CNC (Computer Numerical Control) machining is a cornerstone of modern manufacturing, enabling the production of highly precise, customized parts for industries such as aerospace, automotive, medical, and electronics. CNC service providers play a critical role in meeting the demand for tailored components by leveraging advanced machinery, skilled expertise, and robust quality control systems. This article provides a detailed, technical overview of how these providers deliver customized solutions, focusing on processes, materials, tolerances, and quality assurance to ensure reliability and performance.
Understanding CNC Machining for Customization
CNC machining is a subtractive manufacturing process that uses computer-controlled tools to remove material from a workpiece, shaping it into a precise component based on a digital design. Unlike traditional manufacturing methods, CNC machining offers unmatched flexibility, allowing service providers to produce parts with complex geometries, tight tolerances, and specific material requirements. The process begins with a CAD (Computer-Aided Design) file, which is converted into a CNC program using CAM (Computer-Aided Manufacturing) software. This program directs the machine’s movements across multiple axes (typically 3 to 5) to achieve the desired shape.
Key to customization is the ability to adapt to unique specifications. CNC service providers cater to diverse industries, producing everything from single prototypes to high-volume production runs. They achieve this through a combination of advanced equipment, material versatility, and skilled engineering, ensuring each part meets exact client requirements.
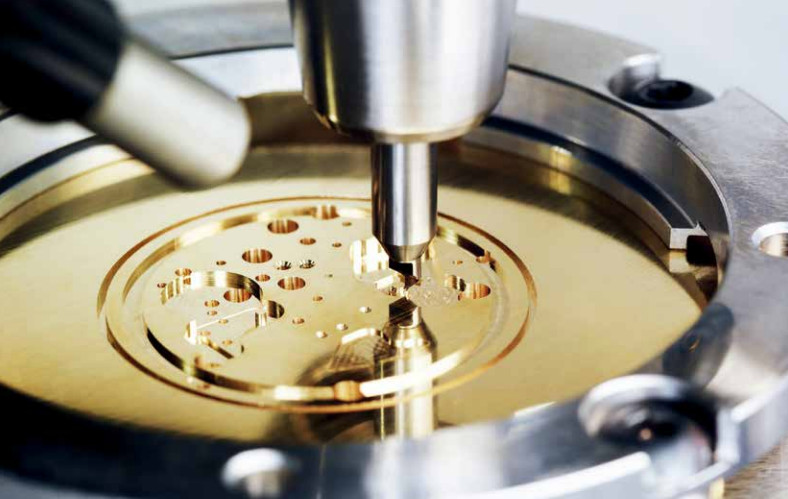
Key Capabilities of CNC Service Providers
CNC service providers offer a range of capabilities to meet customized part demands. These include various machining processes, material options, and finishing techniques, all tailored to specific applications.
CNC Machining Processes
CNC machining encompasses several processes, each suited to different part geometries and requirements. The primary methods include:
- CNC Milling: Uses rotating multi-point cutting tools to remove material from a workpiece. 3-axis mills handle simpler parts, while 5-axis mills enable complex geometries by allowing simultaneous movement in multiple directions.
- CNC Turning: Involves rotating the workpiece while a single-point cutting tool shapes it, ideal for cylindrical components like shafts or bushings.
- Electrical Discharge Machining (EDM): Uses electrical sparks to erode material, suitable for intricate shapes in hard metals like titanium or Inconel.
- Surface Grinding: Achieves smooth, flat surfaces for parts requiring high precision, such as tooling or molds.
Providers often combine these processes within a single project to achieve complex designs, ensuring flexibility for customized needs.
Material Versatility
CNC service providers work with a wide range of materials to meet specific functional and aesthetic requirements. Common materials include:
Material Type | Examples | Applications | Key Properties |
---|---|---|---|
Metals | Aluminum, Stainless Steel, Brass, Titanium | Aerospace components, automotive parts, medical implants | High strength, corrosion resistance, thermal conductivity |
Plastics | ABS, PEEK, Nylon, Acetal | Consumer electronics, medical devices, prototypes | Lightweight, chemical resistance, flexibility |
Composites | Carbon Fiber, Fiberglass | Aerospace structures, automotive panels | High strength-to-weight ratio, durability |
Material selection is guided by the part’s intended application, such as weight reduction for aerospace or biocompatibility for medical devices. Providers often offer material certifications to ensure compliance with industry standards.
Surface Finishing Options
Surface finishes enhance both the functionality and appearance of CNC-machined parts. Providers offer a variety of finishing options, including:
- As-Machined: Leaves tool marks, cost-effective for non-aesthetic parts.
- Anodizing: Increases corrosion resistance and allows color dyeing, commonly used for aluminum parts.
- Polishing: Achieves a high-gloss finish for aesthetic appeal or reduced surface roughness.
- Powder Coating: Applies a durable, wear-resistant layer with customizable colors.
- Electroplating: Bonds a thin metal layer to improve wear resistance and conductivity.
Finishing is selected based on functional requirements, such as corrosion resistance for marine applications or aesthetic needs for consumer products.
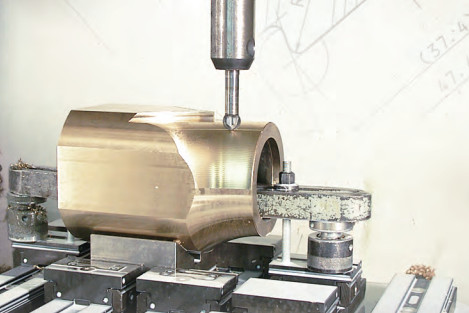
Precision and Tolerance Standards
Precision is a hallmark of CNC machining, enabling providers to meet tight tolerances critical for customized parts. Standard tolerances typically range from ±0.1 mm to ±0.01 mm, with advanced setups achieving tolerances as tight as ±0.005 mm for high-precision industries like aerospace or medical.
Tolerance requirements depend on the part’s application. For example:
- Aerospace components may require tolerances of ±0.01 mm to ensure perfect fit in assemblies.
- Medical implants demand tolerances of ±0.005 mm for biocompatibility and performance.
- Consumer electronics often use ±0.05 mm for less critical features.
Providers achieve these tolerances through advanced CNC machines, such as 5-axis mills, and rigorous inspection processes using tools like Coordinate Measuring Machines (CMM) and profilometers. Detailed 2D drawings with annotated tolerances are often required to ensure accuracy.
Quality Assurance and Inspection Processes
Quality assurance is integral to delivering customized parts that meet client specifications. CNC service providers implement comprehensive quality control systems, including:
- First Article Inspection (FAI): Verifies that the initial sample meets design specifications before full production begins.
- In-Process Inspection: Monitors machining at various stages to catch deviations early.
- Final Inspection: Uses advanced metrology tools to ensure dimensional accuracy and surface quality.
Many providers adhere to standards like ISO 9001:2015 for quality management and AS9100 for aerospace-specific requirements. Certifications such as RoHS compliance ensure environmentally friendly manufacturing. Inspection reports, material certifications, and Certificates of Conformance (CoC) are often provided to validate quality.
Customization Through Design Optimization
Design optimization is a critical step in meeting customized part demands. CNC service providers collaborate with clients to refine CAD designs for manufacturability, reducing costs and improving efficiency. Key considerations include:
- Wall Thickness: Minimum wall thickness of 0.8 mm for metals and 1.5 mm for plastics to prevent vibration or deformation.
- Thread Length: Recommended not to exceed three times the hole diameter to avoid special tooling costs.
- Internal Corners: Require radius features due to the cylindrical nature of cutting tools, avoiding sharp corners to reduce machining time.
- Deep Cavities: Limited to 2-3 times the tool diameter (e.g., a 12 mm cutter can machine a 25 mm deep cavity) to maintain efficiency.
Providers often use automated design analysis tools to identify potential issues, such as thin walls or unthreadable holes, before production begins. This ensures parts are both functional and cost-effective.
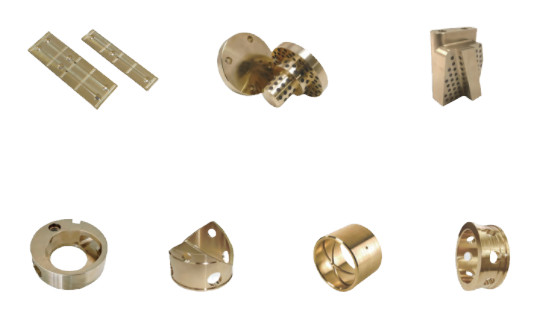
Scalability and Lead Times
CNC service providers offer scalable solutions, accommodating both low-volume prototypes and high-volume production runs (1 to 100,000 parts). Lead times vary based on complexity, material, and quantity:
Production Type | Typical Lead Time | Applications |
---|---|---|
Rapid Prototyping | 1-5 days | Design validation, functional testing |
Low-Volume Production | 5-10 days | Custom components, niche markets |
High-Volume Production | 10-30 days | Mass production for automotive, aerospace |
Advanced providers leverage automated production lines and networked manufacturing facilities to minimize lead times while maintaining quality. For urgent needs, expedited options can deliver parts in as little as one day.
Industry Applications and Expertise
CNC service providers serve a wide range of industries, each with unique requirements:
- Aerospace: Produces lightweight, high-strength components with tight tolerances for aircraft and satellites.
- Automotive: Manufactures precision parts like engine components and custom car parts.
- Medical: Creates biocompatible implants and diagnostic equipment with stringent quality standards.
- Electronics: Fabricates small, intricate parts for consumer devices with high repeatability.
Providers often employ engineers with industry-specific expertise to ensure compliance with standards like ISO 13485 for medical devices or IATF 16949 for automotive parts.
Partnering with CNC Service Providers
Selecting the right CNC service provider is critical for successful customization. Key factors to consider include:
- Equipment Capabilities: Ensure the provider has advanced machines like 5-axis mills or EDM for complex parts.
- Material Expertise: Verify the ability to work with specific materials required for your application.
- Quality Certifications: Look for ISO 9001, AS9100, or other relevant certifications.
- Customer Support: Choose providers with responsive communication and technical support for design optimization.
Online platforms streamline the process by offering instant quotes, design feedback, and order tracking, enhancing efficiency and transparency.
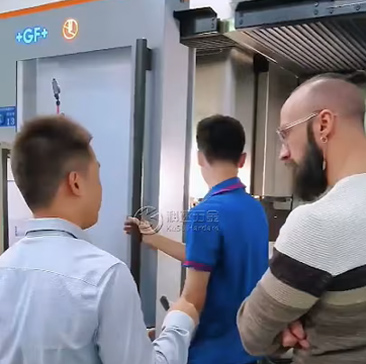
Unleash the Power of Precision Customization with Kesu's CNC Solutions
When it comes to transforming complex designs into high-precision components, Kesu stands as your trusted partner in CNC machining. Our advanced 5-axis mills, EDM capabilities, and a vast material library—ranging from aerospace-grade titanium to biocompatible plastics—empower us to craft tailored parts for industries as diverse as aerospace, medical, and automotive. With tolerances as tight as ±0.005mm, ISO-certified quality assurance, and a commitment to design optimization, we ensure every part meets your exacting standards. Whether you need a single prototype in 24 hours or 100,000 production units, our scalable solutions, instant online quotes, and dedicated technical support make customization seamless. Choose Kesu—where innovation, precision, and reliability converge to bring your vision to life.
Conclusion
CNC service providers meet customized parts demands through advanced machining processes, material versatility, precision tolerances, and robust quality assurance. By leveraging cutting-edge technology and industry expertise, they deliver tailored solutions for diverse applications, from rapid prototypes to high-volume production. Their ability to optimize designs, maintain tight tolerances, and offer scalable manufacturing ensures clients receive high-quality, reliable parts that meet exact specifications.