Mounting screws are essential fasteners used to secure equipment to surfaces, racks, or assemblies in various industries, including electronics, construction, and manufacturing. This guide provides a detailed, technical overview of mounting screws, including their types, specifications, materials, and applications. Designed for engineers, technicians, and procurement professionals, this article offers a systematic exploration of mounting screws to aid in selecting the right fastener for specific needs.
Definition and Purpose of Mounting Screws
Mounting screws are externally threaded fasteners designed to attach components to a surface or structure, often engaging with a pre-threaded hole or nut. Unlike bolts, which typically require a nut for tightening, mounting screws are often self-contained, with the thread engaging directly with the material or a threaded insert. Their primary purpose is to provide a secure, reliable connection that withstands mechanical stress, vibration, and environmental factors.
These screws are critical in applications such as securing server racks, mounting electrical enclosures, or assembling machinery. They are manufactured to precise standards to ensure compatibility and performance, adhering to systems like the ISO metric screw thread or ANSI standards.
Types of Mounting Screws
Mounting screws come in various types, each tailored to specific applications. Below is a detailed breakdown of the most common types used in industrial and commercial settings.
Machine Screws
Machine screws are uniform-threaded fasteners designed to mate with a pre-tapped hole or nut. They are commonly used in precision applications, such as electronics or machinery, where a strong, reliable connection is needed. Machine screws typically have a cylindrical shank and are available in metric (e.g., M5, M6) and imperial (e.g., 10-32, 12-24) thread standards.
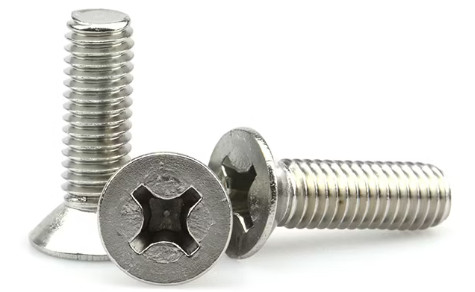
Self-Tapping Screws
Self-tapping screws create their own thread when driven into a material, eliminating the need for a pre-tapped hole. They are ideal for applications in softer materials like plastic or thin metal sheets. Common thread forms include Type A, Type AB, and Type B, each with specific thread-cutting or thread-forming characteristics.
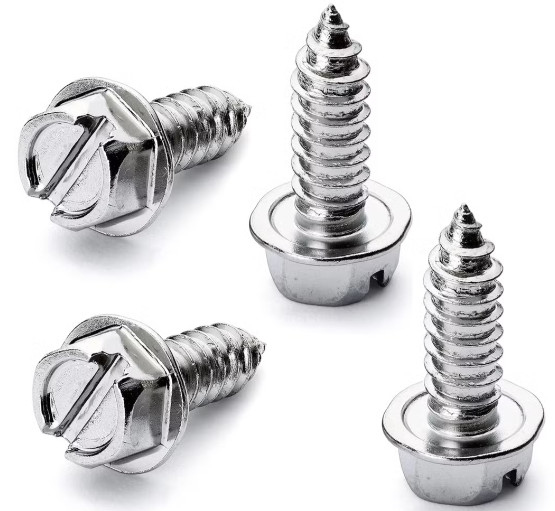
Rack Screws
Rack screws are specialized for mounting equipment to 19-inch server racks, commonly used in IT and telecommunications. They typically feature thread types like 10-32, 12-24, M5, or M6 and are paired with cage nuts or threaded rails. Their design ensures compatibility with standardized rack systems.
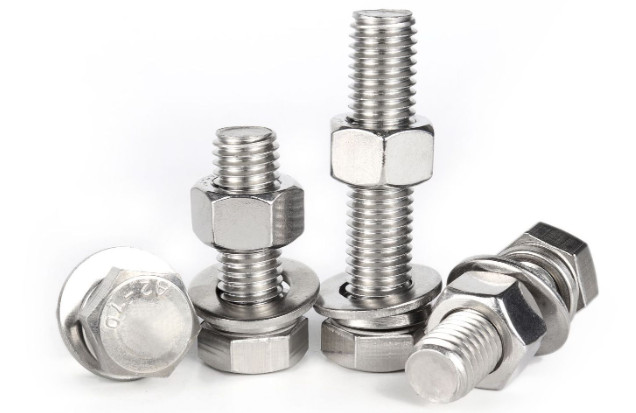
Wood Screws
Wood screws, while less common in industrial mounting, are used in applications involving wooden structures. They feature coarse threads and a tapered point to grip wood fibers securely. For mounting purposes, they are often used in furniture assembly or construction.
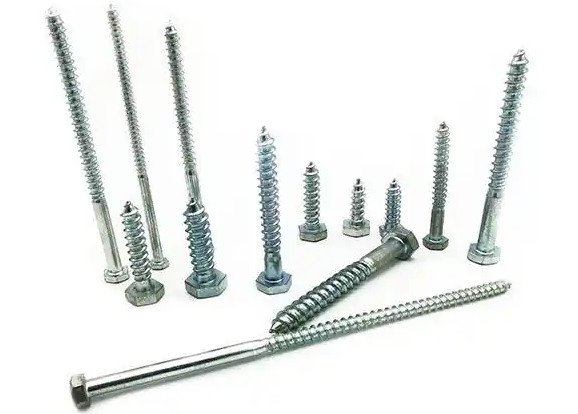
Technical Specifications of Mounting Screws
The performance of mounting screws depends on their technical specifications, which dictate compatibility, strength, and durability. Below is a table summarizing key parameters for common mounting screw types.
Screw Type | Thread Standard | Major Diameter (mm/in) | Pitch (mm/in) | Common Lengths (mm) | Typical Applications |
---|---|---|---|---|---|
Machine Screw | M5, M6, 10-32, 12-24 | 5-6 mm / 0.19-0.24 in | 0.8-1.0 mm / 24-32 TPI | 6-50 | Electronics, machinery |
Self-Tapping Screw | Type A, AB, B | 3-6 mm / 0.12-0.24 in | 0.7-1.4 mm / 10-24 TPI | 6-100 | Plastic, thin metal |
Rack Screw | M5, M6, 10-32, 12-24 | 5-6 mm / 0.19-0.24 in | 0.8-1.0 mm / 24-32 TPI | 10-25 | Server racks, IT equipment |
Wood Screw | Coarse thread | 3-8 mm / 0.12-0.31 in | 1.2-2.0 mm / 8-18 TPI | 10-100 | Wooden structures |
Notes: Major diameter is the largest diameter of the thread (crest). Pitch is the distance between threads, measured in millimeters for metric screws or threads per inch (TPI) for imperial screws. Lengths vary based on application requirements.
Materials and Coatings
The material and coating of a mounting screw significantly affect its performance, corrosion resistance, and suitability for specific environments. Below are the most common materials and coatings used.
Materials
Steel: Carbon steel is widely used for its strength and affordability. It is suitable for general-purpose applications but requires coatings to prevent corrosion.
Stainless Steel: Stainless steel (e.g., A2, A4 grades) offers excellent corrosion resistance, making it ideal for outdoor or high-humidity environments.
Brass: Brass screws are corrosion-resistant and aesthetically pleasing, often used in decorative or electrical applications due to their conductivity.
Aluminum: Lightweight and corrosion-resistant, aluminum screws are used in applications where weight is a concern, such as aerospace.
Coatings
Zinc Plating: Provides basic corrosion resistance for steel screws, suitable for indoor environments.
Black Oxide: Offers a decorative finish and moderate corrosion resistance, commonly used for rack screws.
Nickel Plating: Enhances corrosion resistance and appearance, often used in electronics.
Passivation: Applied to stainless steel to enhance its natural corrosion resistance.
Standards and Thread Systems
Mounting screws are manufactured to specific standards to ensure compatibility and performance. The two primary thread systems are ISO metric and Unified (ANSI) threads.
ISO Metric Threads
ISO metric threads, designated by an "M" (e.g., M6), are the most common worldwide. The designation indicates the nominal outer diameter in millimeters (e.g., M6 = 6 mm). The pitch, typically coarse (e.g., M6 x 1.0), ensures compatibility with standard nuts and tapped holes.
Unified Threads (ANSI)
Unified threads, common in North America, use designations like 10-32 or 12-24. The first number indicates the diameter (e.g., #10), and the second indicates threads per inch (TPI). These are prevalent in rack mounting and machinery.
Applications of Mounting Screws
Mounting screws are used across industries due to their versatility. Below are key applications with specific considerations.
Electronics and IT
In electronics, mounting screws secure components like circuit boards or enclosures. Rack screws (e.g., M6, 10-32) are used in server racks to mount servers and networking equipment. Thread compatibility and torque control are critical to avoid damaging sensitive components.
Construction and Furniture
Wood screws and self-tapping screws are used in construction and furniture assembly. Their coarse threads provide strong holding power in wood or drywall, but care must be taken to avoid over-tightening, which can strip the material.
Automotive and Machinery
Machine screws are used in automotive and machinery applications for assembling components like engines or chassis. High-strength materials (e.g., Grade 8.8 steel) are often required to withstand vibration and load.
Selection Considerations
Choosing the right mounting screw involves several factors to ensure performance and reliability. Below is a systematic approach to selection.
Factor | Consideration | Example |
---|---|---|
Thread Type | Match thread to mating component (metric, unified, or self-tapping). | M6 for ISO metric nuts, 10-32 for rack mounting. |
Material | Select based on environment (e.g., stainless steel for outdoor use). | A2 stainless steel for coastal applications. |
Length | Ensure sufficient engagement without bottoming out. | 20 mm for a 15 mm thick panel with nut. |
Head Type | Choose based on tool access and aesthetic needs. | Pan head for electronics, countersunk for flush finish. |
Load Requirements | Consider shear and tensile strength for load-bearing applications. | Grade 8.8 for high-load machinery. |
Installation Best Practices
Proper installation ensures the longevity and reliability of mounting screws. Follow these guidelines:
- Pre-Drilling: For self-tapping screws, use the correct tapping drill diameter to avoid material damage.
- Torque Control: Apply appropriate torque to prevent stripping or over-tightening, using a torque screwdriver for precision.
- Thread Engagement: Ensure at least 1.5 times the screw diameter is engaged in the mating thread for secure fastening.
- Alignment: Align components to avoid cross-threading, especially in delicate materials like aluminum.
- Inspection: Verify thread compatibility and condition before installation, using gauges if necessary.
Common Issues and Solutions
While mounting screws are reliable, certain issues can arise during selection or installation. Below are common problems and their solutions.
Thread Mismatch: Using a metric screw in an imperial threaded hole (or vice versa) can result in poor engagement. Solution: Verify thread standards (e.g., M5 vs. 10-32) before installation.
Corrosion: Steel screws in humid environments may rust. Solution: Use stainless steel or zinc-plated screws for corrosion resistance.
Over-Tightening: Excessive torque can strip threads or damage components. Solution: Use a torque-controlled tool and follow manufacturer torque specifications.
Insufficient Thread Engagement: Short screws may not provide adequate holding strength. Solution: Select a screw length that ensures sufficient thread engagement (e.g., 1.5 times the diameter).
Conclusion
Mounting screws are indispensable in securing components across industries, from IT to construction. By understanding their types, specifications, materials, and applications, professionals can make informed decisions to ensure reliable and durable installations. Always consider thread standards, material compatibility, and installation best practices to achieve optimal performance.