Titanium alloys are advanced materials that combine titanium with other elements to create lightweight, durable, and corrosion-resistant metals. Known for their exceptional strength-to-weight ratio and versatility, titanium alloys play a critical role in industries like aerospace, medical, and marine engineering. This article provides an in-depth exploration of titanium alloys, covering their composition, types, properties, applications, and future trends, with detailed parameters to help you understand their significance.
What Are Titanium Alloys?
A titanium alloy is a metallic material formed by blending titanium with elements such as aluminum, vanadium, molybdenum, or iron to enhance its mechanical and chemical properties. Pure titanium is prized for its low density (4.51 g/cm³), high corrosion resistance, and biocompatibility, but alloying it tailors these characteristics for specific uses, from jet engines to medical implants.
The alloying process involves precise control to achieve desired traits like strength, ductility, or heat resistance. Titanium typically constitutes 80-90% of the alloy, with alloying elements making up the remainder. These alloys are categorized based on their microstructure—alpha, near-alpha, alpha-beta, or beta—which dictates their performance.
Composition of Titanium Alloys
The composition of titanium alloys is carefully engineered to meet application-specific needs. Below is a breakdown of their typical components:
- Base Metal: Titanium, forming the bulk of the alloy (80-95% by weight).
- Alloying Elements:
- Aluminum (1-8%): Enhances strength and heat resistance.
- Vanadium (2-15%): Improves toughness and corrosion resistance.
- Molybdenum (0.5-15%): Boosts resistance to acidic environments.
- Iron (0.1-2%): Increases strength but may reduce corrosion resistance if excessive.
- Others: Chromium, nickel, zirconium, or tin for specialized properties like creep resistance.
- Trace Elements: Carbon (≤0.08%), oxygen (≤0.2%), or nitrogen (≤0.05%) affect hardness and ductility.
The exact composition varies by alloy grade, with standards like ASTM or AMS defining precise limits for each element.
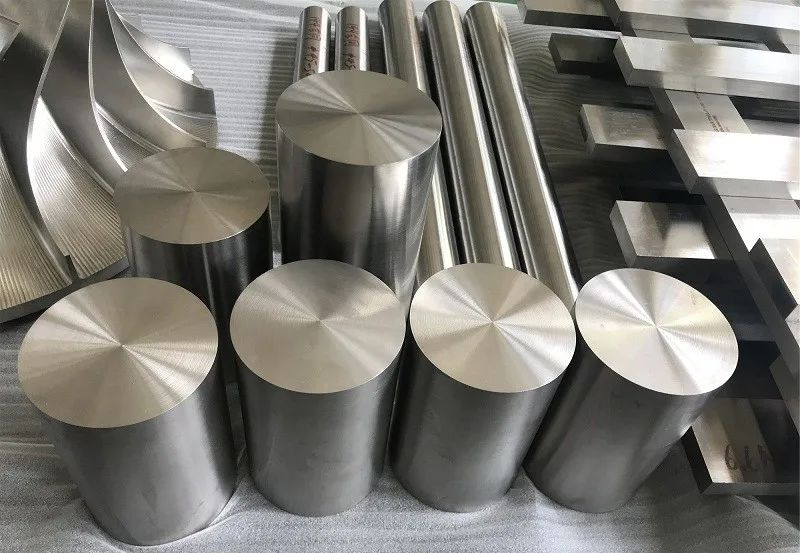
Types of Titanium Alloys
Titanium alloys are classified by their crystallographic structure, which influences their mechanical behavior. The main types are alpha, near-alpha, alpha-beta, and beta alloys, each with distinct properties and applications.
Alpha (α) Alloys
Alpha alloys contain alpha stabilizers like aluminum or oxygen, resulting in a hexagonal close-packed (HCP) crystal structure. They offer excellent corrosion resistance and weldability but have lower strength.
- Example: Ti-5Al-2.5Sn (AMS 4910).
- Properties: High-temperature stability, suitable for cryogenic environments.
- Applications: Chemical processing equipment, aircraft skins.
Alpha-Beta (α-β) Alloys
Alpha-beta alloys combine alpha stabilizers (e.g., aluminum) with beta stabilizers (e.g., vanadium), offering a balance of strength and formability. They dominate the titanium alloy market, with Ti-6Al-4V being the most common.
- Example: Ti-6Al-4V (Grade 5, AMS 4928).
- Properties: Tensile strength ~900-1000 MPa, density ~4.43 g/cm³.
- Applications: Aerospace components, medical implants.
Beta (β) Alloys
Beta alloys use beta stabilizers like molybdenum or vanadium, resulting in a body-centered cubic (BCC) structure. They provide high strength and excellent cold formability but lower creep resistance at elevated temperatures.
- Example: Ti-15V-3Cr-3Al-3Sn (AMS 4914).
- Properties: Tensile strength up to 1200 MPa, good corrosion resistance.
- Applications: Aerospace fasteners, springs.
Properties of Titanium Alloys
Titanium alloys are renowned for their unique combination of properties, making them indispensable in high-performance applications. Below is a detailed look at their key characteristics, supported by parameters.
Property | Description | Parameter |
---|---|---|
Strength-to-Weight Ratio | Stronger than steel but ~45% lighter. | Specific strength: ~200-300 kN·m/kg (vs. steel ~100-150 kN·m/kg). |
Corrosion Resistance | Forms a passive oxide layer resisting saltwater and acids. | Corrosion rate: <0.02 mm/year in seawater. |
Biocompatibility | Non-toxic, ideal for medical implants. | ISO 10993 compliant for cytotoxicity. |
High-Temperature Performance | Maintains strength up to ~600°C. | Max service temperature: 400-600°C (alloy-dependent). |
Fatigue Resistance | Withstands cyclic loading. | Fatigue limit: ~50% of tensile strength. |
These properties make titanium alloys suitable for environments where steel or aluminum may fail, such as deep-sea exploration or high-stress aerospace applications.
Applications of Titanium Alloys
The versatility of titanium alloys enables their use across diverse industries. Below are their primary applications, with examples and parameters.
Aerospace Industry
Aerospace accounts for ~70% of global titanium alloy consumption due to the need for lightweight, strong materials. Alloys like Ti-6Al-4V are used in airframes, turbine blades, and landing gear.
- Example: Boeing 787 uses ~15% titanium by weight.
- Parameters: Yield strength ~830 MPa, density ~4.43 g/cm³.
Medical Industry
Titanium alloys’ biocompatibility makes them ideal for implants, such as hip replacements and dental fixtures. Ti-6Al-4V ELI (Grade 23) is particularly common due to its low interstitial content.
- Example: Orthopedic implants.
- Parameters: Elastic modulus ~110 GPa, closer to bone (~20-30 GPa) than steel (~200 GPa).
Marine and Other Industries
In marine environments, titanium alloys resist corrosion from saltwater, making them suitable for ship hulls and offshore rigs. They also appear in automotive, consumer goods, and chemical processing.
- Marine Example: Propeller shafts (Ti-3Al-2.5V).
- Consumer Example: Titanium watches (Grade 2).
- Parameters: Corrosion rate in seawater: <0.01 mm/year.
Advantages and Limitations
While titanium alloys offer numerous benefits, they also have drawbacks that influence their adoption.
Aspect | Advantages | Limitations |
---|---|---|
Cost | Long lifespan reduces replacement costs. | High extraction cost (Kroll process): ~$10-20/kg for raw titanium. |
Machinability | Can be forged into complex shapes. | Low thermal conductivity increases tool wear. |
Availability | Recyclable without property loss. | Limited ore availability (rutile, ilmenite). |
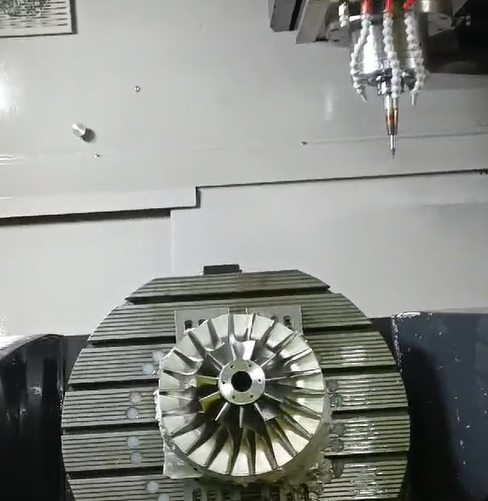
Titanium CNC Machining Service
Opt for KeSu's unparalleled engineering expertise for superior Titanium CNC components.
Beat competition with our innovative solutions with quick prototypes and production parts.
Manufacturing and Processing
Producing titanium alloys involves several steps, each critical to achieving the desired properties:
- Extraction: The Kroll process reduces titanium tetrachloride with magnesium, yielding sponge titanium.
- Alloying: Vacuum arc remelting (VAR) ensures uniform composition (e.g., Ti-6Al-4V: 6% Al, 4% V).
- Forming: Forging at 900-1100°C or rolling shapes alloys into sheets or bars.
- Heat Treatment: Annealing at 700-800°C optimizes strength (e.g., yield strength ~900 MPa for Grade 5).
- Surface Finishing Options for Titanium: Titanium parts can be finished in various ways: left as-machined with visible tool marks, polished for a smooth, reflective surface, sandblasted for a matte, textured look, or tumbled for a smoother matte finish. Electropolishing creates a bright, corrosion-resistant surface, while Alodine, though mainly for aluminum, can offer titanium corrosion protection. Anodizing produces vibrant colors and enhances corrosion resistance, ideal for medical and decorative uses. Electroless nickel plating improves wear and corrosion resistance, and painting or powder coating provides customizable, durable protection, though painting is less common due to titanium’s natural corrosion resistance. A brushed finish gives titanium a fine, linear texture for decorative appeal.
Conclusion
The titanium alloy industry is evolving to meet modern demands for sustainability and performance:
- Additive Manufacturing: 3D printing reduces waste (e.g., Ti-6Al-4V parts with ~90% material efficiency).
- Cost Reduction: Electrochemical extraction could lower costs by ~30%.
- New Alloys: High-entropy alloys with improved strength (e.g., >1200 MPa).
In conclusion, titanium alloys are a cornerstone of modern engineering, offering unmatched strength, corrosion resistance, and versatility. Despite challenges like cost, advancements in manufacturing and alloy design are expanding their potential, ensuring their relevance in future innovations.
FAQs About Titanium Alloys
What is the strongest titanium alloy?
Beta alloys like Ti-10V-2Fe-3Al can achieve tensile strengths up to 1250 MPa, making them among the strongest for aerospace applications.
Why are titanium alloys so expensive?
The Kroll process is energy-intensive, and titanium ores are less abundant than aluminum or iron, driving costs to ~$10-20/kg for raw material.
Can titanium alloys rust?
No, titanium alloys form a protective oxide layer, giving them a corrosion rate of <0.02 mm/year in seawater, far lower than steel.
Are titanium alloys safe for medical use?
Yes, alloys like Ti-6Al-4V ELI are ISO 10993-compliant, ensuring biocompatibility for implants with no adverse reactions.