Efficient CNC (Computer Numerical Control) factories are designed to deliver precision parts with speed and reliability, even under the pressure of urgent orders. Handling urgent orders requires a combination of rapid response mechanisms, flexible production strategies, robust communication, and rigorous quality control. This article provides a detailed, technical, and systematic explanation of how CNC factories manage urgent orders effectively, based on established industry practices. The focus is on practical, experience-based methods that ensure timely delivery without compromising quality.
Analyzing Urgent Order Requirements
When an urgent order is received, the first step is a thorough analysis of the requirements. This involves understanding the technical specifications, including part complexity, material type, quantity, tolerances, and delivery deadlines. Factories assess the feasibility of meeting the deadline based on available resources, such as machine capacity, workforce availability, and material stock.
The analysis includes evaluating the part’s design through computer-aided design (CAD) files and determining the machining processes required, such as milling, turning, or drilling. For example, a complex part with tight tolerances of ±0.005 mm may require 5-axis CNC machines, while simpler parts may be processed on 3-axis machines. The factory also reviews the client’s quality requirements, such as surface finish (e.g., Ra 1.6 μm to 3.2 μm) or specific certifications like ISO 9001 compliance.
Material availability is critical. Factories maintain an inventory of common materials like aluminum 6061, stainless steel 304, and engineering plastics like PEEK to avoid delays. If a specialized material like titanium Ti6Al4V is required, the procurement team confirms lead times with suppliers immediately. This initial assessment ensures the factory can allocate resources efficiently and identify potential bottlenecks early.
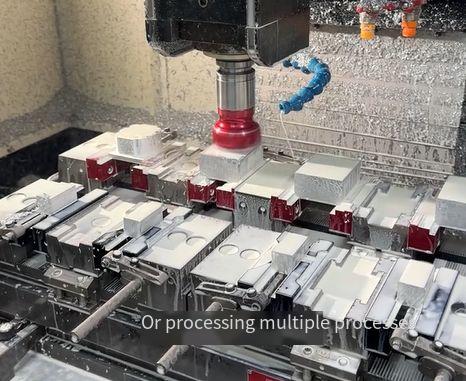
Establishing a Rapid Response Mechanism
A rapid response mechanism is essential for prioritizing urgent orders. This involves restructuring production schedules to accommodate the new order without disrupting existing commitments. Factories use advanced production management software to adjust schedules dynamically, ensuring urgent tasks are prioritized.
For example, enterprise resource planning (ERP) systems like SAP or MachineMetrics allow real-time monitoring of machine availability and operator schedules. When an urgent order is confirmed, the production team resequences jobs, placing the urgent order at the forefront. This may involve pausing non-critical jobs or reallocating machines. For instance, a 5-axis CNC mill with a spindle speed of 20,000 RPM may be reassigned to produce a complex aerospace component with a 48-hour deadline.
Factories also maintain a dedicated rapid response team, consisting of skilled machinists, programmers, and quality inspectors, to handle urgent orders. This team is trained to set up machines quickly, reducing setup times from hours to minutes. For example, using standardized workholding fixtures and pre-calibrated tools can cut setup time by up to 50%. The rapid response mechanism ensures that urgent orders are processed immediately, minimizing delays.
Implementing Flexible Production Strategies
Flexible production strategies enable CNC factories to scale capacity and meet tight deadlines. These strategies include overtime production, outsourcing, and activating backup equipment. Each approach is carefully coordinated to maintain efficiency and quality.
Overtime Production: When demand exceeds regular capacity, factories schedule overtime shifts. For instance, extending machine operation from 8 hours to 12 hours per day can increase output by 50%. Operators are trained to maintain precision during extended hours, and machines are monitored to prevent wear, ensuring consistent performance.
Outsourcing: For high-volume urgent orders, factories may outsource non-critical tasks to trusted partners. For example, a factory might outsource rough machining to a partner with available capacity, while retaining final finishing in-house to ensure quality. Outsourcing partners are vetted for compliance with standards like ISO 9001 to maintain consistency.
Backup Equipment: Efficient factories maintain backup CNC machines to mitigate risks like equipment failure. For instance, a secondary 3-axis mill with a table size of 1000 x 500 mm can be activated if the primary machine encounters issues. Regular maintenance schedules ensure backup machines are production-ready.
The following table summarizes the flexible production strategies and their applications:
Strategy | Description | Application |
---|---|---|
Overtime Production | Extending work hours to increase output | Small to medium urgent orders with tight deadlines |
Outsourcing | Delegating tasks to external partners | High-volume orders exceeding in-house capacity |
Backup Equipment | Activating reserve machines | Equipment failure or unexpected demand spikes |
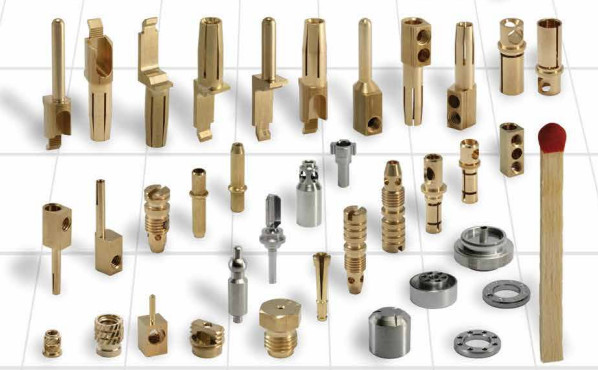
Strengthening Communication and Collaboration
Effective communication is critical for coordinating urgent orders across departments. Production, procurement, quality control, and logistics teams must work in sync to ensure seamless execution. Factories use digital tools like Slack or Microsoft Teams for real-time communication, allowing instant updates on production progress, material shortages, or quality issues.
Internally, daily stand-up meetings are held to align teams on urgent order priorities. For example, the production team may report that a CNC lathe is set up for a 500-unit order of stainless steel shafts, while the logistics team confirms delivery timelines. Externally, factories maintain close contact with clients, providing updates on milestones, such as completion of rough machining or final inspection. This transparency builds trust and ensures alignment with client expectations.
Collaboration extends to suppliers. For urgent orders requiring specialized materials, procurement teams negotiate expedited shipping, often within 24-48 hours. For instance, a factory may request same-day delivery of brass C360 for a prototype order. Clear communication channels ensure all stakeholders are informed, reducing the risk of delays.
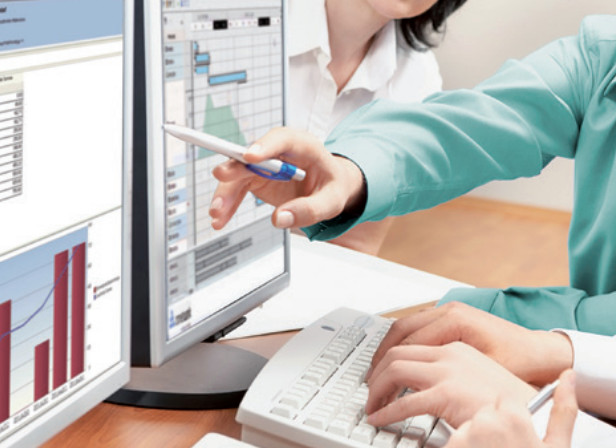
Optimizing Production Processes
Optimizing production processes is key to handling urgent orders efficiently. Factories refine machining parameters, such as cutting speed and feed rate, to maximize throughput without sacrificing quality. For example, optimizing the feed rate to 0.1 mm/rev for aluminum machining can reduce cycle time by 20% while maintaining a surface finish of Ra 1.6 μm.
Standardized processes also enhance efficiency. Factories use pre-programmed G-code templates for common parts, reducing programming time. For instance, a template for drilling holes in steel plates can be reused across multiple orders, saving 10-15 minutes per setup. Additionally, factories employ advanced CAM software to simulate machining paths, identifying potential collisions or inefficiencies before production begins.
Employee training is another critical factor. Operators are trained to handle multi-axis machines and troubleshoot issues quickly. For example, a skilled machinist can adjust tool offsets in under 5 minutes, minimizing downtime. Regular training ensures employees stay updated on the latest CNC technologies, such as 5-axis machining or high-speed spindles.
Ensuring Quality Control
Quality control is non-negotiable, even for urgent orders. Factories implement stringent inspection protocols to ensure parts meet specifications. For example, coordinate measuring machines (CMMs) are used to verify tolerances down to ±0.01 mm. First Article Inspection (FAI) is conducted for critical orders, ensuring the initial part meets all requirements before full production begins.
In-process inspections are performed at key stages, such as after rough machining and before final finishing. For instance, a part requiring a tolerance of ±0.02 mm is checked using digital calipers or laser scanners. Non-destructive testing, like ultrasonic inspection, is used for high-reliability components in industries like aerospace.
The following table outlines common quality control measures for urgent orders:
Measure | Description | Application |
---|---|---|
First Article Inspection (FAI) | Verifying the first part against specifications | Critical orders requiring high precision |
In-Process Inspection | Checking parts during machining stages | Ensuring consistency across batches |
Non-Destructive Testing | Testing for internal defects without damage | Aerospace and medical components |
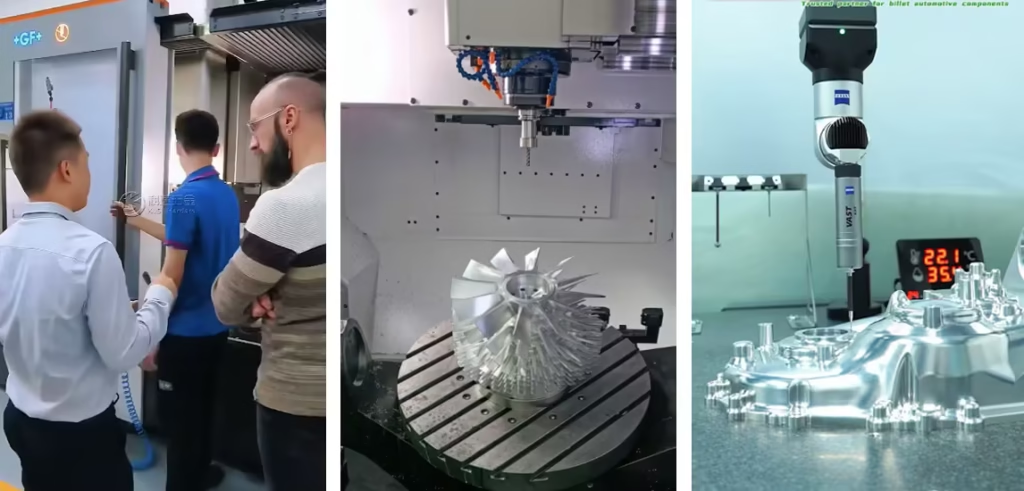
Managing Risks
Risk management is integral to handling urgent orders. Factories identify potential risks, such as machine downtime, material shortages, or operator errors, and develop mitigation strategies. For example, maintaining a spare parts inventory for critical machine components, like spindles or toolholders, reduces downtime from equipment failure.
Redundant supply chains are another risk mitigation strategy. Factories collaborate with multiple suppliers to ensure material availability. For instance, if a primary supplier cannot deliver aluminum 7075 within 24 hours, a secondary supplier is contacted. Additionally, cross-training operators on multiple machines ensures flexibility in case of staffing shortages.
Risk assessments are conducted before accepting urgent orders. For example, a factory may evaluate the likelihood of meeting a 24-hour deadline for a 1000-unit order of plastic components. If risks are deemed high, the factory communicates transparently with the client to set realistic expectations.
Conclusion
Efficient CNC factories handle urgent orders through a systematic approach that combines rapid response mechanisms, flexible production strategies, optimized processes, robust communication, stringent quality control, and proactive risk management. By analyzing order requirements, prioritizing tasks, and leveraging advanced technologies, factories meet tight deadlines while maintaining precision and quality. These practices, rooted in experience and technical expertise, ensure CNC factories remain reliable partners for clients with urgent manufacturing needs.