This guide provides a comprehensive overview of nickel alloys, their applications, and machining techniques, with a strong emphasis on processing methods for prototyping and material handling. It covers material properties, practical applications, and detailed machining parameters to ensure optimal performance in manufacturing.
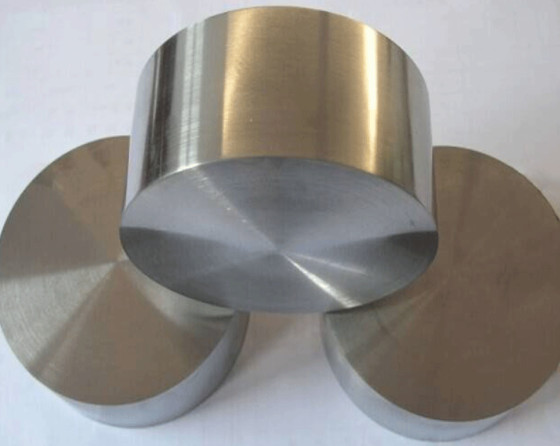
Properties of Nickel Alloys
Nickel alloys are engineered materials valued for their mechanical and chemical properties, making them suitable for extreme environments. Composed primarily of nickel with elements like chromium, molybdenum, iron, and copper, these alloys offer unique characteristics. Key properties include:
- Corrosion Resistance: Nickel alloys resist corrosion in acidic, alkaline, and saline conditions. Monel 400, for instance, withstands seawater corrosion, ideal for marine applications.
- High-Temperature Strength: Alloys like Inconel 718 maintain integrity at temperatures up to 1300°F (704°C), suitable for aerospace components.
- Mechanical Strength: Tensile strengths range from 500 MPa (Monel 400) to over 1200 MPa (Inconel 718), depending on composition.
- Ductility and Toughness: These alloys balance ductility and toughness, enabling complex forming while resisting fracture.
- Thermal Stability: Nickel alloys maintain dimensional stability under thermal cycling, critical for high-temperature applications.
These properties make nickel alloys essential for industries requiring durability and reliability.
Applications of Nickel Alloys
Nickel alloys are used in industries where performance under harsh conditions is critical. Key applications include:
Aerospace Industry
Inconel 718 is used for turbine blades and exhaust systems due to its high-temperature strength (yield strength ~1000 MPa at 1200°F/649°C).
Marine and Chemical Processing
Monel 400 is employed in marine components like propeller shafts, while Hastelloy C-276 is used in chemical reactors, with a corrosion rate of <0.1 mm/year in hydrochloric acid.
Energy Sector
Inconel 625 is used in oil and gas pipelines for sour gas resistance, and nickel alloys are chosen for nuclear reactor components due to radiation stability.
Medical and Electronics
Nitinol is used in medical stents for its shape memory, and Alloy 42 is used in electronics for low thermal expansion.
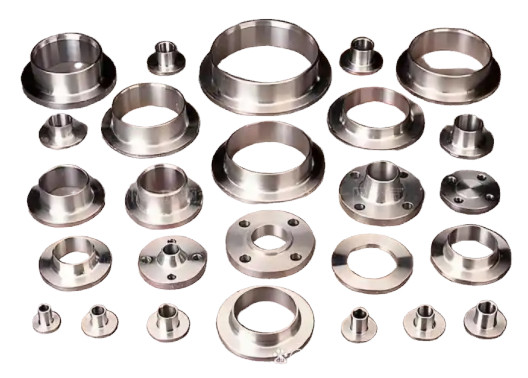
Machining Nickel Alloys
Machining nickel alloys is challenging due to their high strength, work-hardening tendencies, and heat resistance. This section provides an in-depth look at machining techniques, tools, and parameters, with a focus on processing methods for prototyping and production.
Tool Selection for Machining
Selecting the right tools is critical for machining nickel alloys. Carbide tools with positive rake angles (5-10°) reduce cutting forces and heat generation. Coated carbide tools, such as those with TiAlN or AlTiN coatings, extend tool life by up to 30% compared to uncoated tools. For high-speed machining, ceramic tools (e.g., SiAlON) are effective but require rigid setups to minimize vibration. Tool geometry should include a honed edge radius of 0.02-0.04 mm to reduce chipping.
Machining Parameters
Precise machining parameters are essential to achieve quality results while minimizing tool wear. The table below outlines recommended parameters for turning operations on common nickel alloys:
Alloy | Cutting Speed (m/min) | Feed Rate (mm/rev) | Depth of Cut (mm) | Coolant |
---|---|---|---|---|
Inconel 718 | 30-50 | 0.1-0.2 | 0.5-2.0 | Water-based emulsion, 10% concentration |
Monel 400 | 50-80 | 0.15-0.25 | 0.5-3.0 | Oil-based coolant |
Hastelloy C-276 | 25-45 | 0.1-0.15 | 0.5-1.5 | Water-based emulsion, 8-12% concentration |
These parameters are optimized for CNC lathes with rigid setups. For milling, reduce cutting speeds by 10-15% and use climb milling to minimize work hardening. Coolant flow should be maintained at 10-15 L/min to dissipate heat effectively.
Key Machining Techniques
Several machining techniques are employed for nickel alloys, each suited to specific geometries and requirements. Below are the primary methods with detailed considerations:
- Turning: Used for cylindrical components like shafts and fittings. Low cutting speeds (30-50 m/min for Inconel 718) and high coolant flow (15 L/min) are critical to manage heat and prevent work hardening. Use a nose radius of 0.8-1.2 mm to improve surface finish (Ra 0.8-1.6 µm).
- Milling: Suitable for flat surfaces and complex geometries. End milling with coated carbide tools at 40-60 m/min and feed rates of 0.05-0.1 mm/tooth is recommended. Climb milling reduces cutting forces and improves surface quality. For slot milling, use a step-over of 25-40% of tool diameter to avoid excessive tool wear.
- Drilling: Requires cobalt or carbide drills with a 135° point angle and peck drilling cycles (0.5-1 mm per peck) to ensure chip evacuation and prevent work hardening. Use a cutting speed of 20-40 m/min and feed rate of 0.05-0.1 mm/rev for holes up to 10 mm in diameter.
- Grinding: Employed for high-precision components with tight tolerances (±0.01 mm). Use aluminum oxide wheels (60-80 grit) at 20-30 m/s with a cross-feed of 0.01-0.02 mm/pass. Coolant is essential to prevent thermal damage to the workpiece.
- Electrical Discharge Machining (EDM): Used for intricate shapes and hard-to-machine areas. Wire EDM with brass wire (0.25 mm diameter) at a pulse duration of 1-2 µs and current of 10-15 A achieves tolerances of ±0.005 mm. Die-sinking EDM is effective for deep cavities but requires careful electrode design.
Prototyping Considerations
Prototyping with nickel alloys requires additional care to achieve dimensional accuracy and surface quality. Key practices include:
- Reduced Cutting Speeds: Lower speeds by 20-30% compared to production runs (e.g., 25-40 m/min for Inconel 718) to minimize heat buildup.
- Frequent Tool Inspection: Inspect tools every 10-15 minutes of machining to detect wear, as nickel alloys cause rapid tool degradation.
- Robust Workholding: Use hydraulic or vacuum chucks to prevent vibration, which can cause chatter marks and poor surface finish.
- Surface Finish Goals: Target a surface roughness (Ra) of 0.8-1.6 µm for prototypes, achievable with fine feeds (0.05-0.1 mm/rev) and sharp tools.
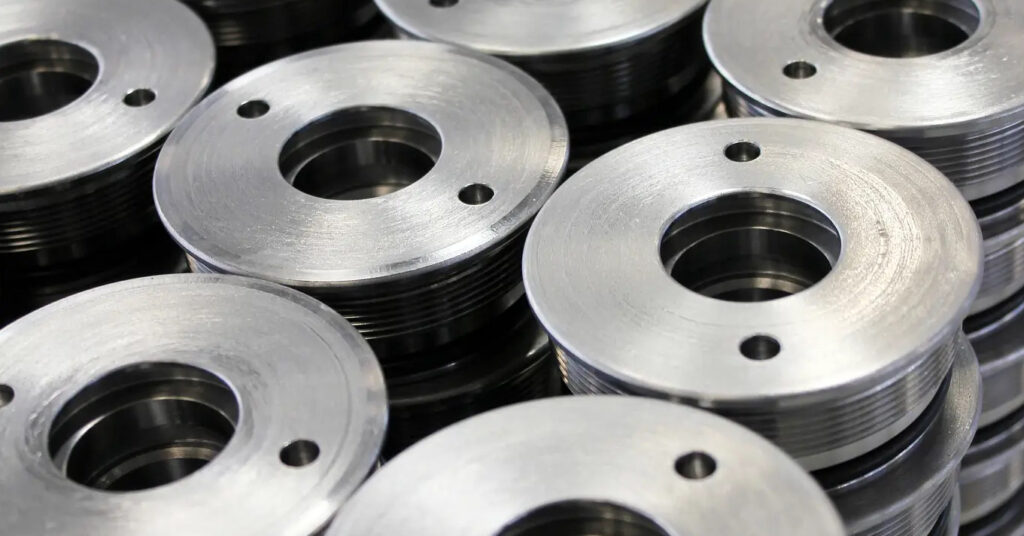
Challenges in Machining Nickel Alloys
Machining nickel alloys presents specific difficulties that require careful management:
- Work Hardening: Rapid hardening during machining increases cutting forces. Use sharp tools and single-pass cuts to minimize this effect.
- Heat Generation: High cutting temperatures (up to 1000°C) can degrade tools. High-pressure coolant (70-100 bar) helps dissipate heat.
- Tool Wear: Abrasive wear is common due to the alloys’ hardness. Coated tools and frequent replacements (every 20-30 minutes for Inconel) are necessary.
- Chip Formation: Nickel alloys produce tough, stringy chips. Use chip breakers and high coolant flow to ensure proper chip evacuation.
Material Processing for Prototyping
Effective prototyping with nickel alloys involves additional processing steps to enhance material properties and machinability.
Heat Treatment
Heat treatment optimizes mechanical properties. For Inconel 718, solution annealing at 980°C for 1 hour followed by aging at 720°C for 8 hours increases hardness to 40-45 HRC. Monel 400 can be annealed at 760°C for 30 minutes to improve machinability.
Forging and Forming
Forging is performed at 900-1200°C. Inconel 625 requires a forging temperature of 1100°C to ensure uniform grain structure. Cold forming is feasible for thin sections but requires forces of 1000-1500 MPa due to high strength.
Welding
Welding uses gas tungsten arc welding (GTAW) with low heat input (1-2 kJ/mm) to prevent cracking. For Hastelloy C-276, use ERNiCrMo-3 filler metal and preheat to 200°C for thick sections to reduce residual stresses.
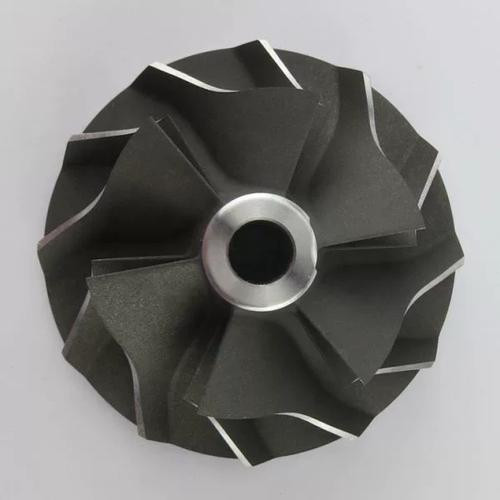
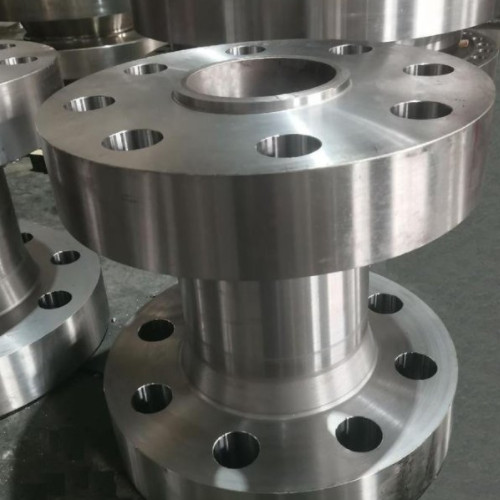
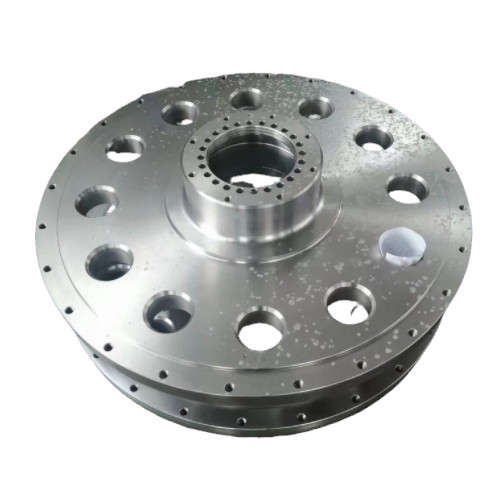
Summary of Key Machining Parameters
The table below summarizes critical parameters for machining nickel alloys:
Process | Alloy | Parameter | Value |
---|---|---|---|
Turning | Inconel 718 | Cutting Speed | 30-50 m/min |
Milling | Monel 400 | Feed Rate | 0.05-0.1 mm/tooth |
Drilling | Hastelloy C-276 | Peck Depth | 0.5-1 mm |
Grinding | Inconel 625 | Wheel Speed | 20-30 m/s |
Conclusion
Nickel alloys are critical for applications in aerospace, marine, energy, and medical industries due to their corrosion resistance and high-temperature strength. Machining these alloys requires precise tool selection, optimized parameters, and robust techniques to address challenges like work hardening and tool wear. By following the detailed guidelines and parameters provided, manufacturers can achieve high-quality prototypes and components with nickel alloys.