Numerical Control (CNC) machining is critical in aerospace manufacturing, particularly for complex components like fuel pump housing parts. These parts, characterized by intricate shapes and long processing cycles, are vital to meeting stringent quality and precision standards. However, despite the widespread adoption of advanced CNC equipment, achieving high productivity remains challenging. This article examines the factors contributing to inefficiencies in CNC machining, based on a case study from a leading aerospace company, and outlines practical solutions to enhance equipment efficiency. By addressing equipment downtime, preparation time, and cutting efficiency, the company achieved a 79.2% capacity increase from 2014 to 2025 without adding equipment or personnel.
Analyzing Equipment Downtime
Equipment downtime is a primary factor limiting CNC machining efficiency. A detailed study of two key machines, DMU60P and DMU80P, over 316 hours across 20 working days revealed 189.8 hours of downtime, with 1,160 stoppage events recorded. The analysis categorized downtime into three types: stoppage losses, speed losses, and planned downtime.
The breakdown of downtime is as follows:
Category | Activities | Time (Hours) | Percentage of Total Downtime |
---|---|---|---|
Stoppage Losses | Changeover, measurement, production preparation, equipment failure | 114.1 | 60.1% |
Speed Losses | Blank inspection, measurement, chip removal, fixture adjustment, program execution | 53.7 | 28.3% |
Planned Downtime | Maintenance, shift handovers, production meetings | 21.8 | 11.5% |
Stoppage losses, particularly from changeovers and equipment failures, were the largest contributors to inefficiency. Speed losses, such as time spent on chip removal and fixture adjustments, also significantly impacted productivity. Planned downtime, while necessary, was a smaller factor but still required optimization.
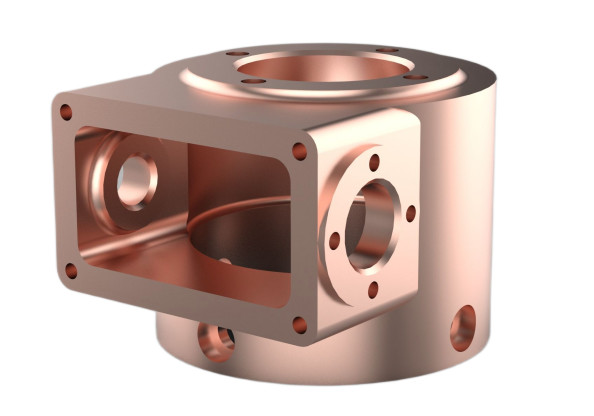
Strategies to Reduce Downtime
Reducing downtime is essential to improving CNC equipment efficiency. The following strategies were implemented to address non-planned downtime and enhance equipment availability.
Minimizing Non-Planned Downtime
Fuel pump housing parts involve over 200 machining operations, often leading to inter-process interference and unplanned stops. To mitigate this, production planning was refined through weekly team reviews conducted three days in advance. This process involved assessing machining status, adjusting task schedules, and ensuring seamless workflow. As a result, non-planned downtime due to process conflicts was significantly reduced.
Equipment failures were another major contributor to downtime. To address this, a Total Productive Maintenance (TPM) approach was adopted, involving seven steps: cleaning, inspection, lubrication, tightening, adjustment, standardization, and autonomous maintenance. Regular maintenance schedules and proactive fault prevention reduced failure rates and extended equipment runtime.
Optimizing Preparation Time
Preparation time, encompassing fixture setup, tool preparation, program loading, measurement, and quality inspections, is unavoidable but can be minimized. The following measures were implemented to streamline preparation processes.
Reducing Fixture Setup Time
Fixtures ensure consistent part positioning and stability during machining. Traditional fixtures, designed for specific operations, required lengthy adjustments during changeovers, increasing preparation time. To address this, a zero-point positioning system was introduced, featuring interchangeable and universal fixture bases. This system standardized machining zero points, enabling seamless fixture transitions and reducing setup time while improving accuracy.
Streamlining Tool Preparation
Tool preparation for housing parts, which primarily involve hole machining, was time-intensive due to the variety of tools required. Previously, tool changeovers took approximately 120 minutes per operation, calculated as:
Tool Changeover Time = (Tool Identification + Disassembly + Installation + Data Input) × Average Tools per Operation + Repeated Adjustments ≈ 4 min × 25 tools + 20 min ≈ 120 min
To reduce this, tools were categorized into Type I (high-frequency, universal) and Type II (low-frequency, operation-specific). Type I tools were fixed in the machine, while Type II tools were stored in an on-site secondary tool library with pre-marked parameters and lifespan tracking. This reduced tool changeover time to 25 minutes per operation, calculated as:
Tool Changeover Time = (Tool Identification + Disassembly + Installation + Data Input) × Average Tools per Operation ≈ 2.5 min × 10 tools ≈ 25 min
Improving Program Preparation
Program preparation involves coding tool paths for machining operations. For housing parts, programs were tailored to hole dimensions and positions. To minimize errors, a program solidification process was implemented. First-piece parts underwent full-dimensional inspections, and validated programs were stored in a Distributed Numerical Control (DNC) system for direct transmission to machines, reducing programming errors and preparation time.
Reducing Measurement Wait Times
Measurement of complex housing parts, particularly for angled holes, was time-consuming, averaging 240–480 minutes per operation. By integrating zero-point positioning with digital measurement programming, parts were measured with their fixtures intact, and automated inspection routines reduced measurement time to 30–60 minutes, a 75–87.5% reduction.
Optimizing Quality Inspections
Quality inspections, involving self-inspection, cross-inspection, and professional inspection, were labor-intensive, with 200–400 dimensions checked per operation. Manual recording often led to omissions. An electronic inspection sheet was introduced, standardizing and digitizing inspection data to eliminate errors and reduce inspection time.
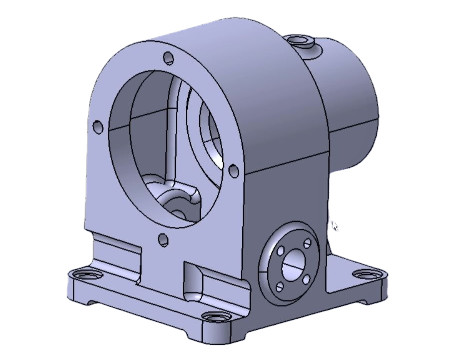
Enhancing Cutting Efficiency
Cutting efficiency directly impacts machining cycle times. Housing parts undergo roughing, semi-finishing, and finishing, with 85% of operations performed on machining centers. To meet increasing production demands, single-operation cutting times were reduced through the following methods.
Optimizing Cutting Parameters and Tool Matching
Hard alloy tools, common in CNC machining, offer high hardness and cutting efficiency but require precise parameter matching. Analysis revealed suboptimal parameter-tool alignment, reducing efficiency. Collaboration with tool manufacturers established a cutting parameter database tailored to aerospace aluminum materials, with feed rates of 0.1–0.15 mm/z, improving tool performance and output.
Minimizing Non-Cutting Tool Movements
Non-cutting movements, such as tool retractions and repositioning, were identified as inefficiencies. Key issues included:
- Excessive Tool Changes: Traditional sequential hole machining led to redundant tool calls. By processing all applicable features with a single tool before switching, tool changes were reduced by 30%, cutting machining time by over 10%.
- Long Approach/Retraction Distances: Programs had excessive safety distances (5–10 mm), which were shortened to 1–2 mm, reducing movement waste.
- Frequent Horizontal-Vertical Transitions: Five-axis machining required posture changes for angled holes. Consolidating horizontal and vertical operations minimized transitions, shortening cycle times.
Reducing Program Interruptions
Program interruptions (M0 codes) for manual alignment increased downtime. By incorporating automatic probe-based alignment, interruptions were minimized, ensuring continuous machining and improving efficiency.
These optimizations were applied to four housing parts, reducing single-operation times by an average of 27.23%, as shown below:
Part | Operations Optimized | Average Time Reduction (%) |
---|---|---|
Housing 1 | 6 | 28.5 |
Housing 2 | 5 | 26.8 |
Housing 3 | 7 | 27.0 |
Housing 4 | 5 | 26.6 |
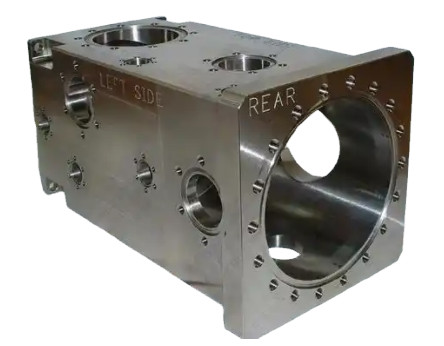
Results and Impact
By addressing downtime, preparation time, and cutting efficiency, the company significantly improved CNC machining productivity. From 2014 to 2025, with no additional equipment or personnel, annual part deliveries increased from 159 to 285 units, a 79.2% capacity improvement. These measures ensured consistent quality, reliable output, and the ability to meet growing customer demands, providing a replicable model for aerospace manufacturers facing similar inefficiencies.