | Jacks, heavy machinery |
Ball Screw | Ball raceway | Chrome-plated steel, stainless steel | High-speed CNC, robotics |
Miniature Screw | Fine Acme/metric | Stainless steel, polymers | Medical devices, electronics |
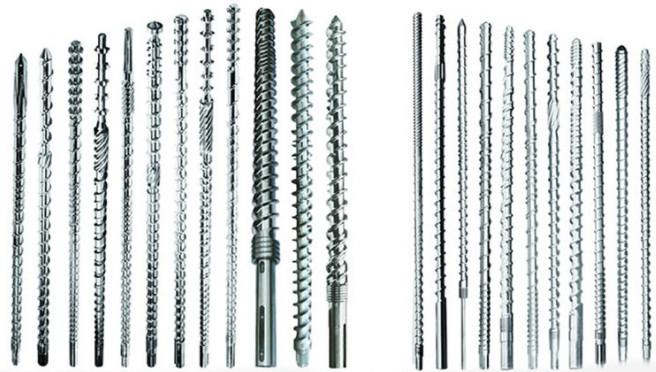
Applications of Lead Screws
Lead screws, or power screws, are integral to industries requiring precise linear motion, such as manufacturing, robotics, and aerospace. Their applications depend on load capacity, precision requirements, and environmental conditions.
Precision Positioning: Acme and ball screws are used in CNC machining centers and 3D printers to achieve accurate positioning, with resolutions as fine as 0.001 mm for ball screws. They ensure repeatability in tasks like milling, drilling, or additive manufacturing.
Actuation Systems: Lead screws drive linear actuators in industrial automation, adjusting components in assembly lines or robotic arms. Acme screws are preferred for moderate-speed applications, while ball screws handle high-speed, high-cycle tasks.
Heavy-Duty Applications: Square thread screws are used in mechanical jacks and heavy presses, supporting loads up to 100 kN or more. Their robust design ensures stability under high axial forces, making them suitable for construction equipment.
Micro-Positioning: Miniature lead screws are critical in medical devices, such as syringe pumps or imaging equipment, where compact size and precise motion (e.g., 0.01 mm/step) are requiredcarbon steel, bronze, or stainless steel, with tensile strengths ranging from 600 MPa (carbon steel) to 1,100 MPa (hardened steel). For prototyping, softer materials like brass or aluminum are often used to reduce machining difficulty, though they offer lower strength (200–300 MPa).
Plastic and Composites: Polymers like PTFE or PEEK are used in miniature lead screws for low-friction or corrosive environments, such as medical or chemical applications. Their tensile strength (50–100 MPa) limits them to low-load applications, and they have temperature constraints (up to 150°C for PEEK).
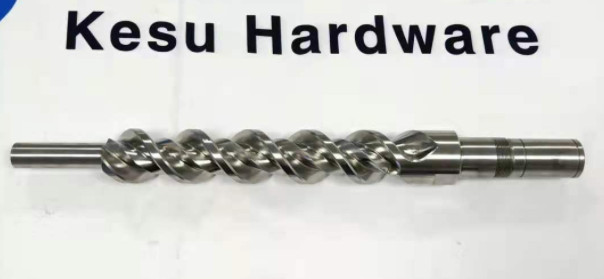
Thread Design and Specifications
Thread design is critical for lead screw performance, affecting efficiency, load capacity, and precision. Key parameters include pitch, diameter, and thread profile, tailored to specific motion control needsexploring machining methods like thread cutting, thread milling, Swiss machining, and thread rolling, with specific parameters and applications for lead screw production.
Thread Cutting: Thread cutting involves removing material to form threads, typically using taps for internal threads or dies for external threads. For an M10×1.5 Acme thread, a core hole of approximately 8.5 mm is required for 70% thread engagement. Cutting speeds range from 10–30 m/min for steel and 15–50 m/min for aluminum, with feed rates of 0.05–0.15 mm/rev.
Thread Milling: Thread milling uses a rotating tool to create threads in a single pass, ideal for large or non-standard threads. It offers superior surface finish and accuracy, with cutting speeds of 50–150 m/min and feed rates of 0.02–0.1 mm/rev. This method is common for prototyping custom lead screws due to its flexibility.
Swiss Screw Machining: Swiss machining is used for high-precision miniature lead screws, achieving tolerances of ±0.0001 inches (0.0025 mm). A sliding headstock and guide bushing minimize deflection, with spindle speeds of 1,000–12,000 RPM based on material and diameter.
Thread Rolling: Thread rolling is a cold-forming process that displaces material to form threads, enhancing strength through work hardening. It is ideal for high-volume production of lead screws, operating at pressures of 50–100 MPa and feed rates of 0.02–0.08 mm/rev. This method is less common in prototyping due to high die costs but offers superior fatigue resistance.
Process | Tool Type | Cutting Speed (m/min) | Feed Rate (mm/rev) | Material |
---|---|---|---|---|
Thread Cutting | HSS/carbide tap/die | 10–30 (steel), 15–50 (aluminum) | 0.05–0.15 | Steel, aluminum, bronze |
Thread Milling | Carbide/indexable mill | 50–150 | 0.02–0.1 | Steel, stainless steel, titanium |
Swiss Machining | Carbide tools | 80–200 | 0.01–0.05 | Stainless steel, aluminum, bronze |
Thread Rolling | Roll dies | N/A (cold forming) | 0.02–0.08 | Steel, stainless steel |
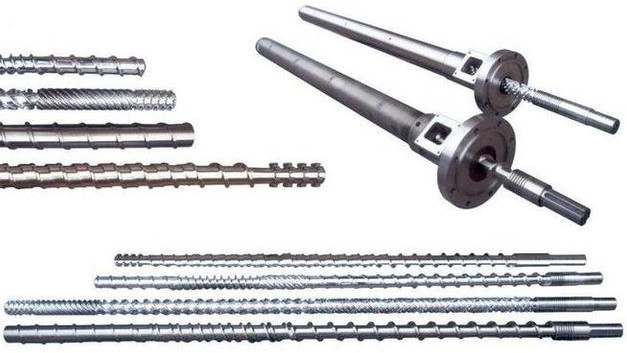
Difficulties in Lead Screw Machining
Machining lead screws involves complexities that impact quality, particularly in achieving precision and managing material properties.
Precision Complexity: Achieving tight tolerances (±0.001 inches or 0.025 mm) for miniature lead screws or high-precision ball screws requires advanced equipment like Swiss CNC machines. Small deviations in thread pitch or diameter can cause backlash or reduced accuracy, critical in applications like CNC systems.
Machining Difficulty: Hard materials like titanium or hardened steel (Rockwell C 30–40) increase tool wear and heat generation. Cutting speeds of 10–30 m/min and high-pressure coolant are necessary to prevent work hardening or thermal distortion, extending machining time and costs.
Thread Quality Issues: Thread stripping, caused by improper tap sizing or excessive force, reduces load capacity. For example, a 10 mm Acme thread requires an 8.5 mm core hole for optimal engagement. Galling, common in stainless steel, can be mitigated with lubricants or coatings like nickel.
Prototyping Constraints: Prototyping custom lead screws increases costs due to setup time and specialized tooling. Thread rolling, while efficient for production, is less cost-effective for small batches, making thread milling or cutting preferred for prototypes.
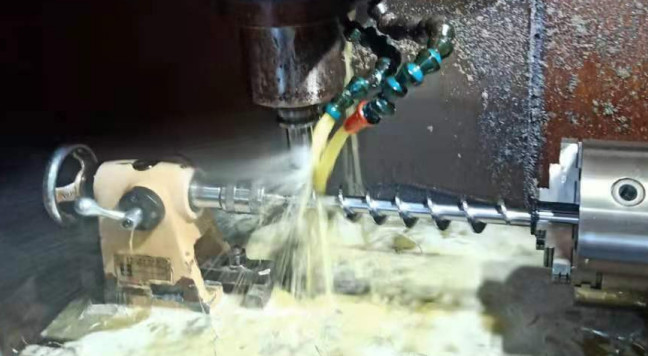
Best Practices for Lead Screw Machining
Producing high-quality lead screws requires adherence to best practices in machining, tool selection, and quality control to ensure precision and durability.
Tool Selection: Carbide tools are preferred for their durability and edge retention, especially for hard materials like titanium. High-speed steel (HSS) tools are suitable for softer materials like bronze but require frequent replacement to maintain quality.
Machining Parameters: Optimize cutting speed, feed rate, and coolant usage to minimize heat and tool wear. For titanium, speeds of 10–30 m/min and feed rates of 0.02–0.05 mm/rev prevent overheating and ensure thread accuracy.
Quality Control: Regular inspection with thread gauges or coordinate measuring machines (CMM) ensures compliance with specifications. Geometric dimensioning and tolerancing (GD&T) standards facilitate precise design communication.
Surface Preparation: Deburring and cleaning workpieces before threading prevent defects like thread stripping. For prototypes, a uniform surface finish enhances thread quality and motion efficiency.
Conclusion
Lead screws, power screws, and translation screws are essential for precise linear motion in industries like manufacturing, robotics, and aerospace. Understanding their types, applications, material selection, and machining processes enables informed decisions for prototyping and production. By optimizing thread design, material choice, and machining parameters, manufacturers can achieve high precision and reliability. Addressing difficulties like precision complexity and machining challenges ensures consistent quality in lead screw production.
FAQ: Lead Screws – Types, Applications, and Machining
What is the difference between lead screws and ball screws?
Lead screws (e.g., Acme, square thread) rely on sliding contact between threads and nuts, resulting in moderate efficiency (30–60%) and higher friction. They are cost-effective for low-speed, moderate-load applications.
Ball screws use recirculating ball bearings in a helical raceway, reducing friction and achieving efficiency up to 90%. They excel in high-speed, high-precision tasks (e.g., robotics, CNC systems) but are more expensive.
What machining methods are used for lead screws?
Thread Cutting: Uses taps/dies to remove material; suitable for standard threads (e.g., M10×1.5 Acme) with speeds of 10–30 m/min (steel) or 15–50 m/min (aluminum).
Thread Milling: Flexible for custom/non-standard threads, offering high precision; ideal for prototyping with speeds of 50–150 m/min.
Swiss Machining: Used for miniature screws (±0.0025 mm tolerance) with spindle speeds up to 12,000 RPM.
Thread Rolling: Cold-forms threads via dies, enhancing strength; cost-effective for high-volume production but not for small batches.
How do I choose between Acme and ball screws for CNC machines?
Acme screws: Balanced strength and efficiency; suitable for moderate-speed CNC tasks (e.g., 3D printers) with lower cost.
Ball screws: Higher efficiency (up to 90%) and precision; better for high-speed, high-cycle CNC systems (e.g., milling machines) where accuracy is critical.