The impeller is a critical component of centrifugal pumps, significantly impacting operational efficiency and stability. Model impellers, typically scaled-down versions of production impellers, are used in high-precision test rigs to validate performance data. Their manufacturing accuracy directly affects the reliability of test results. This article analyzes and compares four primary manufacturing techniques for centrifugal pump model impellers—split manufacturing, integral CNC machining, special processing, and 3D printing—based on their geometric complexity and processing challenges. Each method’s advantages and limitations are discussed to provide a comprehensive guide for selecting optimal manufacturing routes.
Split Manufacturing
Split manufacturing is often employed for model impellers with small diameters and numerous blades, resulting in narrow flow passages that restrict machining access. This method divides the impeller into components—blades, front cover plate, rear cover plate, and hub—which are machined separately and assembled into a complete impeller. Companies such as Germany’s VOITH Group, France’s ALSTOM, and China’s Harbin Electric Machinery have successfully applied this technique to produce model impellers for water turbines, which share similar dimensional and geometric characteristics with centrifugal pump impellers.
In split manufacturing, blades are designed with a segmented rear cover plate, and the hub is integrated using an inlaid structure. These components are assembled using threaded fasteners to form the impeller. Blades are typically machined from customized polygonal or near-net-shape cast blanks with minimal machining allowance. Rough milling is performed on standard three-axis machine tools, while multi-axis machining centers handle finish milling to achieve high surface accuracy. The rear cover plate and hub are processed through CNC turning, followed by milling to create positioning slots for blade assembly and drilling for fastener holes.
Advantages:
- Reduces manufacturing complexity by processing components individually, enabling the production of small-diameter, multi-blade impellers with limited machining access.
- Utilizes a rough-and-finish machining strategy, leveraging multiple machines to enhance efficiency and reduce costs.
- Mature technology widely adopted by major manufacturers, ensuring reliable implementation.
Limitations:
- Individual blade machining leads to potential inconsistencies, requiring high-precision equipment and fixturing.
- Assembly errors and manual adjustments during blade integration with cover plates compromise overall impeller integrity.
- Thin-walled blades exhibit low rigidity, increasing the risk of vibration and deformation during machining.
- Cast blade blanks are prone to defects such as porosity or inclusions, heavily dependent on the casting supplier’s expertise.
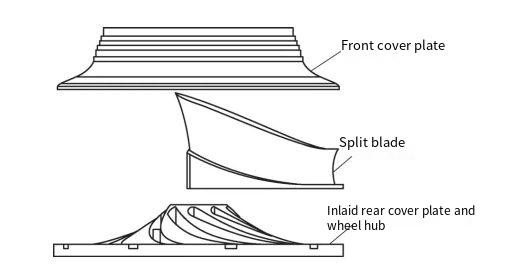
Integral Manufacturing
Integral manufacturing eliminates assembly-related errors by machining the impeller as a single unit, improving structural rigidity and suppressing machining-induced vibrations. However, the complex geometry of impellers, particularly closed designs with intricate flow passages, poses significant manufacturing challenges. Integral manufacturing is divided into semi-open and fully closed approaches, each addressing different impeller configurations.
Semi-Open Integral Manufacturing
Semi-open integral manufacturing involves machining the blades, rear cover plate, and hub as a single unit, with the front cover plate machined separately and assembled later. This method is suitable for impellers with fewer blades (e.g., ≤7) and wider flow passages, allowing sufficient tool access. Advances in CNC technology and multi-axis machining centers have made this approach feasible, supported by programming software like UG NX and Cimatron, which provide algorithms for impeller machining. Specialized CNC machines, such as those developed by Switzerland’s StarragHeckert Group, include dedicated impeller machining modules.
The machining process typically involves roughing with a “3+2” axis strategy for high material removal rates, followed by multi-axis simultaneous machining for finishing. For example, China’s Dongfang Electric has achieved blade surface dimensional accuracy of ±0.03 mm using this approach. Large-diameter tools can be used in semi-open designs, enhancing efficiency and surface quality.
Advantages:
- High production efficiency and surface quality when machining space allows the use of robust, large-diameter tools.
- Improved blade consistency due to single-unit machining, reducing variability.
- Multi-axis machining minimizes setup changes, enhancing precision compared to traditional three-axis methods.
Limitations:
- Complex toolpath generation must account for interference between adjacent blades and ensure access to all areas, challenging programming capabilities.
- Assembly of the front cover plate introduces unavoidable errors, affecting overall accuracy.
- Thin-walled blades remain susceptible to vibration and deformation due to the absence of the front cover plate during machining.
Fully Closed Integral Manufacturing
Fully closed integral manufacturing produces the entire impeller prototyping, including both cover plates, as a single unit. The addition of the front cover plate creates narrow, twisted internal cavities, making this one of the most challenging manufacturing processes. Three primary techniques are employed: multi-axis CNC machining, special processing, and 3D printing.
Multi-Axis CNC Machining
Multi-axis CNC machining is the most widely used method for fully closed impellers due to its flexibility, high precision, and process stability. Companies like Pratt & Whitney, GE, and Rolls-Royce have applied this technique to manufacture titanium alloy impellers for aerospace applications. Research institutions, such as Shanghai Jiao Tong University and Northwestern Polytechnical University, have developed detailed process plans and custom tools to achieve successful machining.
Key considerations in multi-axis CNC machining include:
- Toolpath Safety: Tool interference with blades and cover plates requires highly reliable toolpaths with low tolerance for errors.
- Segmented Machining: Narrow flow passages necessitate machining from both inlet and outlet sides, requiring careful division of machining zones and feasible tool angles within the tool’s effective length.
- Toolpath Smoothness: Smooth five-axis toolpaths and gradual tool axis transitions are critical to avoid vibrations that could damage thin-walled blades.
- Material Removal Efficiency: Large stock volumes and restricted tool sizes demand optimized strategies to balance efficiency and cost.
Specialized software, such as Concepts NREC’s MAX-CAM, automates the generation of smooth, interference-free five-axis toolpaths, enabling high-quality impeller production. Dongfang Electric has successfully used DMU-100 five-axis machining centers and virtual manufacturing to ensure toolpath reliability.
Advantages:
- Eliminates welding and assembly, ensuring excellent impeller integrity and blade consistency.
- High surface accuracy and performance, ideal for demanding applications.
Limitations:
- Complex programming tailored to specific impeller designs, lacking universal applicability.
- Requires advanced machining centers, custom tools, and skilled programmers, increasing costs.
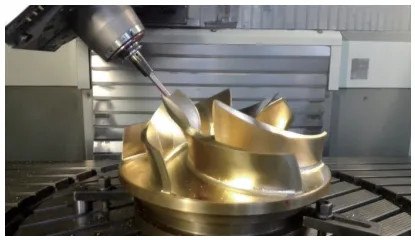
Special Processing
Special processing techniques, such as electrical discharge machining (EDM) and electrochemical machining (ECM), are used when CNC machining cannot access confined impeller areas. EDM removes material through pulsed spark discharges between a tool electrode and the workpiece, while ECM dissolves material via anodic dissolution in an electrolyte. EDM offers higher precision (surface roughness Ra 0.8–1.6 μm), while ECM provides higher efficiency.
Both methods are force-free, suitable for hard-to-machine materials like titanium alloys, and achieve stable, high-quality results. Combined with multi-axis CNC positioning, these techniques enable complex surface machining. GE has used ECM for steel and titanium impellers, while Germany’s ZK employs graphite electrodes for EDM. Chinese universities, including Shanghai Jiao Tong and Nanjing University of Aeronautics and Astronautics, have developed EDM-processed impellers.
Advantages:
- Effective for machining inaccessible areas, complementing CNC methods.
- High stability and quality, unaffected by material hardness.
Limitations:
- Complex electrode design and path planning increase technical difficulty.
- High equipment and operational costs limit widespread adoption.
3D Printing
3D printing, or additive manufacturing, builds impellers layer-by-layer from materials like stainless steel or copper, ideal for complex geometries without requiring blanks or molds. Selective laser melting (SLM) is commonly used for model impellers. Russia’s Tushino factory has produced mixed-flow impellers using 3D-printed molds, while China’s Ningxia Shared Cast Steel created a 1600 mm diameter impeller with a minimum wall thickness of 8 mm. Harbin Electric Machinery delivered a full-scale water turbine impeller in 2020 using additive manufacturing.
Advantages:
- Forms complex shapes without assembly, reducing material waste and costs.
- Eliminates the need for custom tooling, enhancing flexibility.
Limitations:
- Current dimensional accuracy (±0.5 mm) and surface roughness (Ra 3.2–6.3 μm) are inferior to CNC machining, requiring extensive post-processing.
- Material and process limitations restrict applications for high-precision impellers.
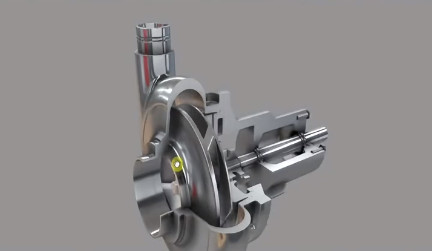
Comparison of Manufacturing Techniques
Technique | Advantages | Limitations |
---|---|---|
Split Manufacturing | Handles narrow passages, mature technology, cost-effective | Assembly errors, blade inconsistency, casting defects |
Integral CNC Machining | High precision, eliminates assembly, good rigidity | Complex toolpaths, high equipment costs |
Special Processing | Accesses confined areas, force-free, high stability | Complex electrode design, high costs |
3D Printing | Forms complex shapes, no tooling, low material waste | Poor accuracy, rough surfaces, post-processing required |
Conclusion
The manufacturing of centrifugal pump model impellers is critical for validating hydraulic performance. Split manufacturing is ideal for small, multi-blade impellers, offering cost-effectiveness but suffering from assembly errors. Integral CNC machining provides superior precision and integrity for semi-open and fully closed designs, though it demands advanced equipment and programming. Special processing excels in inaccessible areas but is cost-intensive. 3D printing offers flexibility for complex geometries but requires further development for precision. Selecting the appropriate method depends on impeller design, precision requirements, and cost constraints, with each technique providing viable solutions for high-quality impeller production.