Manufacturing demands precision and efficiency to remain competitive. 5-axis CNC machining overcomes limitations of three-axis systems, enabling production of high-quality, complex parts. Its flexibility and precision make it essential for industries like aerospace, automotive, medical device manufacturing, and mold making. Below are the primary advantages of 5-axis CNC machining for precision parts.

Handling Complex Geometries
5-axis CNC machining processes intricate and non-standard geometries with ease. Unlike three-axis machines, limited to linear X, Y, Z movements, 5-axis systems include two rotational axes (A and B or C). This allows the cutting tool to approach the workpiece from any angle, enabling machining of complex surfaces, undercuts, and irregular shapes in one setup.
Applications in Aerospace and Turbine Manufacturing
Aerospace and turbine industries rely on 5-axis machining for components like turbine blades, impellers, and aerodynamic parts. These feature intricate curves, contoured surfaces, and tight tolerances (±0.005 mm or better) that three-axis machines struggle to achieve without multiple setups. A turbine blade may require machining on five surfaces with precise curvature. 5-axis machining completes this in one setup, ensuring dimensional accuracy and consistency.
Specifications for high-end 5-axis machines, such as the DMG MORI DMU 50, include positional accuracy of ±0.002 mm and spindle speeds up to 18,000 RPM, ideal for such applications. These machines handle materials like Inconel or titanium, common in aerospace, with minimal tool wear.
Reducing Setup Time and Errors
Multiple setups in three-axis machining introduce misalignment risks, compromising accuracy. 5-axis machining uses a single fixture, minimizing repositioning errors. A mold cavity requiring multiple angles can be machined relative to one datum, achieving tolerances as tight as ±0.003 mm. This reduces setup time by up to 50% compared to three-axis systems, as seen in case studies from mold-making firms using Haas UMC-750 machines.
Single-setup machining enhances repeatability, critical for batch production of precision parts like medical implants or automotive dies.
Streamlining Workflow
By consolidating operations, 5-axis machining simplifies workflows. A complex part, such as an aerospace structural component, may require milling, drilling, and contouring. 5-axis machines perform these in one cycle, reducing handling and fixturing needs. This cuts labor costs and shortens lead times, with some manufacturers reporting 30-40% reductions in total machining time.

Enhancing Precision and Surface Quality
5-axis CNC machining delivers tighter tolerances and superior surface finishes. Simultaneous multi-axis movement ensures smoother cutting paths, minimizing vibrations and tool deflections. This is vital for components requiring exceptional accuracy, such as medical implants or high-performance engine parts.
Optimized Tool Paths
Dynamic tool orientation in 5-axis machining maintains perpendicularity to complex surfaces, reducing scalloping and ensuring finishes as fine as Ra 0.2 µm. For medical implants, where surface roughness must be below Ra 0.4 µm for biocompatibility, this is critical. Machines like the Mazak INTEGREX i-400 achieve angular accuracies of ±0.01 degrees, supporting such precision.
Tool path optimization reduces machining errors. When machining a parabolic reflector, 5-axis systems maintain consistent chip loads, avoiding deviations that three-axis systems encounter due to limited axis control.
Minimizing Post-Processing
Superior surface quality from 5-axis machining reduces post-processing needs. Automotive engine components achieve mirror-like finishes (Ra 0.1-0.3 µm) directly from the machine, eliminating polishing. This saves 10-20% in production costs, as secondary operations like grinding are minimized. Data from Okuma’s MU-5000V shows surface finish improvements of 25% over three-axis systems.
Consistency Across Batches
5-axis machining ensures uniformity in high-volume production. By maintaining consistent cutting conditions, it produces identical parts across batches. This is essential for industries like electronics, where connectors require tolerances of ±0.01 mm. Advanced CAM software, such as Siemens NX, enhances this by generating precise 5-axis tool paths.
Reducing Production Time
5-axis CNC machining shortens production cycles by enabling multi-sided machining in one setup, eliminating repetitive repositioning. This accelerates production and increases throughput, critical for industries with tight deadlines.
Single-Setup Efficiency
A mold or die requiring multiple setups on a three-axis machine can be completed in one 5-axis cycle. An automotive die with undercuts and angled features takes 60% less time on a 5-axis machine like the Hermle C 42 U, which supports simultaneous 5-axis milling at 15,000 RPM. This efficiency is vital for automotive and consumer electronics sectors.
Minimizing Downtime
Reduced setups decrease machine downtime. Three-axis systems may require 2-3 hours for re-fixturing complex parts, while 5-axis machines complete the same task in under 30 minutes. This boosts machine utilization rates, with some shops reporting 20% higher output after adopting 5-axis technology.
Scalability for Large Projects
5-axis machining scales efficiently for large projects. Aerospace manufacturers producing structural components benefit from batch processing with minimal setup changes. Machines like the FANUC Robodrill D21LiB5 offer cycle time reductions of 15-25%, enabling scalability without sacrificing quality.
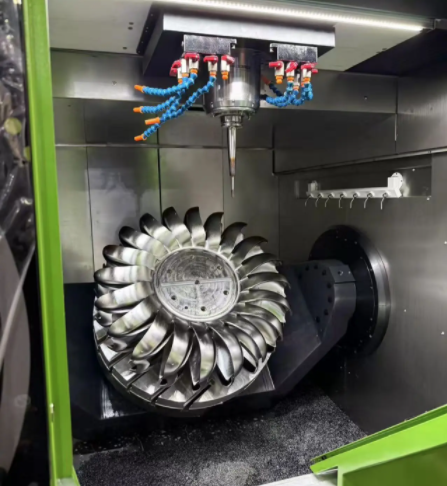
Extending Tool Life and Cost Savings
5-axis CNC machining optimizes cutting by maintaining ideal tool angles, reducing stress and wear. Shorter tools with less overhang enhance rigidity, minimizing vibration and improving performance.
Optimized Cutting Conditions
Maintaining optimal cutting angles reduces tool wear by 20-30%, as reported by Sandvik Coromant studies. When machining titanium, 5-axis machines adjust tool paths to minimize heat buildup, extending tool life by up to 50%. This is critical for high-cost tools like carbide end mills.
Lower Maintenance Costs
Reduced tool wear lowers replacement and maintenance costs. A single carbide tool for titanium machining can cost $100-$300. Extending tool life by 30% saves thousands annually for high-volume shops. Fewer setups reduce labor costs, with some manufacturers reporting 15% savings.
Energy Efficiency
5-axis machines consume less energy per part due to shorter cycle times. A study by GF Machining Solutions found that 5-axis systems use 10-15% less power than three-axis machines for complex parts, contributing to cost savings and sustainability.
Machining Difficult Materials
Modern manufacturing involves materials like titanium alloys, stainless steel, and composites, known for high strength and toughness. 5-axis CNC machining excels in processing these materials with precision and control.
Precision in Tough Materials
Titanium alloys (e.g., Ti-6Al-4V) require low cutting speeds (50-80 m/min) and high torque. 5-axis machines like the Makino T1 maintain consistent chip loads, achieving surface finishes of Ra 0.5 µm. This is critical for aerospace components like landing gear parts.
Handling Composites
Composites, such as carbon fiber-reinforced polymers (CFRP), are prone to delamination. 5-axis machining uses specialized tool paths to minimize fiber pullout, achieving clean edges. Machines like the CMS Ares offer spindle speeds up to 24,000 RPM, ideal for CFRP machining.
Versatility Across Industries
From medical devices (stainless steel implants) to energy sector parts (Inconel turbine blades), 5-axis machining adapts to diverse materials. Its ability to handle high-hardness materials (up to 60 HRC) makes it indispensable for high-end applications.

Precision 5-Axis CNC Machining with Kesu Hardware
At Kesu Hardware Group, our state-of-the-art AFM 5-axis and Mikron 5-axis CNC machining centers deliver unparalleled precision and versatility for industries demanding complex, high-quality components.
With Kesu’s advanced equipment, including the Mikron E 700U and large-stroke GMU-800EVO (platform size 800mm, X/Y/Z stroke: 850/950/550 mm), we provide one-stop solutions for non-standard, high-precision parts with no MOQ, meeting the rigorous demands of automotive, medical, aerospace, and electronics industries. Upload your 2D/3D drawings today to get an instant quote and experience Kesu's commitment to quality and efficiency.
Conclusion
Five-axis CNC machining represents a significant leap forward in precision manufacturing, offering unparalleled advantages over traditional three-axis systems. Its ability to handle complex geometries, enhance precision, reduce production times, extend tool life, and machine difficult materials makes it an essential technology for producing high-quality precision parts. For industries that demand accuracy, efficiency, and versatility, 5-axis machining is not just a tool—it’s a competitive advantage that drives innovation and excellence.
By investing in 5-axis CNC machining, manufacturers can overcome the limitations of conventional methods, streamline their operations, and deliver superior products that meet the rigorous demands of today’s markets. Whether you’re crafting aerospace components, intricate molds, or high-performance automotive parts, the benefits of 5-axis machining ensure that precision and efficiency go hand in hand.
FAQ: 5-Axis CNC Machining for Precision Parts
What is 5-axis CNC machining?
5-axis CNC machining uses a machine with five axes of movement (X, Y, Z, and two rotational axes, typically A and B or C) to process complex parts in one setup, offering greater flexibility and precision than three-axis systems.
How does 5-axis machining improve precision?
It enables smoother tool paths, maintains optimal tool angles, and reduces vibrations, achieving tolerances as tight as ±0.002 mm and surface finishes below Ra 0.4 µm.
Which industries benefit most from 5-axis machining?
Aerospace, automotive, medical, and mold-making industries benefit due to the need for complex geometries, tight tolerances, and challenging materials like titanium and composites.
Is 5-axis machining cost-effective?
Yes, it reduces setup times, extends tool life, and minimizes post-processing, leading to 15-30% cost savings in high-precision applications.