Wheel hubs are critical components in automotive and industrial systems, serving as the central connection point between a vehicle's axle and wheel. They ensure smooth wheel rotation, support vehicle loads, and integrate with braking and suspension systems. This content explores the design principles, functional mechanics, and diverse applications of wheel hubs, emphasizing technical specifications and engineering considerations.
Design of Wheel Hubs
The design of a wheel hub is a complex process that balances structural integrity, weight, and compatibility with other vehicle systems. Engineers prioritize durability, precision, and performance under varying loads and conditions.
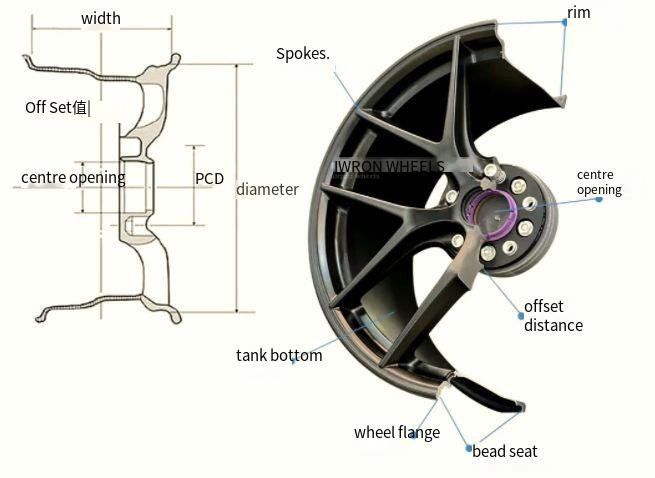
Components of a Wheel Hub
A wheel hub machining assembly typically includes the hub body, bearings, studs or bolts, and seals. Each component is engineered to withstand specific forces while maintaining alignment and functionality.
- Hub Body: The central structure, usually made of cast iron, steel, or aluminum, houses the bearings and connects to the wheel and axle.
- Bearings: Tapered roller or ball bearings reduce friction and support radial and axial loads. Common bearing sizes range from 20 mm to 80 mm in inner diameter, depending on the vehicle type.
- Studs or Bolts: These secure the wheel to the hub, typically M12 or M14 in diameter with a tensile strength of 10.9 or higher per ISO standards.
- Seals: Protect bearings from contaminants like water and dirt, often made of nitrile rubber or silicone, with a typical lifespan of 100,000 to 150,000 miles under normal conditions.
Material Selection
Material choice impacts weight, strength, and cost. Common materials include:
Material | Density (g/cm³) | Tensile Strength (MPa) | Applications |
---|---|---|---|
Cast Iron | 7.2–7.8 | 200–400 | Heavy-duty vehicles, trucks |
Steel | 7.8–8.0 | 400–800 | Passenger cars, commercial vehicles |
Aluminum | 2.7 | 200–300 | Performance vehicles, lightweight applications |
Aluminum is favored in high-performance vehicles for its low density, while cast iron is used in heavy-duty applications for its durability.
Design Parameters
Key design parameters include load capacity, bolt circle diameter (BCD), and hub offset. Load capacity is calculated based on the gross vehicle weight rating (GVWR), typically ranging from 1,000 kg to 10,000 kg for passenger cars to heavy trucks. BCD, such as 4x100 mm or 5x114.3 mm, ensures compatibility with wheels. Hub offset, measured in millimeters, affects vehicle handling and stability, with positive offsets (10–50 mm) common in front-wheel-drive vehicles and negative offsets (-10 to -40 mm) in off-road vehicles.
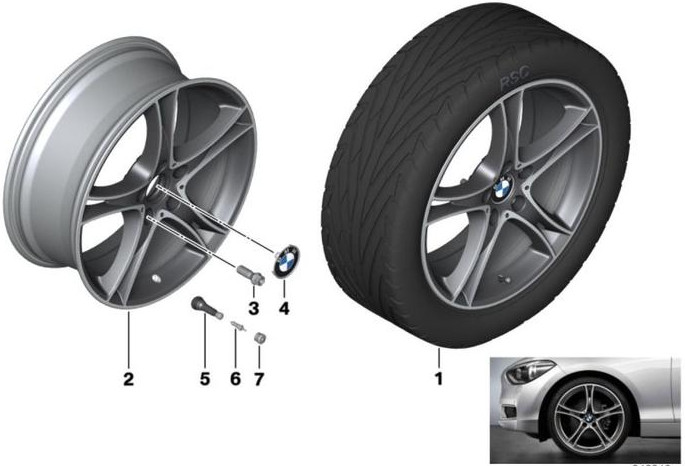
Function of Wheel Hubs
Wheel hubs perform multiple functions critical to vehicle operation, including load bearing, wheel rotation, and integration with braking and suspension systems.
Load Bearing and Support
Wheel hubs transfer the vehicle’s weight and dynamic loads to the wheels. They must withstand static loads (vehicle weight) and dynamic loads (cornering, braking, and road impacts). For example, a midsize sedan with a GVWR of 2,000 kg requires hubs capable of supporting approximately 500 kg per wheel, factoring in load distribution.
Wheel Rotation and Friction Reduction
Bearings within the hub enable smooth wheel rotation by minimizing friction. Tapered roller bearings, with a typical coefficient of friction of 0.001–0.002, are preferred for heavy loads, while ball bearings, with slightly higher friction (0.0015–0.0025), are used in lighter applications. Proper lubrication, often with synthetic grease rated for -40°C to 150°C, extends bearing life.
Integration with Braking Systems
Wheel hubs often house brake rotors or drums, ensuring precise alignment for effective braking. For disc brake systems, the hub’s mounting surface must maintain flatness within 0.05 mm to prevent vibration. Anti-lock braking system (ABS) sensors, often embedded in the hub, monitor wheel speed with a typical resolution of 40–100 pulses per rotation.
Suspension Compatibility
Hubs connect to suspension components like control arms and struts, maintaining wheel alignment. Camber, caster, and toe angles, typically within ±1° of manufacturer specifications, are influenced by hub design to ensure stable handling.
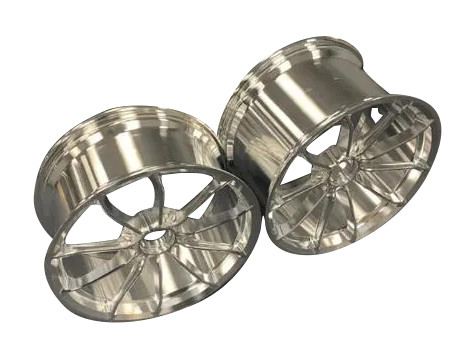
Applications of Wheel Hubs
Wheel hubs are used across various industries, with designs tailored to specific requirements. Applications range from automotive to industrial and specialized vehicles.
Passenger Vehicles
In passenger cars, wheel hubs prioritize weight reduction and fuel efficiency. A typical compact car hub weighs 3–5 kg, with aluminum alloys reducing weight by 20–30% compared to steel. These hubs often integrate ABS sensors and are designed for bolt patterns like 4x100 mm or 5x112 mm.
Commercial and Heavy-Duty Vehicles
Trucks and buses require robust hubs to handle loads up to 20,000 kg per axle. These hubs use larger bearings (50–100 mm inner diameter) and thicker studs (M18–M22) to withstand high torque and stress. Cast iron or high-strength steel is common to ensure durability.
Performance and Racing Vehicles
Racing hubs prioritize lightweight materials and precision. Forged aluminum hubs, weighing 1–2 kg, reduce unsprung mass, improving acceleration and handling. These hubs often feature custom BCDs (e.g., 5x120 mm) and low-friction ceramic bearings with a coefficient of friction as low as 0.0008.
Industrial and Off-Road Applications
Wheel hubs in construction equipment, agricultural machinery, and off-road vehicles are designed for extreme conditions. They use sealed bearings to resist dust and moisture, with load capacities up to 15,000 kg per hub. Hub designs accommodate large tire sizes (20–50 inches in diameter) and rugged terrains.
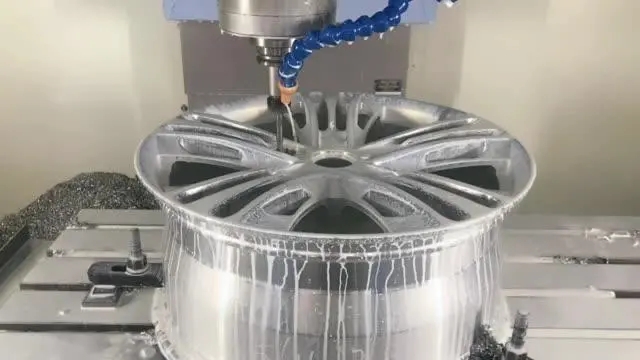
Engineering Considerations
Several factors influence wheel hub performance and longevity, requiring careful engineering and maintenance.
Durability and Fatigue Resistance
Hubs must resist fatigue from cyclic loading. Finite element analysis (FEA) is used to simulate stress, with maximum stress typically kept below 60% of the material’s yield strength (e.g., 240 MPa for steel hubs). Heat treatment processes, such as quenching and tempering, enhance fatigue life.
Thermal Management
Braking generates significant heat, often exceeding 300°C in heavy braking scenarios. Hubs must dissipate heat effectively to prevent bearing failure. Aluminum hubs offer better thermal conductivity (200 W/m·K) than cast iron (50 W/m·K), but cooling fins or ventilation channels may be added for high-performance applications.
Maintenance and Replacement
Wheel hubs require periodic inspection for wear, particularly in bearings and seals. Common issues include bearing noise (indicating wear or lack of lubrication) and seal degradation, leading to contamination. Replacement intervals vary by application, with passenger car hubs lasting 100,000–150,000 miles and heavy-duty hubs requiring service every 50,000–80,000 miles.
Compatibility and Standardization
Hubs must align with industry standards, such as ISO 7646 for bolt patterns and SAE J694 for lug nut specifications. Interchangeability is critical in aftermarket applications, where hubs must match OEM specifications for BCD, offset, and bearing size.
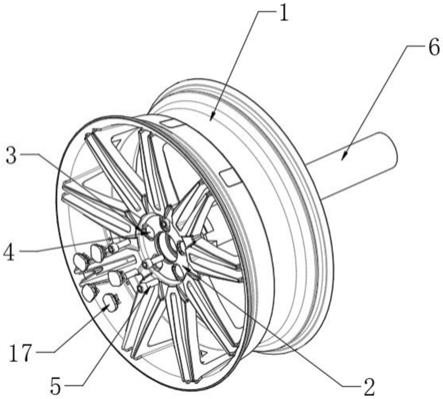
Performance Specifications
Wheel hub performance is defined by measurable parameters that ensure reliability and efficiency across applications.
Parameter | Typical Range | Application |
---|---|---|
Load Capacity | 500–15,000 kg | Passenger cars to heavy trucks |
Bearing Life (L10) | 100,000–1,000,000 miles | Dependent on load and maintenance |
Hub Weight | 1–10 kg | Racing to heavy-duty vehicles |
Operating Temperature | -40°C to 150°C | Standard conditions |
These specifications are tailored to vehicle type, ensuring optimal performance and safety.
Conclusion
Wheel hubs are integral to vehicle performance, combining advanced engineering with practical functionality. Their design, driven by material selection, load requirements, and system integration, ensures reliability across diverse applications. By understanding their components, functions, and specifications, engineers and technicians can optimize vehicle performance and longevity.
Wheel Hubs FAQ (Frequently Asked Questions)
What is a wheel hub?
A wheel hub is a critical component in a vehicle's wheel assembly that connects the wheel to the car's chassis. It houses the wheel bearings, which allow the wheel to rotate smoothly while supporting the vehicle's weight. In modern vehicles, wheel hubs often integrate with other parts like the brake rotor mounting surface and, in some cases, the ABS sensor ring.
What are the signs of a failing wheel hub?
Common symptoms of a faulty wheel hub include:
Unusual noises: A grinding, humming, or rumbling sound that gets louder as you accelerate (often more noticeable at highway speeds).
Vibration: Steering wheel or vehicle vibration, especially during acceleration or when turning.
ABS issues: Illumination of the ABS warning light on the dashboard, caused by a malfunctioning integrated ABS sensor.
Wheel looseness: Excessive play in the wheel when jacked up (check by gently wiggling the wheel back and forth).
Uneven brake wear: If the hub affects brake rotor alignment, it may cause uneven pad or rotor wear.
How long do wheel hubs typically last?
Wheel hubs are designed to be durable, with a lifespan ranging from 80,000 to 150,000 miles (130,000 to 240,000 km) under normal driving conditions. Factors that can shorten their life include:
Rough roads (potholes, gravel)
Heavy loads or towing
Poor wheel alignment
Water, dirt, or debris entering the hub assembly (common in off-road vehicles)
Can a wheel hub be repaired, or does it need to be replaced?
In most cases, wheel hubs are replaced rather than repaired. This is because they are pre-assembled with bearings, seals, and (often) ABS components, which are not designed to be disassembled or serviced individually. Attempting to repair a hub (e.g., repacking bearings in older, non-sealed designs) may compromise safety and lead to premature failure. Modern sealed hubs are engineered as a single, replaceable unit.
What’s the difference between a front and rear wheel hub?
The main differences depend on the vehicle’s drivetrain:
Front hubs (FWD or AWD): Often integrate with CV joints or axle shafts to transfer power to the wheels, in addition to supporting the wheel. They may have more complex internal components.
Rear hubs (RWD or FWD): In FWD vehicles, rear hubs are typically simpler, as they only support the wheel (no power transfer). In RWD or AWD vehicles, rear hubs may connect to axle shafts for power transfer.
Both front and rear hubs can include ABS sensors, but front hubs are more likely to have them in vehicles with 4-wheel ABS.
Are all wheel hubs the same, or do they vary by vehicle?
Wheel hubs are vehicle-specific. They vary in size, bolt pattern, bearing type, and integration with other components (e.g., ABS sensors, axle shafts). Always use a hub designed for your vehicle’s make, model, year, and drivetrain to ensure proper fit and safety. Aftermarket hubs are available but should meet OEM specifications.