Titanium alloys are characterized by their silver-gray appearance and metallic luster. With a density of 4.51 g/cm³, titanium is heavier than aluminum but lighter than steel, copper, or nickel, classifying it as a lightweight metal. Key properties include a high melting point (approximately 1,668°C), high hardness (Rockwell C 30-40 depending on the alloy), and high tensile strength (up to 1,000 MPa for some grades). Titanium alloys exhibit excellent ductility when pure, though impurities can increase brittleness and hardness. They are non-toxic, non-magnetic, and capable of withstanding high temperatures. Their corrosion resistance is exceptional, surpassing that of stainless steel by approximately 15 times, particularly in seawater environments, earning titanium the moniker “future metal” or “dream metal” in industrial applications. As the “third metal” after iron and aluminum, titanium alloys are indispensable in high-performance sectors.
In aerospace, titanium alloys are widely used in aircraft engines and structural components, with usage ranging from 15% to 41% in aircraft such as the Su-27, F-14, F-15, and F-22. In civilian applications, their biocompatibility makes them ideal for medical implants, including dental prosthetics, bone replacements, and joint repairs. Additionally, titanium is employed in sports equipment like tennis rackets, badminton rackets, and golf club heads, leveraging its strength-to-weight ratio.
Principles of Chemical Etching
Chemical etching, also known as chemical milling, involves immersing a workpiece in a chemical solution that selectively dissolves the material. This process enables precise material removal within predefined areas and depths by controlling the chemical solution and applying protective measures, such as masking. The etching process involves multiple localized reactions, including diffusion, adsorption, chemical reactions, and electrochemical reactions. For alloys, the presence of varying metal potentials results in both chemical and electrochemical reactions, with the dominant mechanism depending on the material’s composition and content. In pure metals, chemical etching primarily involves the dissolution of crystal boundaries and grains.
The etching rate is influenced by the atomic structure of the material. Areas with wider interatomic spacing dissolve faster, resulting in uneven surfaces. Crystal boundaries, where lattice distortions and impurities are concentrated, often experience accelerated dissolution, potentially leading to pitting corrosion. However, for most materials except certain steels, grain boundary corrosion has negligible effects on mechanical or fatigue properties.
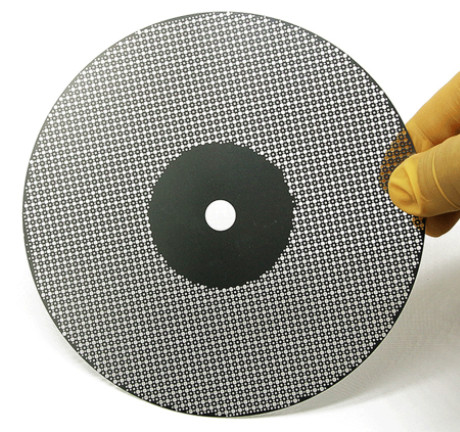
Classification of Chemical Etching
Chemical etching can be categorized based on the processing method, as shown in the table below:
Category | Description | Applications |
---|---|---|
Overall Etching | Uniform material removal across the entire workpiece surface. | Reducing thickness of large panels or removing surface layers. |
Localized Etching | Selective material removal in specific areas using masks or protective coatings. | Creating intricate patterns or reducing weight in designated regions. |
Overall etching is suitable for uniform thickness reduction, while localized etching allows for precise patterning, such as creating complex geometries or lightweight structures.
Technical Advantages of Chemical Etching
Chemical etching offers distinct advantages over traditional mechanical machining, particularly for titanium alloys:
- No Mechanical Stress: Unlike mechanical methods, etching does not apply force to the workpiece, preventing deformation in thin or large-area parts.
- Material Versatility: Etching is effective regardless of the material’s state—whether formed, heat-treated, or hardened—making it suitable for a wide range of titanium alloys.
- Structural Simplification: Etching enables the production of monolithic structures, replacing complex assemblies involving welding, riveting, or bonding, which reduces weight and assembly time.
- High Efficiency: Multiple parts can be processed simultaneously, enhancing production rates.
- Tapered Sections: Controlled immersion rates allow the creation of tapered cross-sections, ideal for applications like aircraft wings.
- Material Savings: Compared to forging, casting, or mechanical machining, etching minimizes material waste.
- Design Flexibility: Changes in part design require only modifications to the protective mask, facilitating rapid prototyping.
- Cost-Effectiveness: Simple equipment and low investment make etching an economical choice for complex geometries.
- Surface Quality: Etching achieves low surface roughness (Ra 0.8-3.2 µm) and high precision (±0.01 mm in some cases).
Applications in Aerospace Industry
Chemical etching is a critical technology in aerospace manufacturing, particularly for titanium alloy components. Its applications include:
Weight Reduction
Etching removes excess material (“dead weight”) from specific regions of aircraft structures, such as fuselage panels or wing skins, based on stress distribution and assembly requirements. For complex single- or double-curvature surfaces, etching is more practical than mechanical milling, which struggles with thin-walled or curved geometries. For instance, titanium alloy components in the Boeing 747 and Tu-144 have been etched to reduce weight while maintaining structural integrity.
Monolithic Structures
Etched monolithic structures offer superior aerodynamic performance, with smoother surfaces and better symmetry compared to riveted assemblies. They also provide higher strength-to-weight ratios, reducing component weight by 15-20% and improving airtightness. Etching reduces the need for fasteners, cutting assembly costs by up to 50% and enhancing corrosion resistance.
Tapered Components
Etching excels at producing long, thin components with gradually varying thicknesses, such as aircraft wing skins that transition from thicker roots (e.g., 5 mm) to thinner tips (e.g., 1 mm). This capability optimizes structural efficiency based on load distribution.
Hard-to-Machine Materials
Titanium alloys, including high-strength grades (e.g., Ti-6Al-4V with tensile strength >900 MPa) and surface-hardened forgings or castings, are challenging for conventional machining. Etching effectively removes hardened layers, such as oxide or nitride coatings, from components like turbine blades.
Extruded Profiles
Extruded titanium profiles often exhibit coarse surface grains that impair mechanical performance. Etching removes these surface defects, improving fatigue resistance and enabling the use of complex extruded shapes in aircraft manufacturing.
Thin-Walled Components
Etching is ideal for processing thin-walled parts (e.g., thicknesses <1 mm) with complex contours, such as wing, tail, or fuselage skins, without causing deformation common in mechanical machining.
Applications in Civilian Industries
Beyond aerospace, chemical etching is widely applied in civilian industries for processing titanium, aluminum, magnesium, nickel, copper, and steel alloys. Specific applications include:
- Precision Components: Etching is used to refine gear electrodes for straight bevel gears, achieving precise tooth profiles and low surface roughness (Ra 0.4-1.6 µm).
- Medical Devices: Titanium alloy heart valve frames and other biocompatible implants are etched to achieve intricate shapes and smooth surfaces critical for medical applications.
- Consumer Electronics: Etching produces titanium alloy components like camera shutter disks and resistance wire sheets with high precision and minimal material waste.
- Automotive: In high-performance vehicles, etching reduces the weight of titanium or aluminum body panels. For example, a U.S. company used etching to reduce racecar body weight by 90.8 kg, improving performance.
- Filtration Systems: Etching creates fine mesh filters with precise pore sizes (e.g., 0.1-0.5 mm) for industrial and medical applications.
Current State of Chemical Etching Technology
Chemical etching for titanium alloys emerged in the 1950s and has since evolved significantly. Early etching solutions, such as hydrofluoric acid (HF) combined with chromic acid in the U.S. or nitric acid in the U.K., were effective but posed challenges. Chromic acid-based solutions, for instance, caused hydrogen embrittlement, reducing mechanical properties, and were environmentally harmful due to chromium waste. Modern etching solutions typically use HF-nitric acid mixtures or silicofluoric acid to minimize environmental impact and improve material integrity.
In China, etching solutions for titanium alloys like TC1 and TC4 have been developed with long service life, low environmental impact, and surface roughness values as low as Ra 0.8 µm. Common etching solutions include:
Solution Type | Composition | Characteristics |
---|---|---|
HF-Based | Hydrofluoric acid alone | High etching rate, suitable for simple geometries |
HF-Nitric | Hydrofluoric acid + nitric acid | Balanced etching rate, improved surface quality |
HF-Chromic | Hydrofluoric acid + chromic acid | High precision but causes hydrogen embrittlement |
Silicofluoric | Silicofluoric acid | Environmentally friendly, moderate etching rate |
While etching is widely used in aerospace engine and airframe manufacturing, its adoption in civilian industries remains limited, primarily serving as an auxiliary process for high-precision components.
Conclusion
The unique properties of titanium alloys, including high strength, low density, and exceptional corrosion resistance, make them critical in aerospace and civilian applications. Chemical etching addresses the challenges of machining titanium alloys, offering a stress-free, precise, and cost-effective method for producing complex geometries. Its ability to reduce weight, simplify structures, and process difficult materials has made it indispensable in aerospace, while its applications in civilian industries continue to expand. As etching solutions and techniques improve, this technology will further enhance the utility of titanium alloys across diverse sectors.