Computer Numerical Control (CNC) machining is a cornerstone of modern manufacturing, enabling the production of high-precision components for industries ranging from aerospace to medical devices. Among the materials used, aluminum alloys are a preferred choice due to their exceptional combination of lightweight design, strength, and machinability. This article delves into the composition, properties, precision capabilities, and diverse applications of aluminum alloys in CNC machining, providing a comprehensive guide for manufacturers, engineers, and industry professionals seeking to optimize their production processes.
What Are Aluminum Alloys?
Aluminum alloys are materials primarily composed of aluminum, enhanced with alloying elements to achieve specific mechanical, physical, and chemical properties. These alloys are engineered to meet the rigorous demands of CNC machining, offering a balance of performance, cost, and manufacturability that makes them indispensable in precision manufacturing.
Composition and Classification
Pure aluminum is lightweight, highly corrosion-resistant, and ductile, but its low strength limits its use in demanding applications. By adding alloying elements, manufacturers create alloys with enhanced properties tailored to specific needs. Common alloying elements include:
- Copper: Increases strength and fatigue resistance, as seen in 2024 alloys used in aircraft structures.
- Magnesium: Enhances corrosion resistance and weldability, as in 5052 alloys for marine environments.
- Zinc: Boosts strength, as in 7075 alloys for high-performance aerospace components.
- Silicon: Improves castability and strength, as in 6061 alloys for structural applications.
- Manganese: Enhances workability and strength, often used in 3003 alloys for general-purpose applications.
Aluminum alloys are classified into two main categories: wrought and cast. Wrought alloys, such as 6061 and 7075, are preferred in CNC machining due to their superior workability and ability to be shaped through rolling, forging, or extrusion. Cast alloys, while used in molding, are less common in precision CNC due to their lower machinability. The Aluminum Association's four-digit system standardizes alloy identification, with series like 6XXX (silicon-magnesium) and 7XXX (zinc) widely used in CNC applications. These designations align with international standards, such as ASTM B211 and ISO 6361, ensuring global consistency.
Why Aluminum Alloys Matter in CNC Machining
Aluminum alloys are critical in CNC machining because they offer a unique combination of properties that enhance manufacturing efficiency and product performance. Their high machinability allows for faster cutting speeds and reduced tool wear, lowering production costs. Additionally, their diverse properties—ranging from high strength to excellent corrosion resistance—enable manufacturers to select the ideal alloy for specific applications, from lightweight aerospace components to durable marine fittings. The recyclability of aluminum further supports sustainable manufacturing practices, making it a preferred material in environmentally conscious industries.
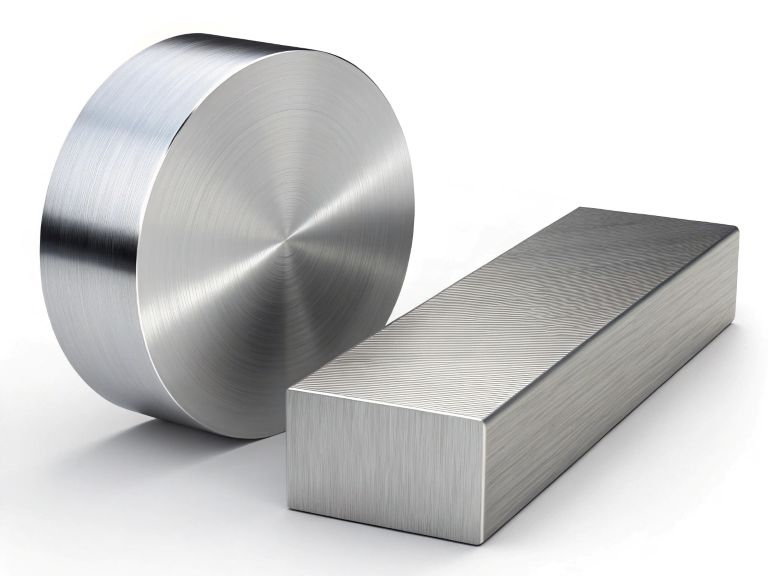
Properties of Aluminum Alloys for CNC Machining
The properties of aluminum alloys make them exceptionally suited for CNC machining, enabling the production of components with high precision and durability. These properties include physical characteristics, machinability, and the ability to customize alloys for specific needs.
Core Physical Characteristics
Aluminum alloys have a low density of approximately 2.7 g/cm³, making them one-third the weight of steel while maintaining significant strength. This high strength-to-weight ratio is critical for applications requiring lightweight yet robust components, such as aerospace and automotive parts. Their natural oxide layer provides excellent corrosion resistance, ideal for harsh environments like marine or chemical processing. Additionally, aluminum alloys offer superior thermal conductivity (e.g., 6061: ~167 W/m·K) and electrical conductivity, making them essential for heat sinks and electronic connectors.
Alloy Variants and Their Specific Properties
The choice of aluminum alloy depends on the application's requirements, with each variant offering unique properties. Below is a detailed overview of common alloys used in CNC machining:
- 6061: A versatile alloy with balanced strength (tensile strength: ~310 MPa), corrosion resistance, and weldability. It is widely used for structural components, such as automotive chassis and building frameworks.
- 7075: A high-strength alloy (tensile strength: ~570 MPa) with excellent fatigue resistance, ideal for aerospace components like wing spars and landing gear brackets. Its moderate corrosion resistance requires protective coatings in some environments.
- 2024: Known for high strength (tensile strength: ~470 MPa) and fatigue resistance, used in aircraft structures like fuselage skins. Its moderate corrosion resistance necessitates surface treatments.
- 5052: Offers excellent corrosion resistance and formability (tensile strength: ~230 MPa), suited for marine applications like hull fittings and chemical processing equipment.
- 5083: Provides exceptional strength and weldability (tensile strength: ~317 MPa), used in heavy-duty applications such as shipbuilding and pressure vessels.
- 2011: Optimized for machinability, with high cutting speeds and minimal tool wear, ideal for intricate parts like screws, bolts, and electronic fittings.
Tempering processes, such as T6 (solution heat-treated and artificially aged), further enhance properties like hardness, ductility, or fatigue resistance. For example, 6061-T6 offers improved strength and stability for structural applications.
Alloy | Tensile Strength (MPa) | Corrosion Resistance | Machinability | Typical Applications |
---|---|---|---|---|
6061 | 310 | High | Good | Structural components, engine blocks |
7075 | 570 | Moderate | Moderate | Aerospace parts, suspension arms |
2024 | 470 | Moderate | Good | Aircraft structures, wing ribs |
5052 | 230 | Excellent | Moderate | Marine fittings, chemical equipment |
5083 | 317 | Excellent | Moderate | Shipbuilding, pressure vessels |
Customization Through Alloying and Tempering
Beyond alloy selection, manufacturers can customize aluminum alloys through alloying and heat treatment. For instance, adding silicon to 6061 improves its castability, while T651 tempering reduces internal stresses for precision machining. These customization options allow engineers to fine-tune alloys for specific performance criteria, such as increased hardness for wear-resistant parts or enhanced ductility for complex geometries.
Achieving Precision in CNC Machining with Aluminum Alloys
Aluminum alloys are renowned for their ability to achieve high precision in CNC machining, thanks to their uniform material structure, low thermal expansion, and excellent machinability. These properties enable tight tolerances and intricate designs, critical for advanced manufacturing.
Why Aluminum Excels in Precision
Aluminum alloys' uniform microstructure minimizes warping or distortion during machining, ensuring dimensional stability. Their low thermal expansion coefficient (e.g., 6061: ~23.6 µm/m·°C) maintains accuracy across temperature variations, crucial for aerospace and electronics applications. Additionally, their high machinability allows for smooth cutting, reducing surface imperfections and enabling tolerances as tight as ±0.005 mm in advanced CNC setups.
Advanced CNC Techniques for Precision
Several CNC techniques leverage aluminum's properties to achieve exceptional precision:
- 5-Axis Machining: Enables simultaneous multi-angle cuts, ideal for complex geometries like turbine blades or aerospace fittings. This technique reduces setup times and improves accuracy for intricate parts.
- High-Speed Machining (HSM): Uses high spindle speeds (e.g., 20,000+ RPM) and optimized feed rates to minimize cycle times while maintaining surface quality, especially for thin-walled aluminum components.
- Micro-Machining: Achieves sub-micron precision for small, detailed parts like electronic connectors or medical implants, leveraging aluminum's machinability for fine features.
- Cryogenic Cooling: Uses liquid nitrogen to minimize heat-induced distortion, ensuring accuracy in high-precision applications like optical components.
- Electrical Discharge Machining (EDM): Employed for hard alloys like 7075, creating intricate features like mold inserts with minimal material stress.
Tooling plays a critical role, with carbide or diamond-coated tools used to handle aluminum's abrasiveness. Advanced CAD/CAM software optimizes toolpaths, reducing material waste and ensuring precision. Quality control measures, such as Coordinate Measuring Machines (CMM) and laser scanning, verify tolerances and surface finishes (e.g., Ra 0.4 µm) for both functional and aesthetic components.
Case Study: Precision Aerospace Component
A practical example is a landing gear bracket machined from 7075-T6 aluminum using 5-axis CNC machining. The component required tolerances of ±0.01 mm and a surface finish of Ra 0.8 µm to ensure structural integrity and fatigue resistance. By employing high-speed machining and cryogenic cooling, the manufacturer achieved the required precision, with CMM verification confirming compliance with aerospace standards like AS9100.

Applications of Aluminum Alloys in CNC Machining
Aluminum alloys are integral to numerous industries, producing specific, high-performance products that leverage their lightweight, strength, and corrosion resistance. Below are detailed examples across key sectors.
Aerospace Applications
The aerospace industry relies on aluminum alloys for their strength-to-weight ratio and precision:
- Wing Ribs (2024, 7075): Structural components that support aircraft wings, requiring high strength and fatigue resistance for safety and longevity.
- Engine Housings (6061): Lightweight, heat-resistant casings for jet engines, machined to precise tolerances for thermal efficiency.
- Satellite Frames (7075): Precision-machined structures that minimize weight while maintaining rigidity for space applications.
- Fuselage Panels (2024): Thin, durable panels that form the aircraft's outer skin, balancing strength and aerodynamics.
Automotive Applications
Aluminum alloys enhance vehicle performance and efficiency:
- Engine Blocks (6061): Lightweight and thermally conductive, used in internal combustion engines and electric vehicle (EV) motors to reduce weight and improve fuel efficiency.
- Suspension Arms (7075): High-strength components for performance vehicles, offering durability under dynamic loads.
- Battery Trays for EVs (5083): Corrosion-resistant enclosures that protect lithium-ion batteries in electric vehicles, ensuring safety and longevity.
- Wheel Rims (6061): Lightweight, aesthetically finished rims that enhance vehicle handling and fuel economy.
Electronics Applications
Aluminum alloys support precision and thermal management in electronics:
- Heat Sinks (6061): Efficiently dissipate heat from CPUs, GPUs, and LED systems, machined to maximize surface area and thermal conductivity.
- Smartphone Frames (7075): Thin, durable casings for premium devices like iPhones, offering strength and a premium finish.
- Connector Housings (2011): Intricate, high-precision parts for USB, HDMI, or RF connectors, leveraging 2011's machinability.
- Laptop Chassis (6061): Lightweight, rigid enclosures that protect internal components while maintaining portability.
Medical, Marine, and Industrial Applications
Aluminum alloys are also critical in specialized sectors:
- Surgical Instruments (5052): Corrosion-resistant tools like forceps, scalpels, and retractors, machined for precision and biocompatibility.
- MRI Scanner Components (6061): Non-magnetic, lightweight parts for imaging systems, ensuring safety and accuracy.
- Propeller Shafts (5083): Durable, corrosion-resistant components for marine vessels, withstanding saltwater exposure.
- Robotic Arms (6061): Lightweight, precise components for industrial automation, enabling high-speed and accurate movements.
CNC Machining Processes for Aluminum Alloys
CNC machining encompasses a range of processes tailored to aluminum alloys' properties, ensuring precision, efficiency, and quality in component production.
Primary Machining Processes
Key CNC processes for aluminum alloys include:
- Milling: Face milling creates flat surfaces for aerospace panels, while pocket milling forms cavities for automotive parts. High-helix end mills optimize chip evacuation.
- Turning: Precision lathe operations produce cylindrical components like shafts, fittings, or fasteners. Thread cutting is used for screws and connectors in electronics.
- Drilling: High-speed drilling creates bolt holes in structural components, while deep-hole drilling forms fluid channels in engine parts.
Specialized and Finishing Processes
Additional processes enhance precision and functionality:
- Grinding: Surface grinding achieves ultra-smooth finishes (e.g., Ra 0.2 µm) for medical tools, improving aesthetics and functionality.
- Anodizing: Post-machining anodizing enhances corrosion resistance and adds aesthetic finishes, common for smartphone frames and marine fittings.
- Laser Cutting: Precision cutting of thin aluminum sheets for electronics enclosures or decorative panels, offering clean edges and minimal waste.
- Electrical Discharge Machining (EDM): Used for intricate features in hard alloys like 7075, such as mold inserts or aerospace components.
Process optimization is critical, with adaptive control systems adjusting feed rates and spindle speeds to suit aluminum's properties. Coolant systems (e.g., mist or flood cooling) manage heat and chip evacuation, preventing tool damage and ensuring surface quality.
Tooling and Optimization
Carbide or diamond-coated tools are essential for machining aluminum, with high-helix geometries reducing burr formation. Chip breakers and high-pressure coolant systems address aluminum's tendency to form long, stringy chips. Regular tool maintenance and advanced CNC programming ensure consistent performance, minimizing downtime and maximizing throughput.
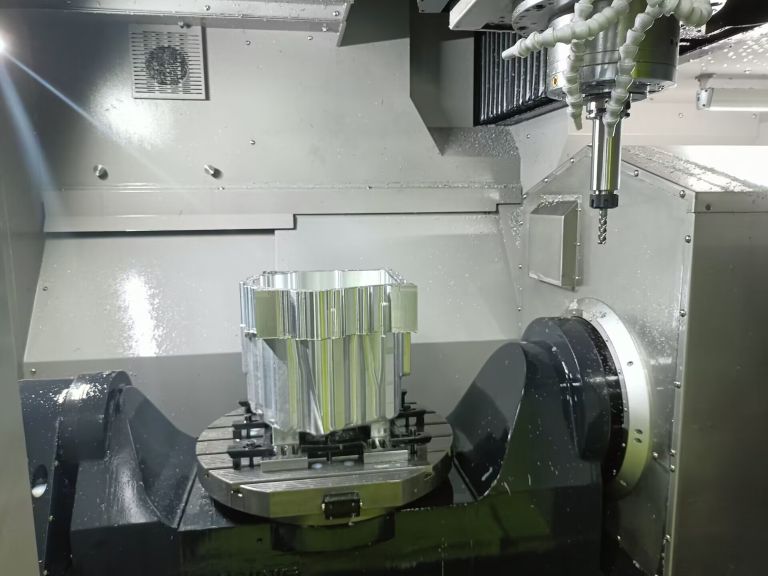
Advantages and Challenges of Aluminum Alloys in CNC Machining
Aluminum alloys offer significant advantages but also present challenges that require careful management.
Advantages
Key benefits include:
- Lightweight Design: Reduces energy consumption in aerospace and automotive applications, improving fuel efficiency and performance.
- Recyclability: Supports sustainable manufacturing, with aluminum being 100% recyclable without loss of properties.
- Versatility: A wide range of alloys allows tailored solutions for diverse applications, from high-strength aerospace parts to corrosion-resistant marine components.
- Cost-Effectiveness: High machinability reduces production costs through faster cycle times and lower tool wear.
Challenges and Solutions
Challenges include:
- Burr Formation: Soft alloys like 6061 may produce burrs, addressed with optimized tool geometries (e.g., high-helix end mills) and finishing processes.
- Tool Wear: High-strength alloys like 7075 are abrasive, requiring durable tools like diamond-coated cutters and regular maintenance.
- Chip Management: Aluminum's stringy chips can clog machines, mitigated by chip breakers and high-pressure coolant systems.
By addressing these challenges, manufacturers can fully leverage aluminum alloys' benefits, ensuring high-quality, cost-effective production.
Conclusion
Aluminum alloys are a cornerstone of CNC machining, offering a unique combination of precision, properties, and applications. From their tailored composition to their ability to achieve tight tolerances, these materials drive innovation across industries like aerospace, automotive, electronics, and medical manufacturing. By selecting the right alloy, employing advanced CNC techniques, and addressing machining challenges, manufacturers can produce high-performance components that meet global standards. As industries continue to demand lightweight, durable, and sustainable solutions, aluminum alloys will remain at the forefront of precision manufacturing.
FAQ: Aluminum Alloys in CNC Machining
What are aluminum alloys, and why are they used in CNC machining?
Aluminum alloys are materials made by combining aluminum with elements like copper, magnesium, or zinc to enhance properties like strength and corrosion resistance. They are used in CNC machining for their lightweight, high machinability, and versatility, making them ideal for producing precise components in aerospace, automotive, and electronics.
Which aluminum alloy is best for CNC machining?
The best alloy depends on the application. For example, 6061 is versatile for structural parts, 7075 offers high strength for aerospace components, 5052 excels in corrosion resistance for marine applications, and 2011 is optimized for intricate, machinable parts like fasteners.
How does CNC machining achieve precision with aluminum alloys?
Precision is achieved through techniques like 5-axis machining, high-speed machining, micro-machining, and cryogenic cooling. Advanced tools, CAD/CAM software, and quality control systems like CMM ensure tolerances as tight as ±0.005 mm and smooth surface finishes.
What are the challenges of machining aluminum alloys?
Challenges include burr formation in soft alloys, tool wear in high-strength alloys, and chip management due to stringy chips. These are addressed with optimized tool geometries, durable cutters, chip breakers, and effective coolant systems.